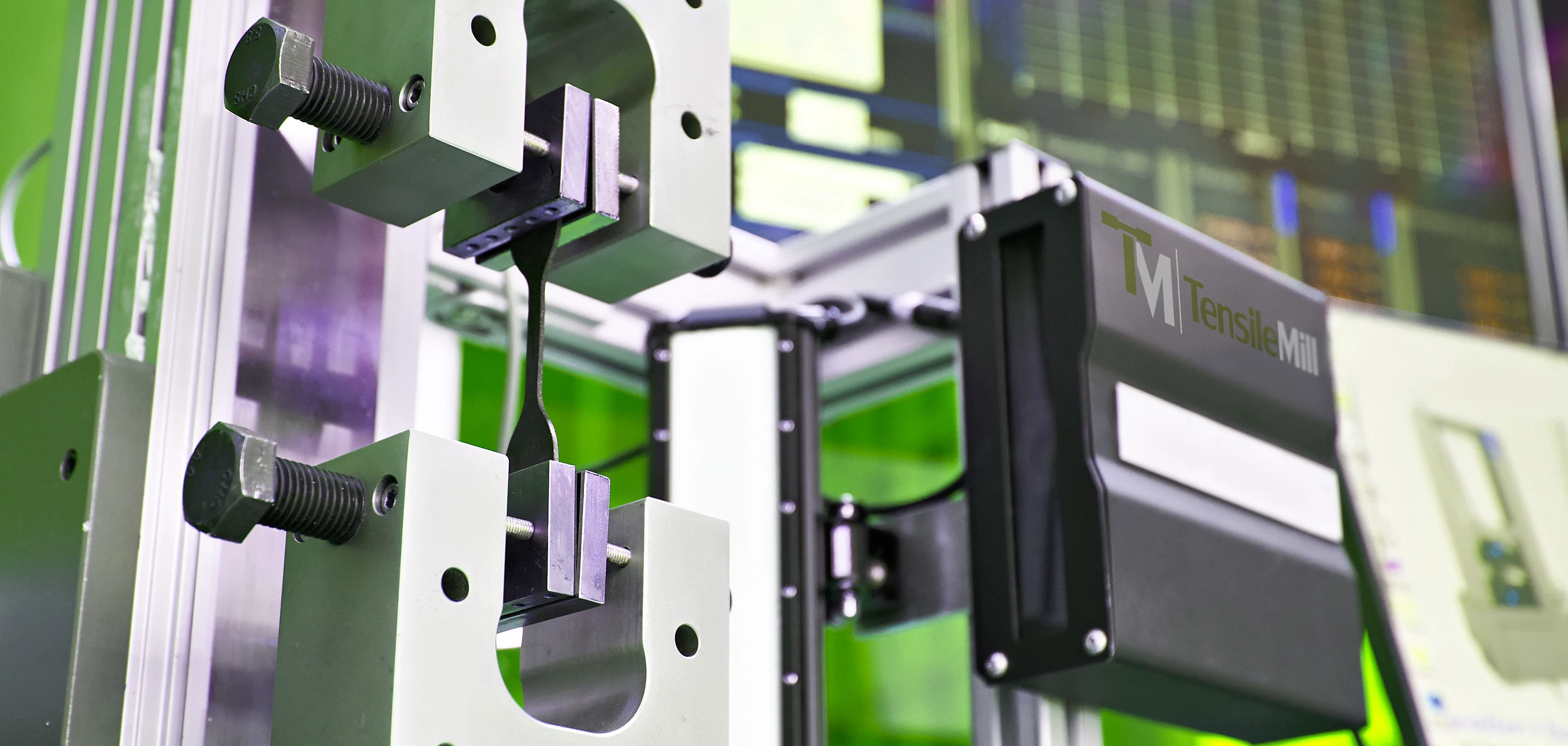
Tensile testing in Research and Development measures a material's mechanical properties under tension. This testing method allows scientists and engineers to identify the strength, flexibility, and elasticity of newly developed and existing materials, verifying they meet specific standards and quality requirements. By accurately assessing these properties, tensile testing aids in product innovation and enhancement for many industries. It is necessary not only for developing safer and more efficient materials but also for driving technological advancements and maintaining competitive edges in rapidly evolving markets.
Tensile testing is continually evolving as an important aspect of material testing, experiencing notable technological advancements each year. This evolution introduces advanced machines capable of producing tensile specimens in diverse shapes and materials, alongside modern Universal Testing Machines (UTMs) designed to handle any testing requirement.
Tensile testing is also becoming increasingly popular, not just in large industries, but also among small startups to assess the materials for their products. Moreover, this is particularly significant in research and development within organizations, industries, and academia. Among other benefits like cost-efficiency and reliability, testing for tensile strength can provide peace of mind for both manufacturers and people, as this method can guarantee the quality of the end product.
Today, we will discuss tensile testing in Research and Development in 2024, focusing on current trends and future expectations for this field. We aim to provide insights into how the tensile test is shaping up this year and its implications for material innovation and quality assurance in the field of Research and Development.
Understanding Research and Development
Research and Development (R&D) is a key driver of innovation in both the public and private sectors, shaping industries' future and propelling economic growth. R&D involves basic and applied research. Basic research explores fundamental principles without a direct commercial objective, often leading to unexpected applications, while applied research targets specific goals, aiming to develop new products or refine existing processes.
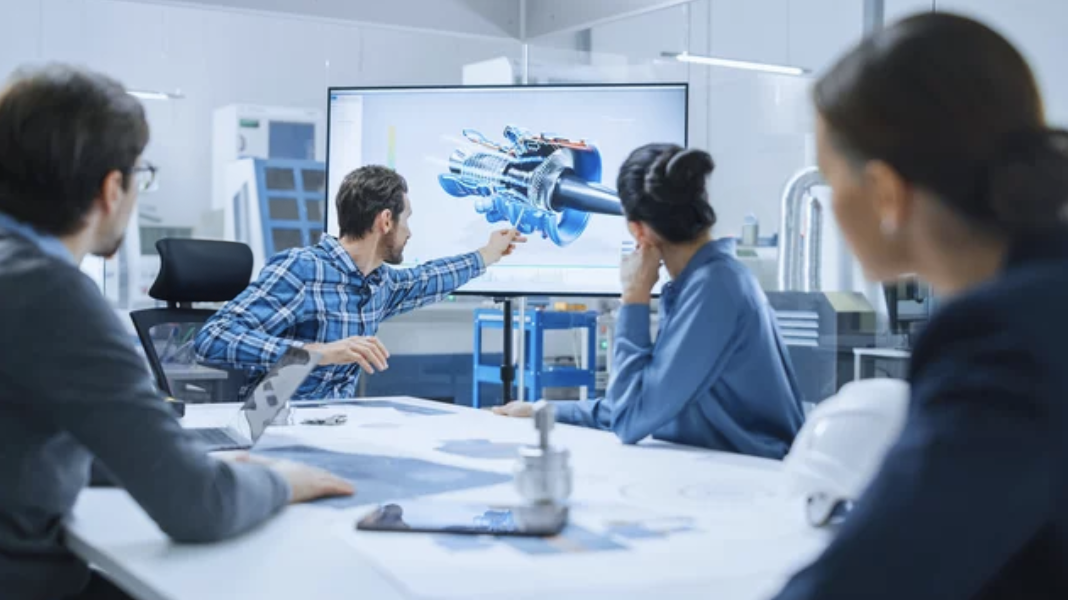
R&D is an integral part of many domains including technology, healthcare, and manufacturing, contributing to advancements that can significantly alter market dynamics. Manufacturing, for example, requires R&D to verify the properties and performance of materials intended for product development. This process involves detailed testing protocols to verify that materials conform to required standards for durability, safety, and functionality before integration into final products. Effective verification processes prevent costly recalls, boost product reliability, and strengthen consumer trust.
Industries invest in R&D to remain competitive. The process typically starts with an idea in a laboratory setting, progresses through stages of prototype development, and culminates in the production and market launch of a new or improved product. This structured approach provides assurance that scientific breakthroughs transition effectively from theory to practical applications, meeting market needs and consumer demands.
Governmental bodies also recognize the importance of R&D, often providing funding and support to foster an environment conducive to research breakthroughs and innovation. This support not only accelerates technological advancements but also addresses broader societal challenges, increasing national competitiveness on a global scale.
The Role of Tensile Testing in R&D
Tensile testing is a key component of R&D for advancing material science and engineering innovations. It serves a number of important functions aimed at optimizing materials development and application in a range of industries.
Primarily, testing for tensile properties in R&D helps characterize the mechanical characteristics of novel materials or modified versions of existing materials. This is an essential step because understanding these properties - such as tensile strength, elongation, yield strength, and Young's modulus - allows scientists and engineers to predict how materials will behave under different stress conditions in real-world applications. Such predictions are vital for guaranteeing safety, efficiency, and effectiveness in product design and application.
Furthermore, tensile testing helps validate theoretical models developed during material research. By comparing experimental results with predicted outcomes, researchers can verify the accuracy of their models and make necessary adjustments to their theories, leading to more reliable and practical solutions for material applications.
Testing tensile strength is also necessary for material selection in product development. Engineers rely on data from tensile tests to choose appropriate materials that meet the specific requirements of their projects, such as durability, flexibility, and strength. This selection process is fundamental in sectors like aerospace, automotive, construction, and healthcare, where material performance can directly impact the functionality and safety of the final products.
Moreover, tensile tests play a key role in quality control and assurance in manufacturing. By routinely testing materials for their tensile properties, manufacturers can maintain high standards, making certain that all products meet the required specifications before they reach the market. This systematic testing helps minimize the risk of failures and increases consumer trust in the products offered.
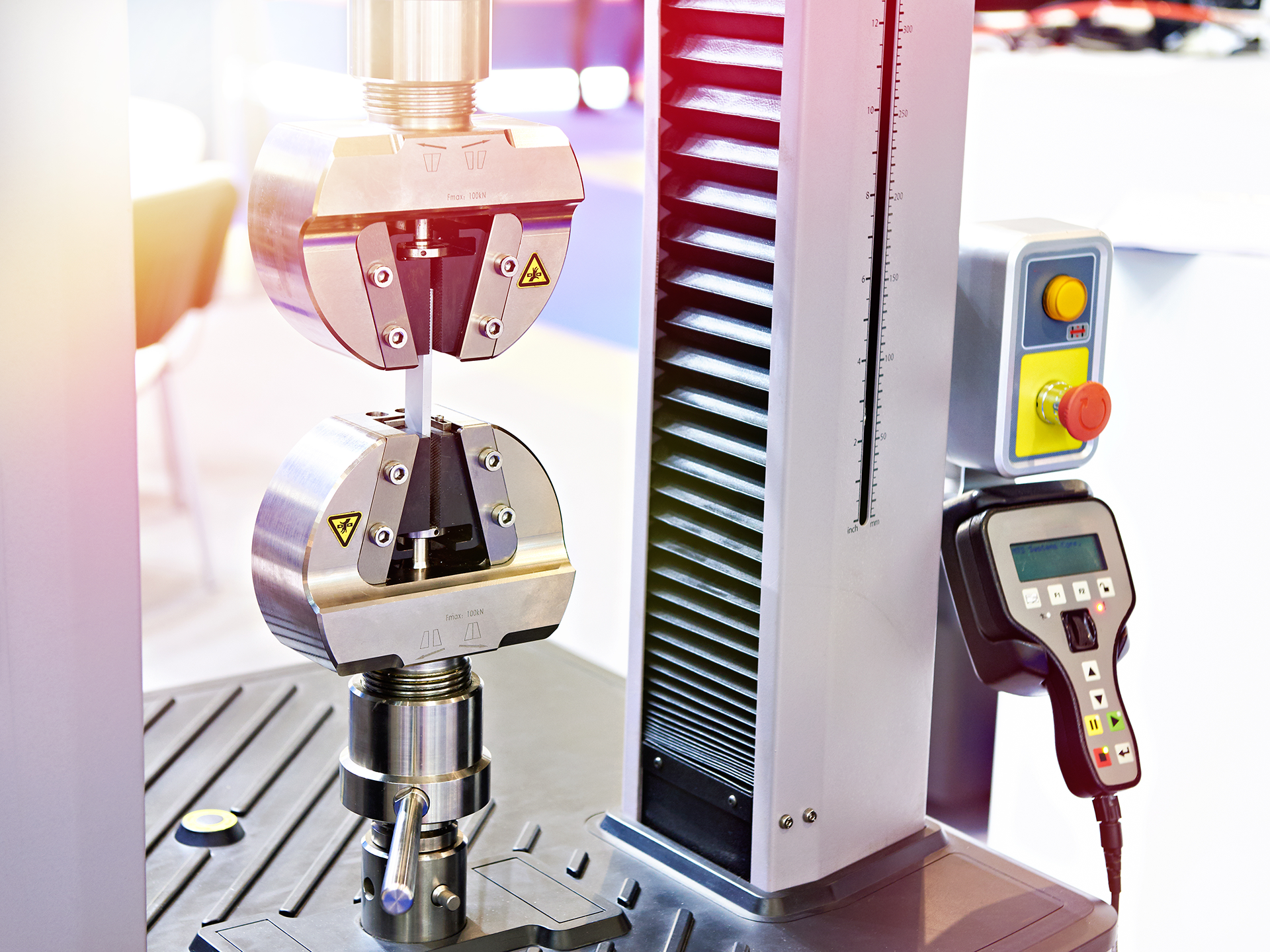
Advances in Tensile Testing in the Recent and Future
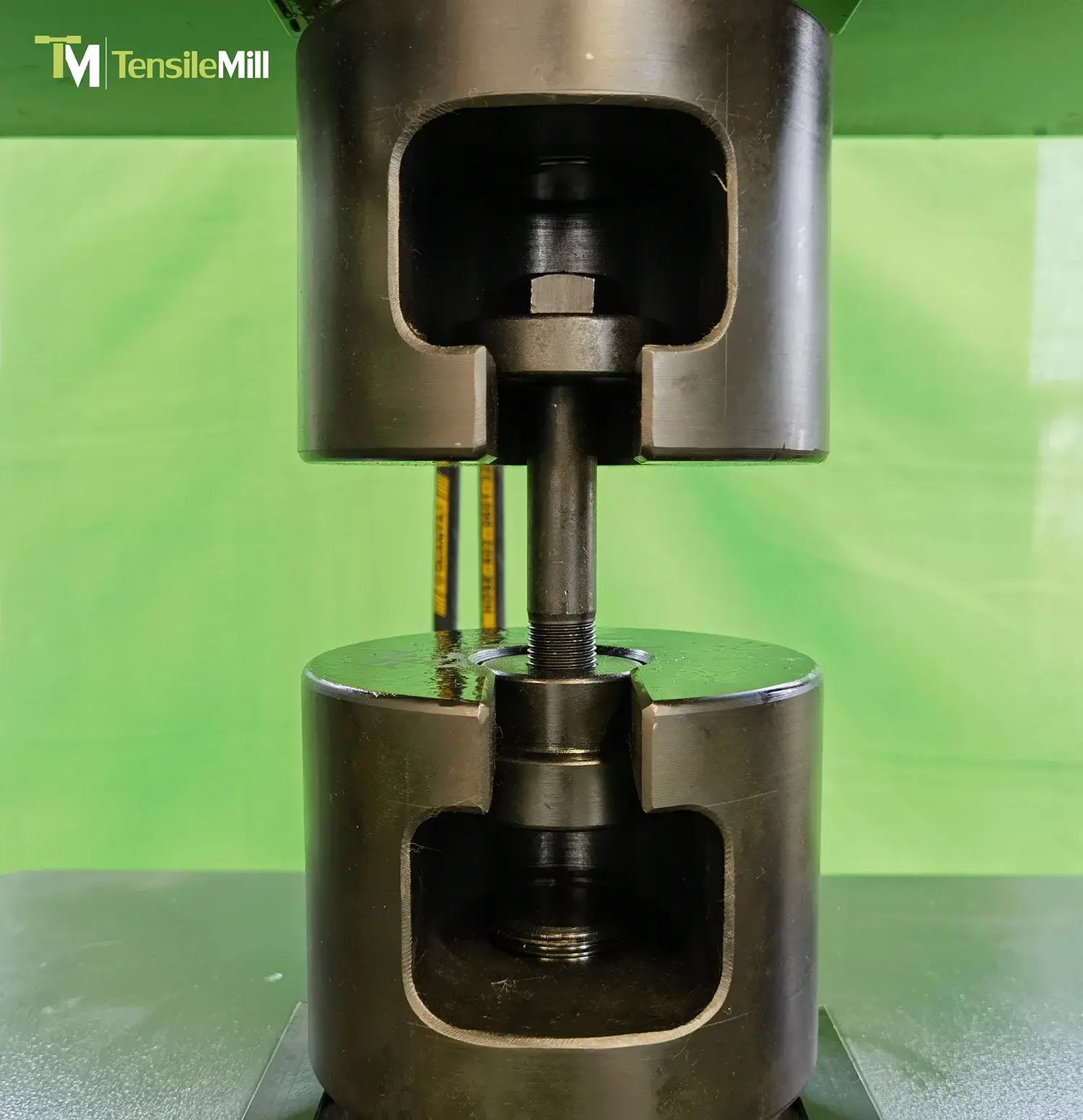
Tensile testing is continually evolving, as we stated at the beginning of this article. Recent advancements in tensile tests have been marked by a number of technological innovations, which have increased the precision, efficiency, and application scope of these tests. One of the most notable trends is the integration of automation and advanced technologies such as artificial intelligence (AI) and machine learning. These technologies have transformed tensile testing by improving test results accuracy and reducing human error, particularly in high-volume testing conditions. Automated systems can now conduct tests with minimal human interference, allowing data to be produced consistently and reliably.
Looking toward the future, tensile testing is set to advance greatly with new machine capabilities and cutting-edge technologies. One prominent development is the increasing integration of digital and automated technologies, which notably increases tensile test accuracy and efficiency. These advancements allow for more sophisticated data acquisition and analysis, a necessity for industries requiring high precision.
Additionally, there is a trend towards more universal tensile testing systems that can handle a greater variety of materials, including high-capacity machines capable of assessing forces up to 2000 kN. These machines are extremely useful for testing advanced materials' mechanical properties under more extreme conditions. This broadens the scope of applications in an array of fields from construction to high-performance engineering materials.
Implications for R&D
The benefits of these advancements in tensile testing are particularly valuable for Research and Development. Improved testing capabilities allow for a more statistically precise assessment of material properties under varying conditions. Furthermore, the precision and efficiency gained through automation and advanced technologies accelerate R&D processes, enabling faster turnaround times from material development to market readiness.
Moreover, the ability to test a broad range of materials with greater accuracy supports product customization to meet specific customer needs and industry standards. A high level of adaptability is essential for maintaining competitiveness in ever-changing industries.
High-Tech Tensile Testing Equipment in R&D Labs
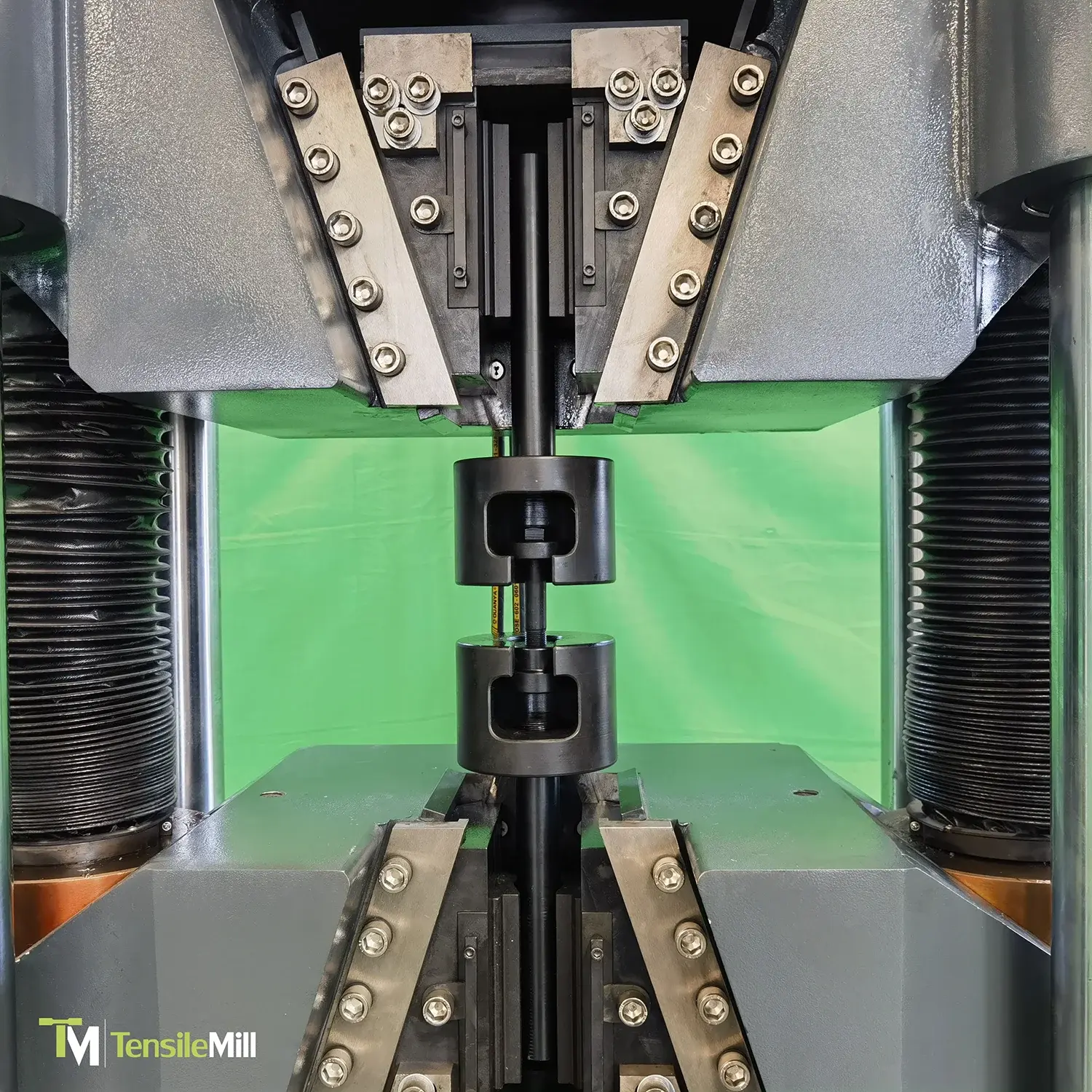
As we mentioned the UTMs above, it is relevant to note that our company, specializing in tensile testing and tensile sample preparation, offers equipment that supports an array of applications - from quality assurance in manufacturing to the stringent demands of Research and Development.
Our state-of-the-art tensile testing machines are designed to cater to the specific needs of different industries, enabling precise measurement and analysis of material properties under tension.
In order to gain a better understanding of how our tools can benefit Research and Development, we will take a closer look at a few of our UTM for tensile testing.
Servo Hydraulic Universal Testing Systems NG-SHM600 and NG-SHM1000
Researchers and developers will find the NG-SHM600 Class A and the NG-SHM1000 Class A highly versatile and robust solutions that meet the rigorous requirements of material testing for many types of industries. Engineered for precision, these systems offer a capacity range of 600kN to 1000kN. These include tension, compression, shearing, and bending tests.
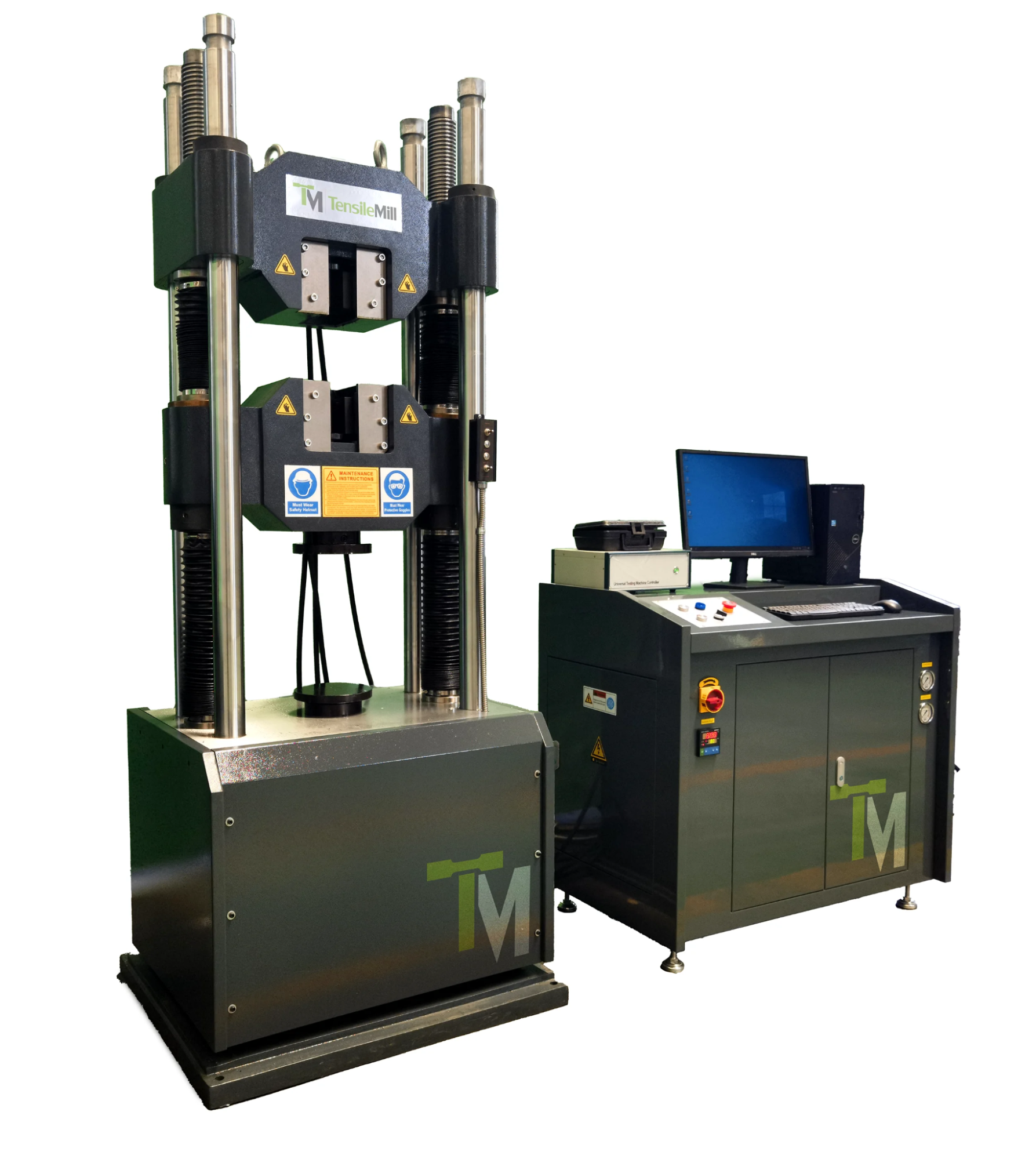
These tools are specifically designed to comply with a multitude of international standards such as ASTM E8, ISO 6892, and BS 4449, allowing applicability globally in different regulatory environments. This compliance guarantees that materials tested under these standards meet the highest criteria for strength, durability, and performance.
Constructed with a robust four-column and two-lead screw structure, the NG-SHM600 and NG-SHM1000 enhance durability and stability during high-force testing situations. The inclusion of a hydraulic-operated tensile grip simplifies the operation process, while the dual testing space configuration allows for easy switching between tensile and compression tests without reconfiguring the setup.
Accuracy is key to any testing process. With these systems, testing force is directly measured using a load cell, offering precision down to 0.5%. The user-friendly interface of the EVOTest software, compatible with modern Windows versions, offers an intuitive experience with features such as real-time graphical representations of stress-strain curves and customizable test modules.
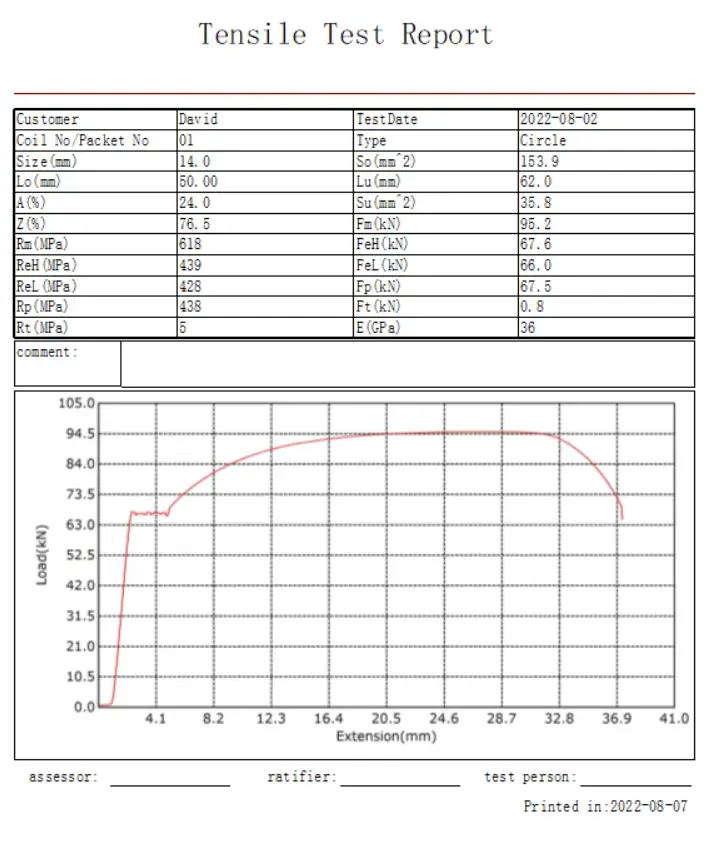
Servo Hydraulic Universal Testing Machine 2000kN
As our second featured product in the lineup, the Servo Hydraulic Universal Testing Machine 2000kN represents a robust and highly reliable solution for advanced material testing. This machine is designed to meet rigorous international standards such as ASTM E4 and ISO 750001, which means that it will be compatible with all of the global testing protocols.
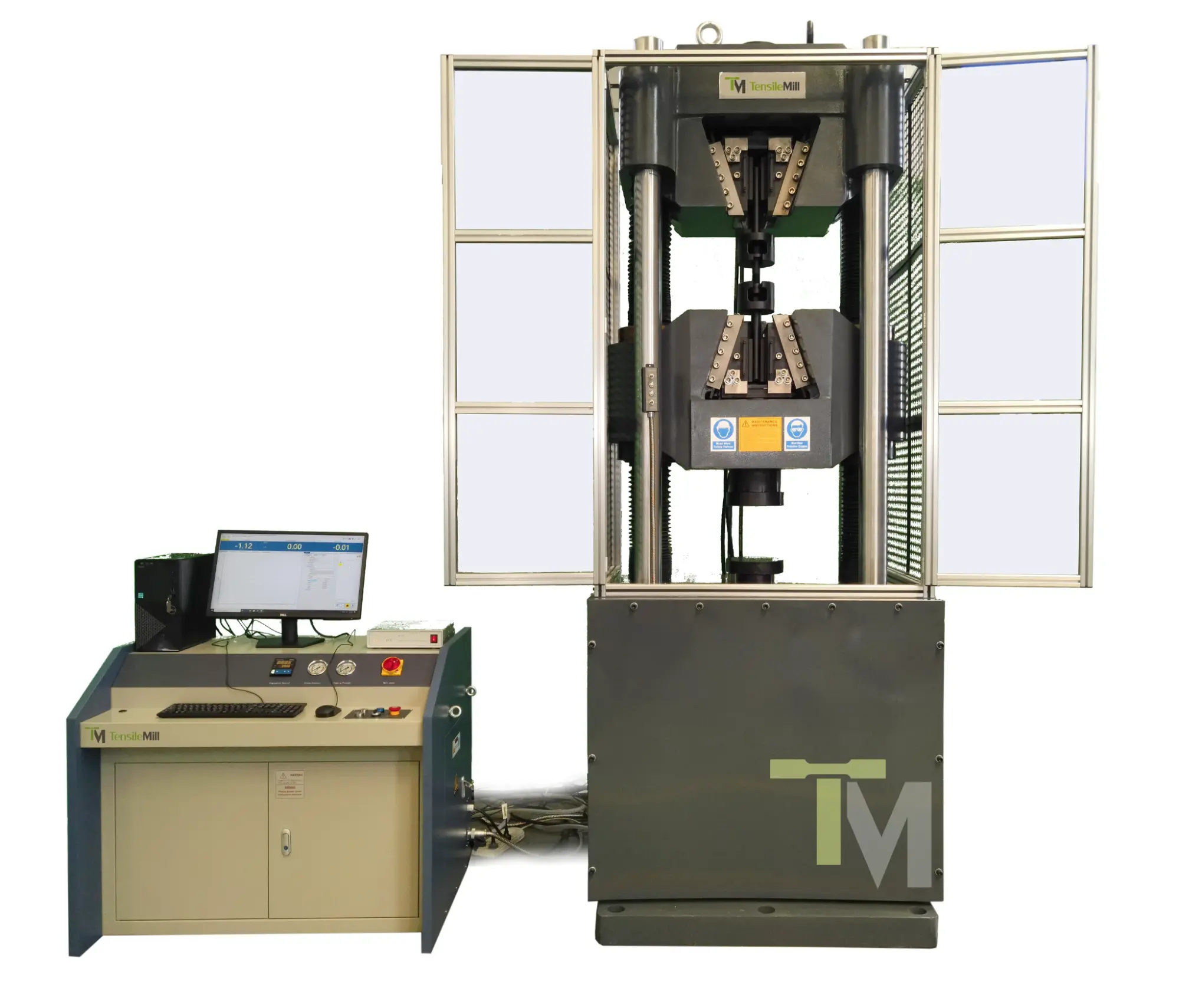
Primarily used for testing the tensile strength and mechanical properties of fasteners like bolts and nuts, this machine is a staple in both laboratory and industrial quality control environments. The machine's capabilities are highly relevant for high-grade bolt specifications ranging from M6 to M56, including grades 8.8, 10.9, and 12.9.
Featuring a precision Italian ATOS servo valve hydraulic power pack, the machine provides complete control over the loading process. It features a high-precision load cell for measuring testing force and a photoelectric encoder for displacement measurement, supporting a three-closed-loop control system - load, displacement, and strain. As a result, tests are performed under constant loading rates, displacement, or strain, which enhances the accuracy of the results.
The machine's dual test space setup allows for efficient switching between tensile and compression tests, maximizing testing throughput without sacrificing accuracy. The operation is further streamlined by Maxtest testing software, a powerful testing tool that can be used with different types of material testing machines and extensometers, such as clip-on, large travel, and video extensometers.
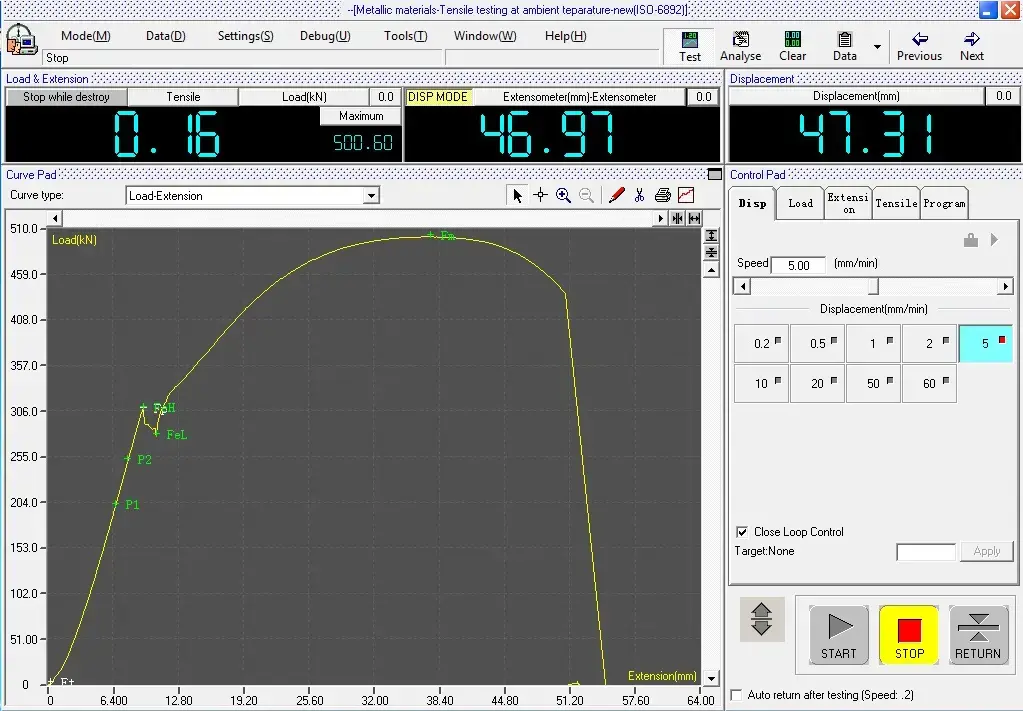
The Value of Tensile Testing in Industry-Specific R&D
R&D is the backbone of innovation in many fields. It adapts to unique challenges and evolving needs. It is a dynamic field, not isolated within a singular framework but expansive, stretching over different industrial landscapes. Each industry customizes its R&D efforts to foster advancements that propel its specific products forward and also meet increasingly stringent regulatory standards and consumer expectations.
The Research and Development domain is responsible for driving the progress from conceptual design to the realization of the final product. In this context tensile testing becomes one of the most important quality inspection tools that can be used to verify the highest.
The demand for more complex and reliable materials increases as industries pursue innovation. Tensile testing assists in this pursuit by guaranteeing that materials perform optimally under varying stress conditions. Whether applied to aerospace high-performance alloys, durable polymers in automotive manufacturing, or robust fabrics in textile applications.
Within the most prevalent R&D fields in industries, we will explore the specific roles and applications of tensile testing, along with the materials they test. The focus of this exploration is how tensile testing supports the development of safer, more efficient, and more durable products across the board, not just as a procedure.
Aerospace Industry
In the aerospace industry, tensile testing is extremely important, not only for routine material properties verification but also for guaranteeing the highest level of safety and functionality of components under extreme conditions. Although not the largest user of tensile testing, the aerospace industry's reliance on this testing method is among the most significant due to the high financial stakes and human safety concerns involved.
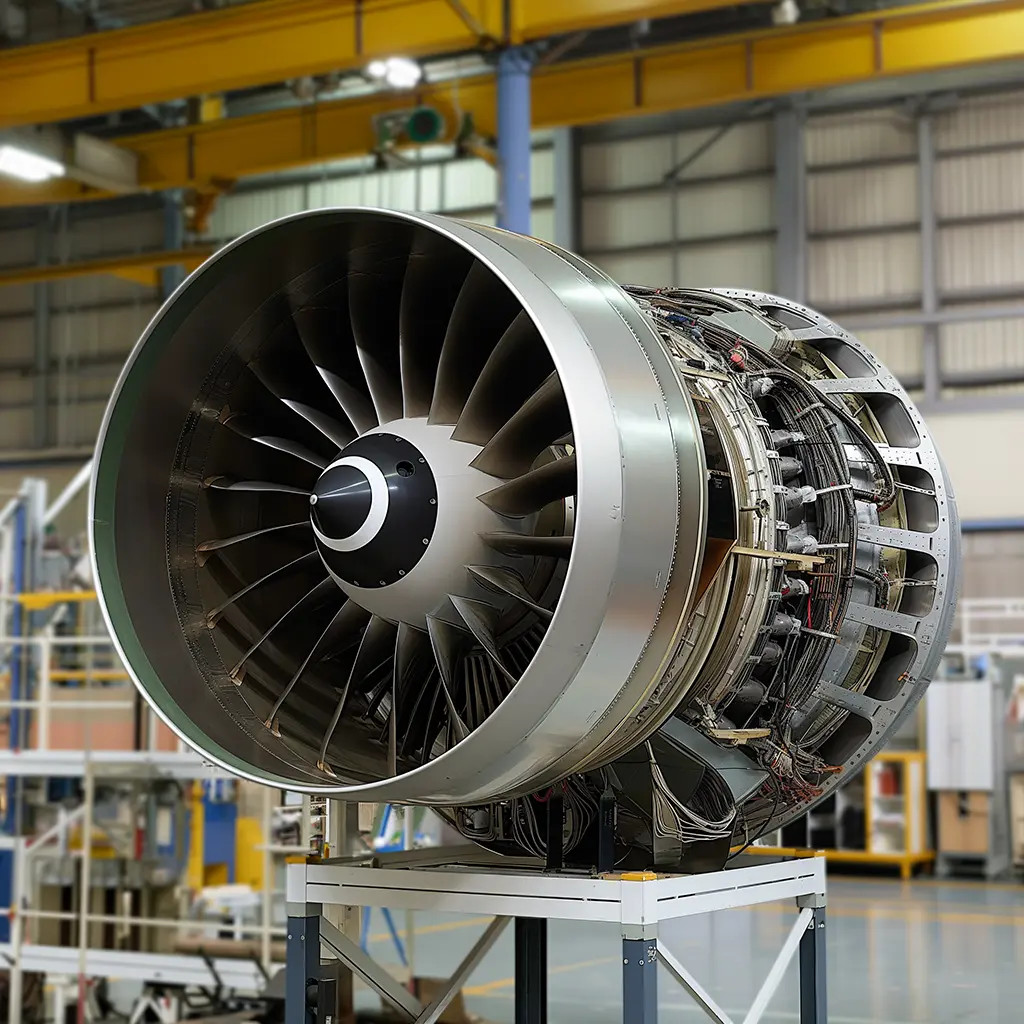
Launching a satellite, for instance, can cost significant amounts, but a manned spacecraft can be exponentially more expensive - not to mention the precious human lives involved. Given these high stakes, tensile testing becomes indispensable for validating the integrity and performance of different aerospace materials under the specific stresses they will encounter during flight.
The aerospace industry tests a number of materials. These include metals like aluminum alloys, which are favored for their high strength-to-weight ratio, and composites which are used extensively due to their lightweight and high tensile strength properties. These materials find applications in aircraft parts such as fuselages, wings, and internal structures. For instance, aluminum alloys are commonly used for structural components due to their strength and lightweight characteristics. Composites are commonly used in areas requiring high strength with minimal weight addition, such as panels and frame structures.
Moreover, the integrity of these materials must be carefully verified through tensile testing to prevent failures that could lead to catastrophic outcomes. Tensile tests help determine material properties such as ultimate tensile strength, yield strength, and elongation at break, which are essential for designing components that can withstand both flight operational stresses and outer space conditions.
Manufacturing Industry
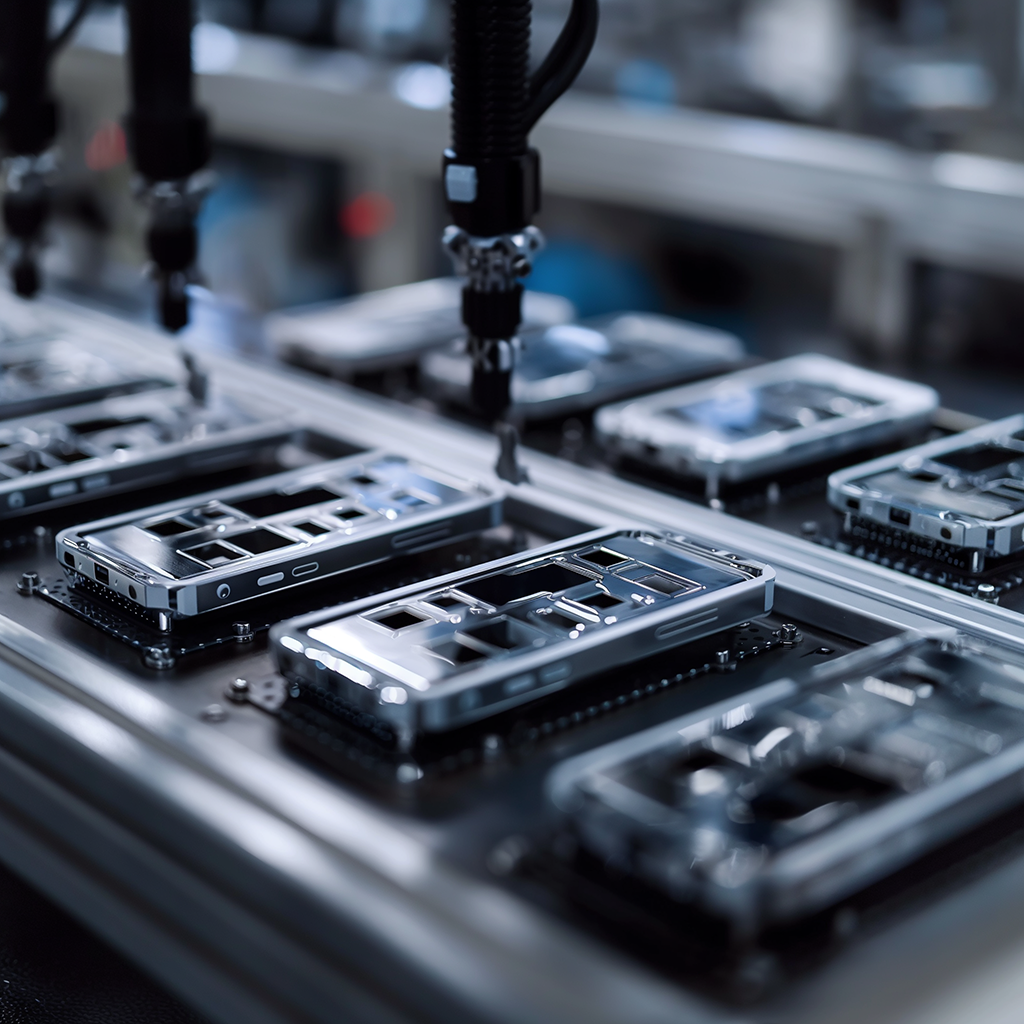
The importance of tensile testing in the manufacturing industry cannot be overstated, since it protects the financial stakes as well as the safety of consumers. Unlike aerospace, where risks include the vast void of space, manufacturing risks, such as those involving consumer electronics like smartphones, can have direct implications for user safety. Among these incidents are battery explosions.
The manufacturing sector uses tensile testing extensively to evaluate the properties of a diverse array of materials before they are shaped into finished products. Metals, for example, are foundational in the production of automotive components and construction materials, where tensile strength, ductility, and resistance to environmental factors are critical. Plastics, which have many uses, are tested for mechanical endurance in applications ranging from medical devices to packaging solutions. Composites, favored for their strength-to-weight ratios, are fundamental in advanced engineering applications like sports equipment, necessitating thorough tensile evaluations to assure performance under stress.
Ceramics, tested primarily for their durability and thermal properties, find their application in abrasive environments and high-temperature settings typical of the electronics and aerospace industries. Through tensile testing, manufacturers can verify that these materials meet the required specifications for each application.
Construction Industry
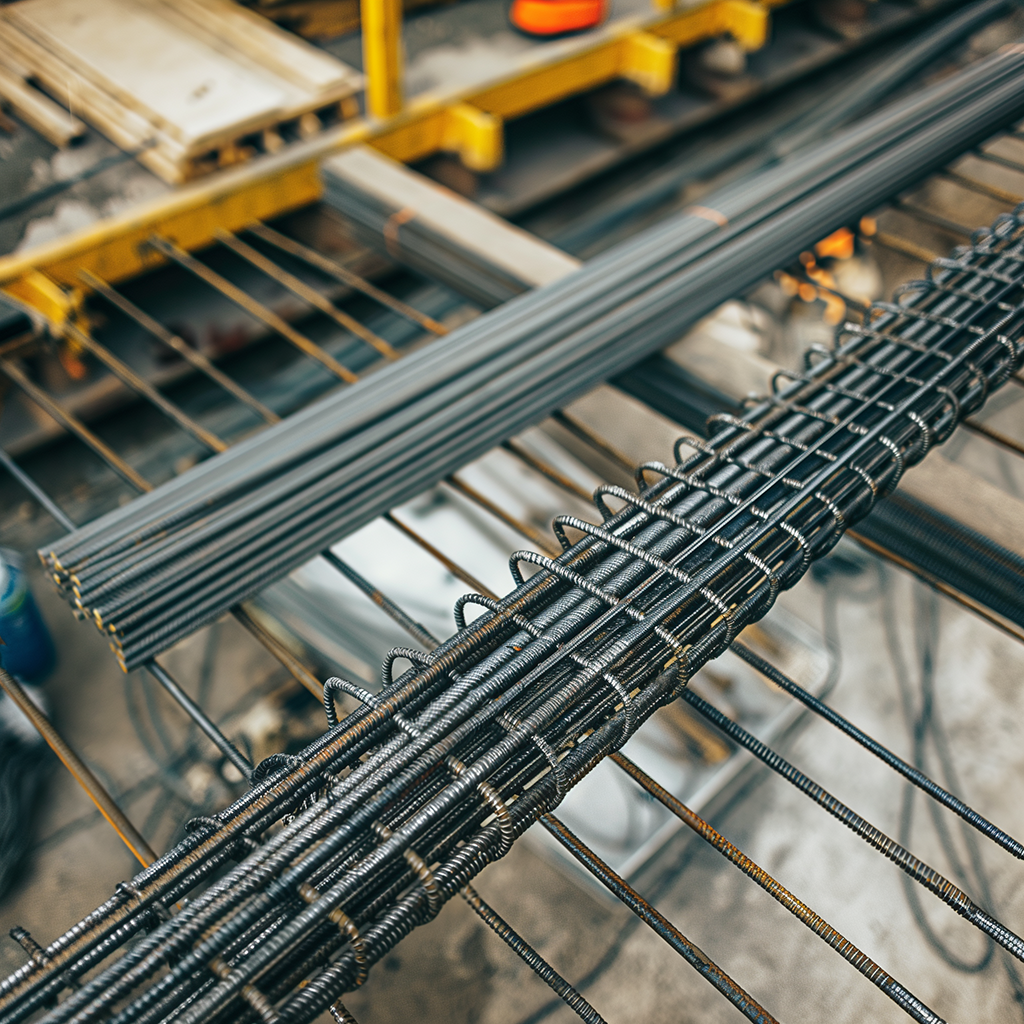
As of 2024, the construction industry is heavily engaged in the development of modern structures, ranging from residential buildings to expansive shopping centers. These structures often feature complex and visually striking designs that challenge traditional architectural norms. Critical to their construction is material integrity assurance, where tensile testing is of critical importance in Research and Development.
Construction materials such as steel, concrete, and composites require tensile testing to verify their quality. These materials need to be able to bear significant loads and stresses, particularly in high-rise constructions where the potential for catastrophic failure makes the stakes extremely high. For example, in iconic structures such as the Burj Khalifa, tensile testing was vital to determine the suitability of materials used in its construction. Testing confirms that these materials can handle the immense pressures and dynamic stresses of such towering structures.
Beyond these traditional materials, tensile testing in the construction industry also extends to newer materials like advanced alloys and polymers. These materials are often used in critical structural applications, including support beams and safety barriers, where failure could have severe consequences.
Automotive Industry
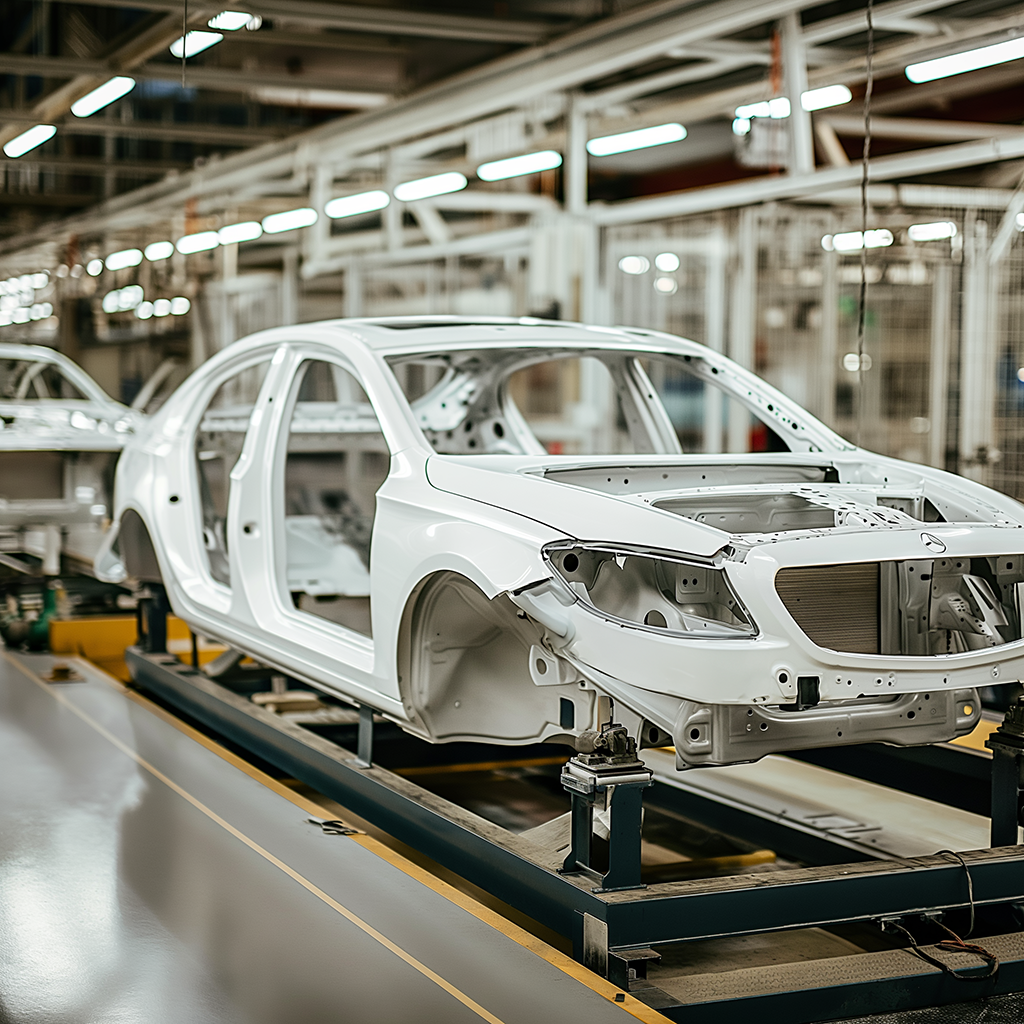
The automotive industry will continue to emphasize tensile testing as a critical part of its R&D processes in 2024, driven by the need to guarantee vehicle safety, reliability, and environmental sustainability. Testing the tensile properties of a variety of car components, such as metals, polymers, and composites.
Testing the tensile strength, ductility, and fatigue resistance of materials used throughout a vehicle is crucial to automotive safety. This is especially important for structural components such as chassis, engine parts, and body panels, which must withstand the rigors of operation. Metals used in engine components, for example, are tested to verify that they can handle thermal and mechanical stresses.
Further, as the industry moves towards lighter materials, advanced composites, and high-strength alloys are used more frequently.
Summarizing Tensile Testing in R&D for 2024
Tensile testing remains a cornerstone of Research and Development in many industries, vital for verifying materials and products' safety, durability, and functionality. This methodical testing process allows scientists and engineers to precisely measure and understand new materials' mechanical properties. This aids in the innovation and improvement of products in industries such as aerospace, automotive, construction, and manufacturing. By verifying that materials can meet demanding standards under stress, tensile testing not only increases product reliability but also contributes to technological advancements. As a result, industries can remain competitive in a constantly changing market.
Furthermore, testing for tensile strength in quality assurance helps prevent costly recalls and makes sure that upcoming developments are ready for market challenges, maintaining consumer trust and safety. The necessity of reliable, advanced equipment for testing tensile strength becomes ever more apparent with material science advancement.
If you are looking for dependable tensile testing solutions, our offerings such as the Servo Hydraulic Universal Testing Systems (600kN / 1000kN) and the Servo Hydraulic Universal Testing Machine 2000kN are designed to address the needs of a broad range of industries. These systems are equipped with the latest technology to ensure high precision and efficiency in testing, meeting international standards, and accommodating different material types and testing requirements.
At TensileMill CNC, we are committed to supporting your tensile testing needs. We provide top-tier equipment for tensile testing and tensile sample preparation. Whether you need to evaluate novel materials or ensure product quality, we offer personalized solutions that boost your R&D capabilities. Feel free to request a quote or contact us directly to ask questions about our products and how they can facilitate your projects. Your advancements through accurate material testing are just a conversation away.