Description
TensileMill CNC's Alignment Device is a meticulously engineered fixture designed to ensure impeccable axial alignment in universal testing machines. Initially introduced as an optional enhancement for our Electro Mechanical Universal Testing System, its significance in achieving accurate testing has led to its availability as a standalone product. This device can be seamlessly retrofitted onto both TensileMill CNC machines and third-party frames, such as popular Instron® models, instantly elevating them to meet the most stringent alignment standards. By fine-tuning the load train coaxiality to within ≤5% misalignment, the device effectively eliminates bending stress and off-center loading, resulting in highly reliable and repeatable material test outcomes.
In practical application, the alignment device is installed between the machine's crosshead and grips or fixtures, allowing for initial coarse positioning followed by precise adjustments via an integrated high-precision coaxiality meter. Post initial setup, the system's coaxiality detection mechanism empowers operators to achieve precise alignments, ensuring full compliance with alignment standards like ASTM E1012 and NASM 1312B. The outcome is a test frame alignment that meets or surpasses stringent requirements for aerospace and other quality-critical industries. Laboratories can leverage this device to guarantee uniform force application, preventing subtle bending stresses that can lead to premature specimen failures or data inaccuracies. The Alignment Device is compatible with a broad range of load capacities—from low-load testing machines up to high-capacity floor models—and is constructed to be durable and rigid, maintaining alignment even under maximum loads.
Key Advantages of the Alignment Device
1. Precision Alignment (≤5% Coaxiality Misalignment)
Achieves exceptionally tight load alignment, minimizing bending and eccentric forces. This level of precision ensures compliance with ASTM E1012 and NASM 1312B alignment standards, which is critical for attaining NADCAP accreditation in aerospace testing laboratories. The built-in coaxiality meter guides users to adjust alignment until the load train is virtually perfectly centered.
2. Enhanced Test Result Reliability
By eliminating misalignment-induced errors, the device delivers accurate and repeatable test outcomes. Engineers can trust that variations in test data are due to material behavior, not anomalies in the test frame. This enhances the statistical significance of results and reduces the need for re-tests due to suspect data.
3. Versatile Application
The alignment fixture supports tensile, compression, bending, and other test modes without modification. Whether you're testing metal specimens to failure, compressing aerospace components, or conducting flexural tests on composites, the device maintains the coaxial alignment of the specimen throughout the test. This versatility makes it suitable for laboratories handling multiple types of mechanical tests.

4. Cross-Platform Compatibility
Designed for universal adaptability, the TensileMill CNC alignment device can be installed on our own Electro Mechanical UTM as well as third-party testing machines (e.g., Instron®). Its mounting system and adjustment interfaces are standardized, allowing seamless integration with most universal testing frames. This protects your investment—you can use the same alignment tool across different machines in your lab, or even if you upgrade equipment.
5. Standards Compliance & NADCAP Readiness
Utilizing this device helps laboratories conform to the highest international testing standards (ASTM, ISO, DIN, etc.) and meet specific alignment criteria set by programs like NADCAP. In fact, integrating this fixture enables labs to be "NADCAP ready", as it ensures the alignment calibration required during audits is in place. The device directly addresses requirements from standards such as ASTM E1012 (verification of testing frame alignment) and ISO 23788 (alignment of fatigue testing machines), and aids in satisfying audit criteria (e.g., NADCAP AC7101/AC7122 for materials testing) by keeping alignment error within permissible limits.
6. Improved Operator Efficiency and Confidence
The alignment process is straightforward and quick. After installation, operators can perform alignment verification in-house without lengthy downtime. The device's coaxiality indicator provides immediate feedback, saving time compared to trial-and-error methods or the need for external alignment services. With confidence in the alignment, engineers can focus on the test itself rather than worrying about equipment setup.
The Importance of Precise Alignment in Testing
Even slight misalignments in a test system can dramatically affect the outcome of material tests. If the test specimen is not perfectly aligned with the machine's loading axis, it will experience uneven stress distribution. Misalignment causes the specimen to bend under load, creating strain "hot spots" near the gripping points and leading to premature failure at the grips. In a tensile test, for example, a misaligned specimen often breaks at or near the grip faces instead of the gauge length, indicating that bending stress, not just axial tension, contributed to the failure. These unintended bending stresses not only cause early breakage but also distort the measured results—the material may appear to have a lower elongation or strength than it actually does, due to the added bending component. In short, poor alignment can mask the true behavior of the material.
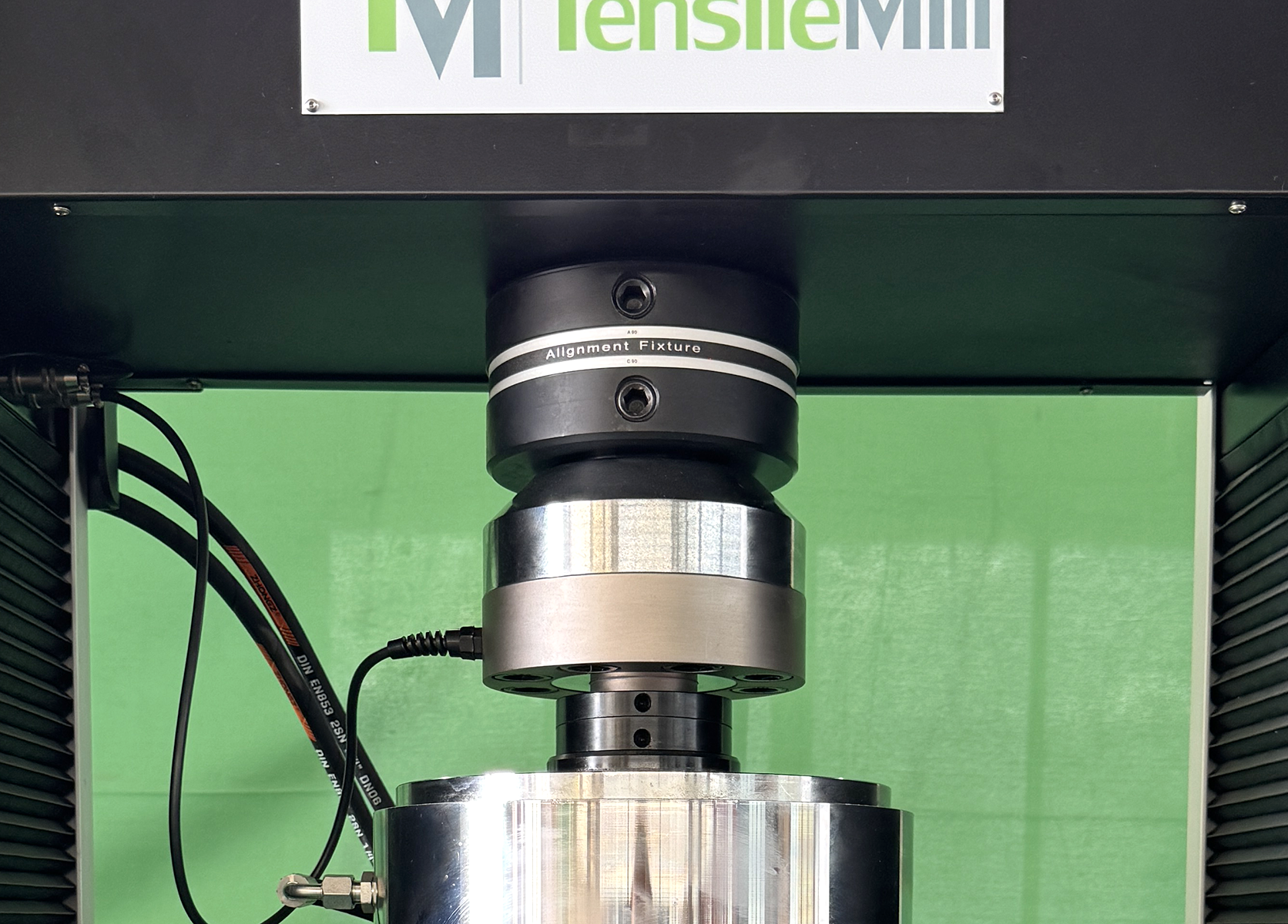
Without a precision alignment device, laboratories may find that stiff or brittle materials frequently fracture outside the expected gauge region at seemingly low loads. This is a classic symptom of misalignment: the specimen is effectively being stressed in a combination of tension and bending, causing it to fail earlier than it should. Such failures and data are not reliable for analysis or certification. Moreover, non-uniform force application violates the assumptions of many testing standards, potentially putting a lab out of compliance. ASTM and ISO testing protocols assume that the force is applied axially; if that is not the case, the calculated material properties (like tensile modulus, yield strength, etc.) can be significantly in error. Engineers in aerospace, automotive, and metallurgical fields are particularly sensitive to these issues because even minor data inaccuracies can lead to improper material selection or unexpected component failures in service.
From a quality and accreditation standpoint, precise alignment is not optional—it is mandatory. The ASTM E1012 standard was developed specifically to address this: it outlines how to verify and quantify the alignment of a testing frame because industry studies showed that misalignment-induced bending can seriously skew test results. In aerospace and defense testing, the NADCAP program similarly requires proof of proper alignment as part of its Materials Testing accreditation. During NADCAP audits, laboratories must demonstrate that their tensile or fatigue test frames have been aligned within allowed tolerances (often using strain-gauged specimens per ASTM E1012 or similar methods). Failure to control alignment can result in audit non-conformances, meaning the lab cannot achieve or maintain NADCAP accreditation until the issue is resolved.
This is why an alignment device is so critical. By using TensileMill CNC's Alignment Device, laboratories ensure uniform, axial loading of test specimens, which dramatically improves result reliability and repeatability. It eliminates one of the biggest hidden variables in materials testing. When alignment is properly managed, any variations in test results are truly due to material differences or natural scatter—not artifacts of test setup. This not only boosts confidence in the data but also means laboratories can meet the requirements of strict standards and customer specifications (for example, NADCAP or OEM mandates that tests be conducted under aligned conditions as per ASTM E1012).
Standards Compliance and NADCAP Integration
The Alignment Device is engineered to help your laboratory meet key industry standards and accreditation requirements related to testing machine alignment:
- ASTM E1012 – Standard Practice for Verification of Testing Frame and Specimen Alignment. This device enables you to verify and adjust frame alignment in accordance with ASTM E1012, ensuring that any bending strain in the specimen is within the allowable percentage. By achieving a coaxiality of ≤5% during setup, you're directly adhering to ASTM E1012 guidelines for minimal misalignment. The result is reduced measurement error in tensile, compressive, and fatigue tests, as required by this standard.
- NASM 1312B – This specification, derived from aerospace requirements (originally stemming from MIL standards), also demands strict alignment in fastener and material testing. The TensileMill CNC alignment fixture meets the NASM 1312B criteria for coaxial loading, making it suitable for use in testing scenarios governed by this aerospace methodology. In practical terms, if your projects or contracts reference NASM 1312 series test methods, this device will ensure your setup complies.
- DIN / ISO Standards – Many European and international standards emphasize proper alignment (for example, ISO 23788 for fatigue test machine alignment and parts of ISO 6892 and DIN 50100 series for tensile testing procedures). Using the alignment device helps laboratories conform to these global standards by maintaining the alignment within specified limits. This is important for multinational companies or those selling to global markets, as compliance with DIN and ISO standards is often required. The device's capability to reduce misalignment to negligible levels supports adherence to the alignment verification guidelines found in these standards, ensuring that tests conducted are valid under ISO/DIN criteria.
- NADCAP – The National Aerospace and Defense Contractors Accreditation Program (NADCAP) is a critical industry standard for quality and safety, particularly in aerospace and defense materials testing. Compliance with NADCAP requires laboratories to verify that their testing frames are properly aligned, reducing any potential test result errors caused by misalignment. TensileMill CNC's Alignment Device plays a crucial role in achieving and maintaining NADCAP accreditation, as it ensures that your test machines conform to the alignment standards specified by NADCAP. The device aids in passing the rigorous NADCAP audits by keeping the alignment of your testing machines within the strict tolerances required for certification. This makes it an essential tool for aerospace and defense laboratories pursuing or maintaining NADCAP certification.
Contact for Estimate
Precision is the foundation of accurate testing. Equip your TensileMill CNC Electro-Mechanical UTM (50kN–600kN) with our Alignment Device and ensure your lab consistently produces reliable, standards-compliant results.
Ready to elevate your testing accuracy? Contact us today for an estimate or to request a personalized consultation. Our team is ready to help you integrate this essential tool into your testing process, ensuring maximum performance and audit readiness.
People Also Searched For
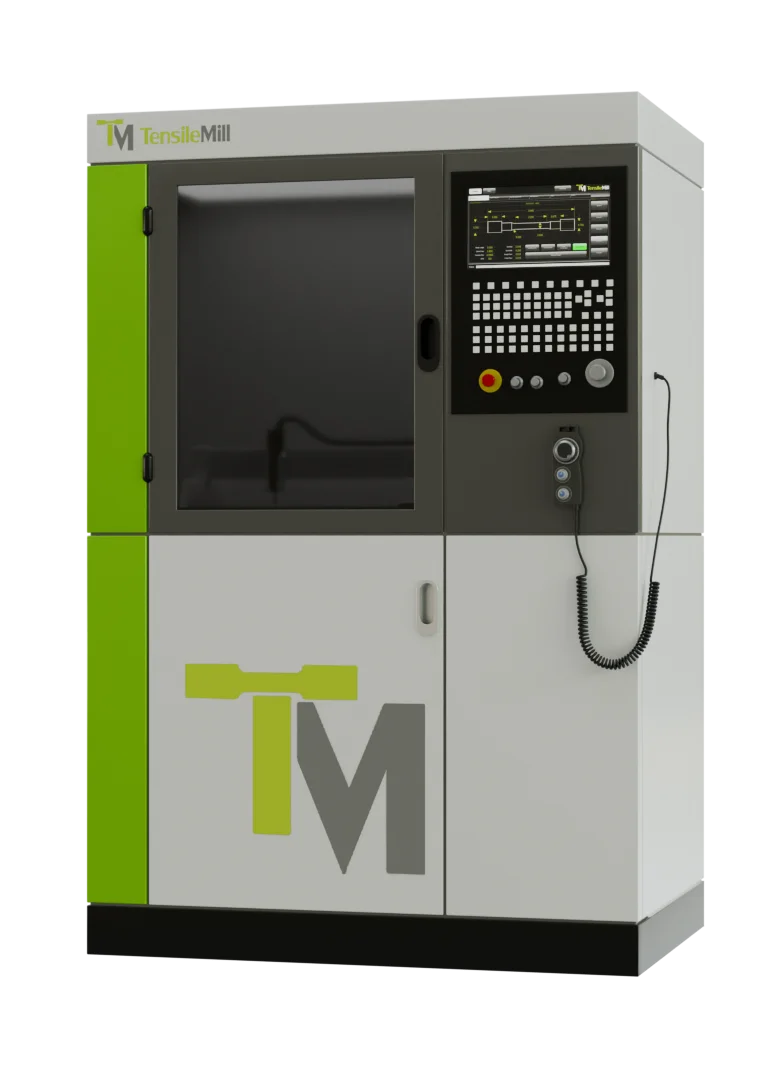
TensileMill CNC - Classic Upgrade
The TensileMill CNC - Classic Upgrade is the ultimate solution for precise and repeatable flat tensile and impact test specimen preparation. Engineered with TensileSoft™ technology and powered by a Fanuc controller, this machine offers an intuitive, user-friendly experience for both seasoned CNC operators and those with minimal training. Its compact footprint and turnkey design make it an ideal addition to any testing facility, ensuring maximum efficiency without compromising on accuracy. With a high-precision 3.2kW servo motor, the TensileMill CNC - Classic Upgrade ensures 0.0003” accuracy, handling specimens up to 14” long, 2” wide, and 0.5” thick. It meets ASTM, ISO, DIN, and JIS standards while efficiently preparing three 1.0” thick stacks at once with its triple clamping fixture. Compatible with an Impact/Pendulum notching machine, it also streamlines U & V-notch specimen preparation, making it a top choice for precise, high-speed testing.
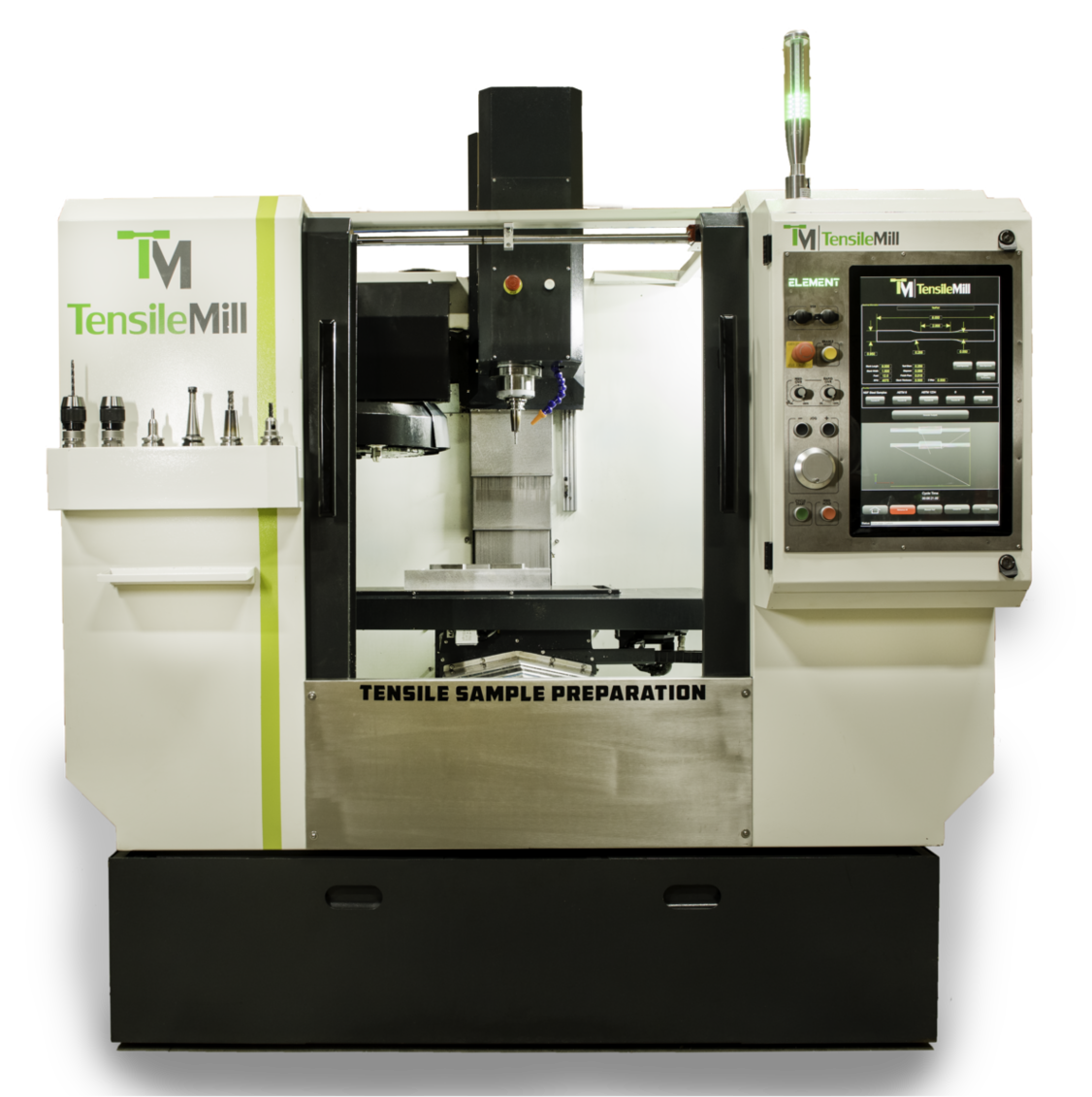
TensileMill CNC XL - Flat Specimen Preparation
The XL model is our larger tensile sample preparation machine that comes standard with an upgrade function of full CNC Carbon package for general purpose CNC requirements. TensileMill CNC XL is equipped with a state-of-the-art auto tool changer for the ultimate milling flexibility and time savings, allowing to prepare various types of tensile specimens and other parts. The advanced software allows to the operator reach milling results in seconds with a push of a few buttons. TensileMill CNC XL is an ideal user-friendly solution for medium to large size laboratories and manufacturing facilities.
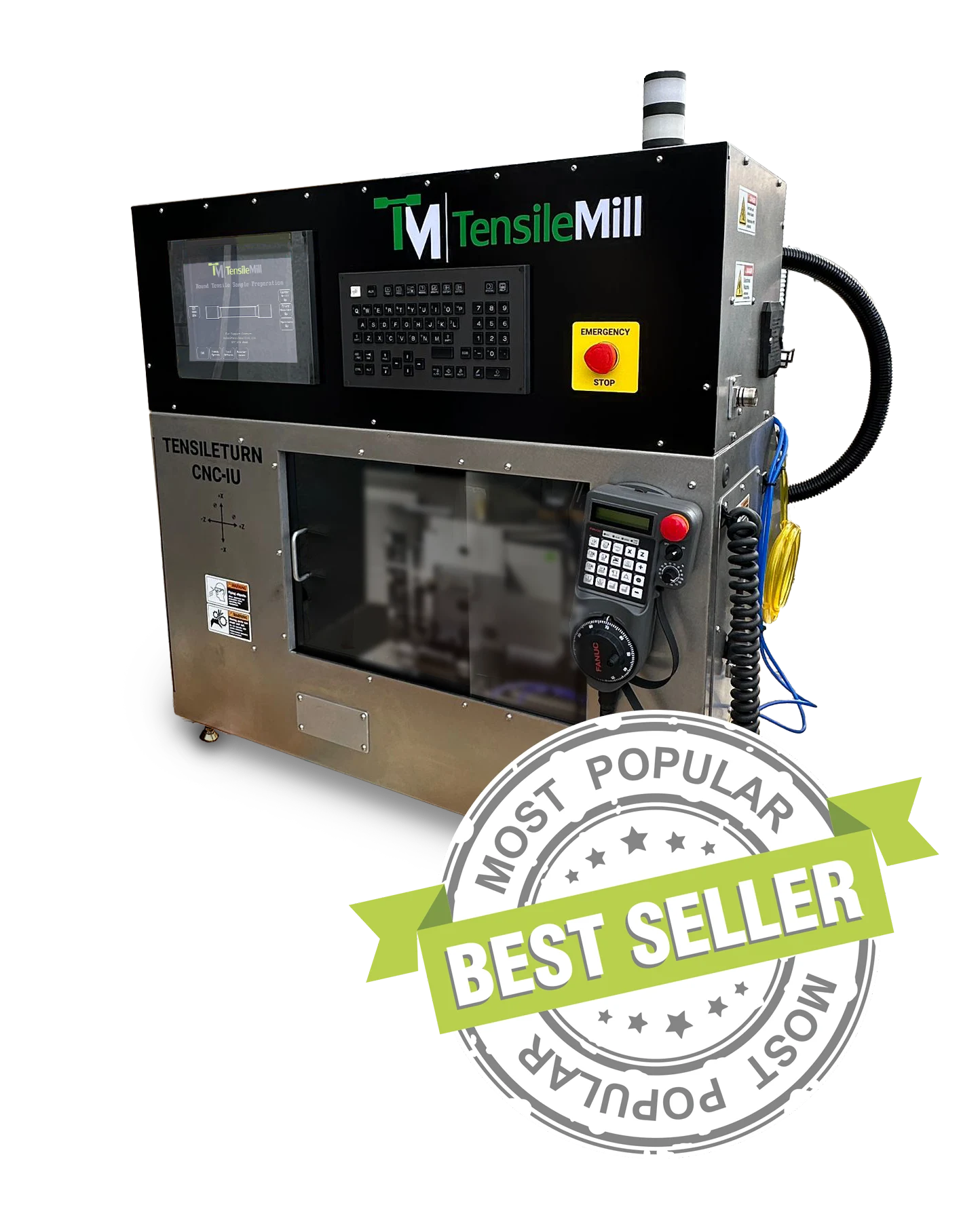
TensileTurn CNC - Industrial Upgrade - Round Tensile Sample Preparation Machine
The Industrial Upgrade model is a substantial step up from our Classic system. It offers the ability to accommodate larger starting blank sizes, tougher materials, irregular shapes, higher specimen preparation volumes, automatic center drilling and other unique functions required for the simplest and most accurate round tensile sample preparation. This system comes standard with a granite frame for added stability and the shock absorption for maximum sample preparation accuracy and longer system life-span. Though the Industrial Upgrade system is extraordinary for tensile specimen preparation needs, it is also capable of full range of CNC machining capabilities.
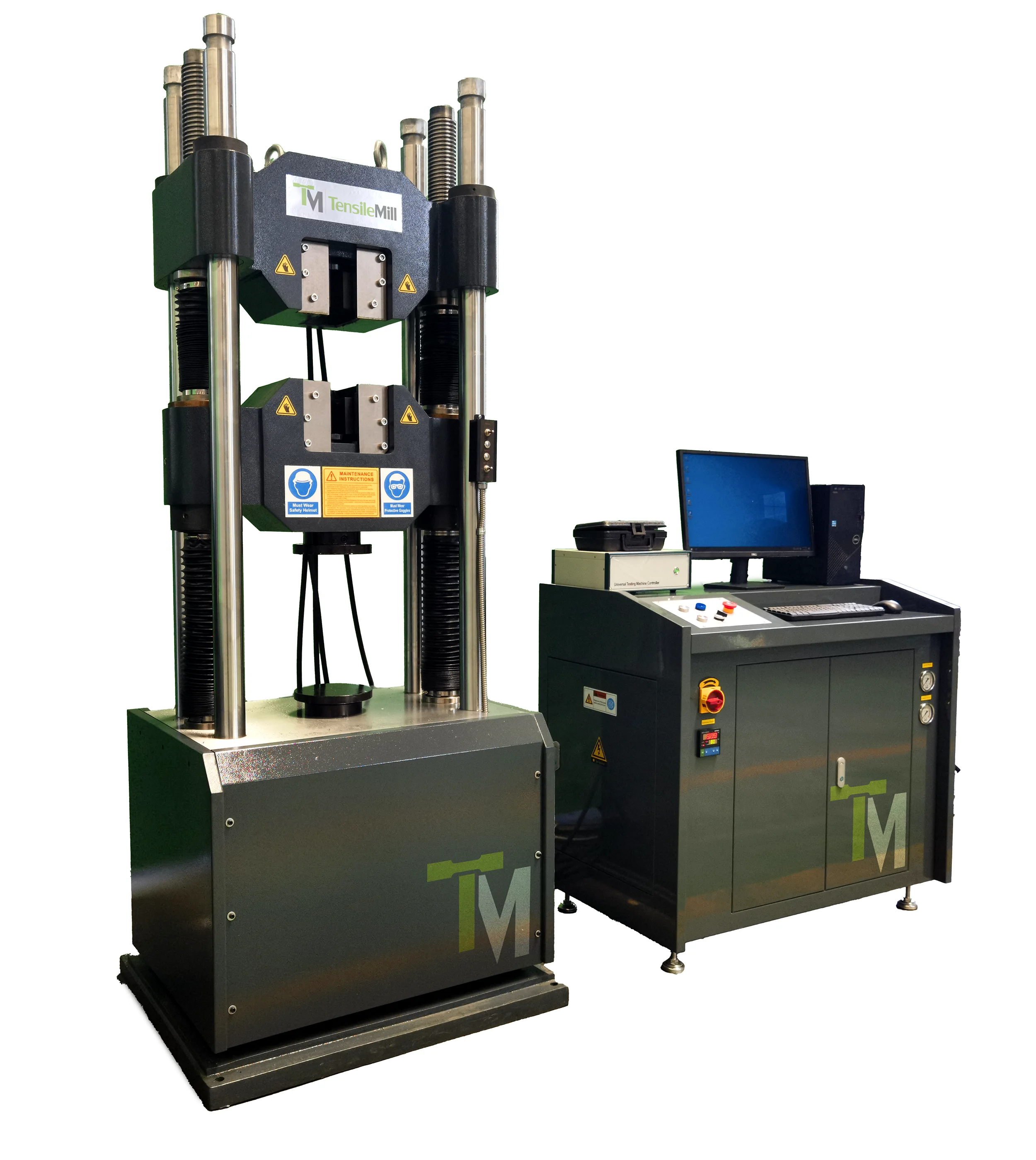
Tensile Testing Equipment
When selecting a tensile testing machine, there are a number of factors that must be considered. Whether you're upgrading in quality or functionality, or have the decision to move your materials testing in-house, you want to avoid buying a machine that doesn't meet the range of testing or materials for your needs. Of course you will be guided by the type of testing - tensile, compression, fatigue, etc. - and the ASTM or ISO standards for the market your product will enter. Other factors to consider when selecting the perfect tensile tester include…