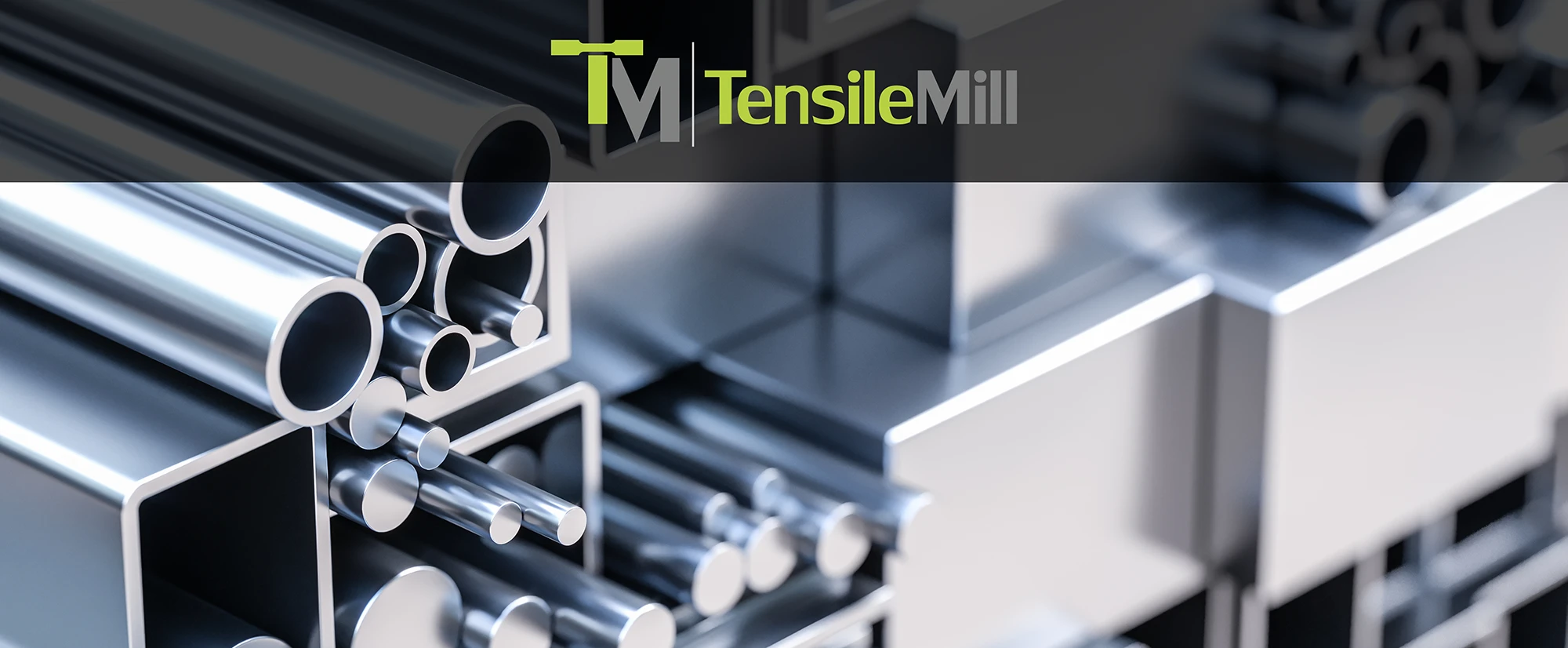
In this article, we discuss issues related to aluminum extrusion processes and quality control of industrial products manufactured using this process.
Extrusion Process, What Is It For and How Does It Work?
The process of creating any industrial product after its design involves three stages: material selection, development and implementation of production technology, and ongoing quality control of products.
The choice of materials is based on compliance with the design requirements, and they must also be durable and reliable, have a low cost, and be easily processed to give the appropriate shape, which is also provided for by the design. The quality control includes testing material mechanical properties as the most informative procedure. It is carried out at two stages: when selecting the material and when controlling the quality of the parts obtained after processing.
One of the most versatile methods of material processing is extrusion (from the Latin "extrusio" is "pushing out") is the process of giving a plastic material a constant shape by forcing it through an opening using an extruder. The basic principle is that the material is heated in a closed chamber until it acquires plastic properties. After that, it is pushed out using pressure through the outlet of a specified shape that defines the geometry of the resulting workpiece. This geometry of the billet is maintained by cooling at the outlet of the extruder. The resulting profile can be further cut into specific fragments for multiplication, or vice versa, welded with a previous billet to produce longer shapes. Continuous feeding of the feedstock into the extruder chamber makes it possible to produce extended shapes without the need for welds. For example, TensileMill CNC MINI - Compact Flat Tensile Specimen Preparation Machine can help prepare tensile dog bones for Tensile Testing Process.
What Materials Can Be Processed By Extrusion?
The main materials that can be processed by extrusion include plastics, rubbers, ceramics, and even food. Products that can be manufactured by extrusion include plastic pipes, plates, profiles, building and packaging materials, wires, small channels for electronics, and much more. As for metals, extrusion requires the process to be carried out at sufficiently high temperatures to make the metal ductile.
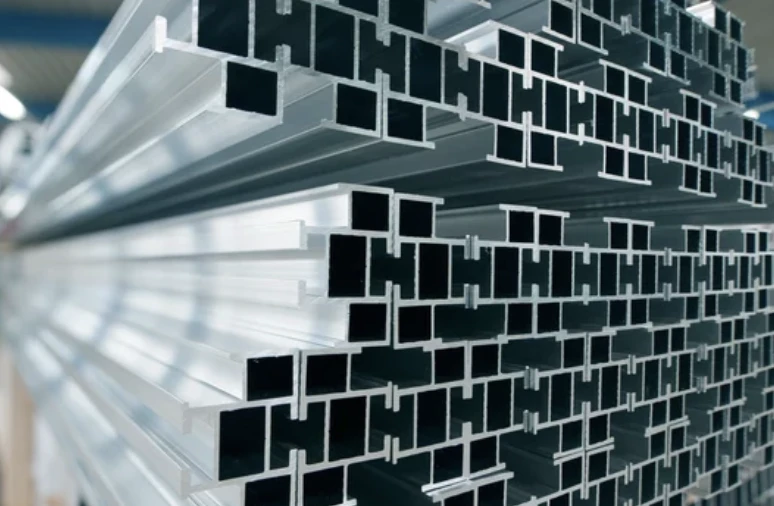
What Makes Extrusion Effective?
The efficiency and commercial success of the extrusion process is most evident when automated, computer-controlled production lines are used. This provides the highest level of precision, allowing for products with identical parameters. The use of automatic sensors and systems for monitoring pressure, temperature and production speed makes it possible to automatically adjust the extrusion process parameters in real time, ensuring production quality and safety.
Robotic systems can be used to perform labor-intensive operations such as loading and unloading, cutting and processing of products. Computers can be used to calculate the necessary process conditions, store, process and analyze resulting data. It helps to increase production efficiency and accuracy. Combined with Internet technology, this enables remote monitoring and control.
Features of Metal Extrusion
Metal extrusion is used to form pipes, profiles, sheets and other metal products. During the extrusion process, a metal bar (a starting block of metal) is heated to a high temperature and pushed through a die using pressure. This process can be performed using various types of metals, such as aluminum, copper, lead, steel, and others. Metal extrusion is an effective way to produce a large number of complex metal parts. This process allows for the creation of high-quality products with high shape accuracy and high productivity. The ability to make the process continuous makes it easy to integrate the process into conveyer line. Extrusion allows for the production of parts with sufficient precision and high shape repeatability. It can be used to form various types of metals, such as aluminum, copper, lead, steel, and others.
Pros and Cons Of Using Extrusion For Industrial Metal Processing
In addition to extrusion, there are other methods of metal processing, including:
- metal casting: creating a mold from metal, the process allows for products with complex shapes and high surface quality, but can be quite expensive and time-consuming;
- stamping: forced change of shape according to the stamp, a process with high accuracy and speed, but limited to the shape of the stamping dies;
- machine tool processing is the process of removing material from the metal surface using cutting tools (milling or turning). This process allows for creation of products with high precision and a variety of shapes, but is quite slow and can be expensive.
The extrusion process provides products with relatively high precision, but with very high speed, and a variety of shapes. Because of its high rate, extrusion is usually a more efficient and cost-effective process than other metalworking methods especially for long workpieces or a large number of parts.
The Advantages of Extrusion For Metal Forming
The advantages of extrusion for metal forming include:
- a variety of shapes and sizes: from rectangular and round to millions of different complex and highly complex shapes
- sufficient precision and surface quality, which makes the part ready for further processing or use;
- efficiency and cost-effectiveness compared to other metal processing methods, as extrusion can be easily adapted to conveyor production;
- strength and durability: parts made by metal extrusion usually have increased strength and durability, as the material is formed with a homogeneous structure without pores;
- low material loss: the process principle itself provides for minimal wastage, and fewer defective products, that further increases material savings and reduce costs;
- longer product lengths: metal parts up to 100 meters or more in length can be produced, allowing for the production of large metal structures;
- suitability for different types of metals.
There are also several disadvantages of the extrusion process, namely:
- the extrusion process requires high energy, especially when processing refractory metals such as steel. This can lead to increased production costs;
- moderate accuracy of metal extrusion shapes (up to a millimeter) compared to other machining methods, such as milling or turning (up to several micrometers): this can lead to inaccuracies in shapes;
- metal extrusion cannot always be used to create complex shapes that contain internal parts;
- processing brittle metals by extrusion can be difficult.
The extrusion process can lead to defects such as cracks or deformations. However, this is largely due not to the shortcomings of the technology, but to its inaccurate use: when the process is applied to brittle or refractory materials at incorrect temperature conditions, or when excessive pressure is applied. It can also be caused by improper use of equipment, neglect of timely calibration of control sensors and other maintenance.
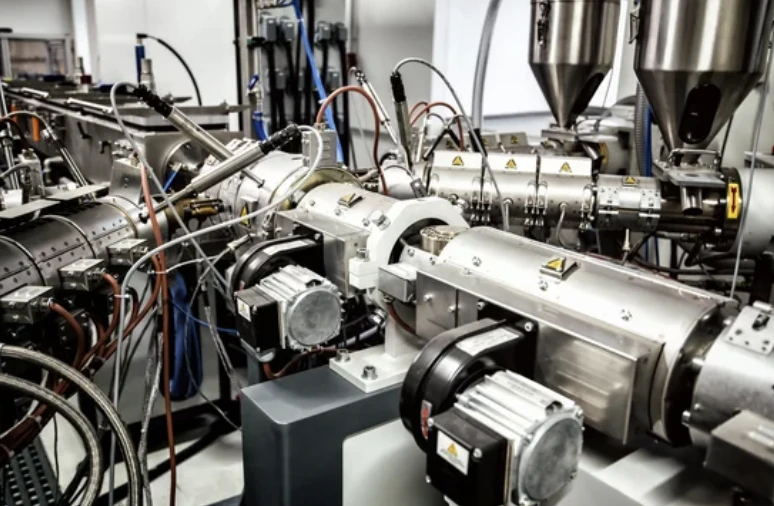
Combining Extrusion With Other Metal Processing Methods
To offset the disadvantages and effectively utilize the advantages of extrusion, this process can be combined with other metalworking methods to create complex parts with high shape accuracy and surface quality. Finding the optimal combination of methods is the main task of technological development to bring a product design into production. Cutting machines are the most common complement to extrusion technology, as the resulting elongated profile must be cut to specific dimensions specified by the product design.
To achieve greater shape accuracy, the part can be further processed on machine tools after extrusion. In this way, the high precision of machine tool processing will be combined with the material savings inherent in extrusion. In addition, since the shape of the part will only require some adjustments, machine work will not take much time. Both milling and turning can be included depending on the desired shape. This will not only improve accuracy, but also result in a smooth, uniform surface. Even more significant changes in shape can be achieved by using press processing. Metal casting and extrusion also go hand in hand, as casting molds can be produced by extrusion.
Thus, the combination of different metal processing methods allows for the creation of complex parts with greater precision that meet the requirements of various industries.
Features of The Aluminum Extrusion Process
Pure aluminum is almost never used as a structural material because it is a rather soft metal. But its alloys, which contain 1 to 15 percent of other metals, have much better mechanical properties. However, all such alloys are usually referred to simply as "aluminum" in layman's terms. Typical alloying elements include copper, magnesium, manganese, silicon, tin, nickel, and zinc. These additives not only give the alloy certain mechanical properties, but also affect corrosion resistance and the temperature at which extrusion takes place.
Typically, aluminum extrusion temperatures are between 400 and 550°C (750 and 1025°F), depending on the alloy used to produce aluminum profiles. At this temperature, the hardness of the aluminum alloy decreases, and it becomes ductile, allowing the mass to be pushed through the extruder outlet. The aluminum extrusion temperature depends on the alloy composition and processing technology. Uniform temperature distribution along the entire length of the workpiece is an important condition to avoid deformation during extrusion. Due to aluminum's high thermal conductivity and heat capacity, this task is usually easily accomplished with a heating system. In some cases, the temperature in certain areas can be regulated by the flow of gaseous or liquid nitrogen. The mold exiting the extruder can also be cooled by water.
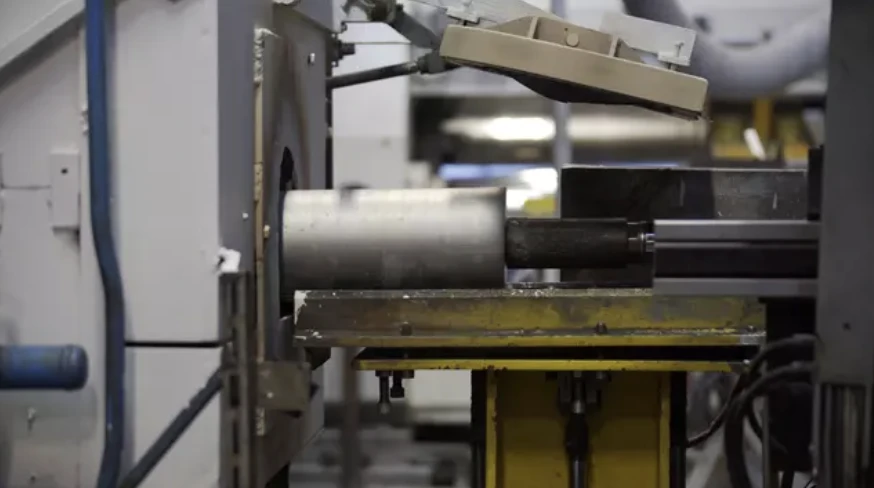
Other features of the aluminum extrusion process include the following:
- pressure control is very important in the process of aluminum extrusion for high precision and repeatability of product shape: since aluminum is a rather soft material and can be easily deformed, especially when it leaves the extruder quickly under excessive pressure, which will not allow timely reduction of the outlet temperature;
- aluminum has a high coefficient of thermal expansion, so when preparing the extrusion, this factor should be taken into account in calculations of the amount of feed metal and process conditions;
- aluminum is highly susceptible to oxidation at evaluated temperatures, so contact with air and other substances that can cause oxidation must be avoided during extrusion: to create an inert atmosphere, aluminum extrusion is carried out in a stream of gaseous or even liquid nitrogen, which also serves to prevent overheating of the alloy and certain parts of the equipment;
- high requirements for surface treatment: aluminum products usually have a high surface quality, which requires more careful attention to the fulfillment of all the conditions of the technology and the technical condition of the extruders.
In general, the aluminum extrusion process is well known. There are reliable technical extrusions are available depending on the type of alloy and the shape of the product. It should be added that the use of aluminum is well aligned with saving environmental trends, as it is a non-toxic and recyclable material.
What Industries Use the Aluminum Extrusion Process?
Aluminum extrusion products are found everywhere in our daily lives. In construction, aluminum profiles are used to make windows, doors, facades, balconies, fences and other structures. Aluminum profiles are used to make car bodies, frames, and decks, as well as various radiators, cases, panels, and other parts of electronic devices. In furniture production, aluminum profiles are used as connecting elements. Food packaging, such as cans for canned food, tubes for toothpaste or ointments, etc., is also made using the aluminum extrusion process. Modern sports equipment, as bicycles, skateboards, fishing rods, ski poles, tripods, and much, much more are made from profiles produced by the aluminum extrusion process.
The aerospace industry uses aluminum due to its unique properties. First and foremost, it has a low density, which can be up to three times lower than, for example, iron-containing alloys. Combined with the high strength of aluminum alloys, this makes it possible to use them as materials for the manufacture of spacecraft parts and structures.
Aluminum extrusion is also widely used in the aircraft industry to manufacture various parts such as fuselages, wings, landing gear struts, and others. Aluminum profiles produced by extrusion are highly durable and lightweight, which are important characteristics for the aviation industry. This helps to reduce aircraft weight and fuel consumption, thus increasing its performance. Therefore, aluminum extrusion plays an important role in the production of aircrafts. Tensile testing is one of the key aspects that ensures high quality of the manufactured parts. TensileMill Flat Specimen Preparation Equipment can be used to prepare the tensile dog bones for Tensile Testing processes.
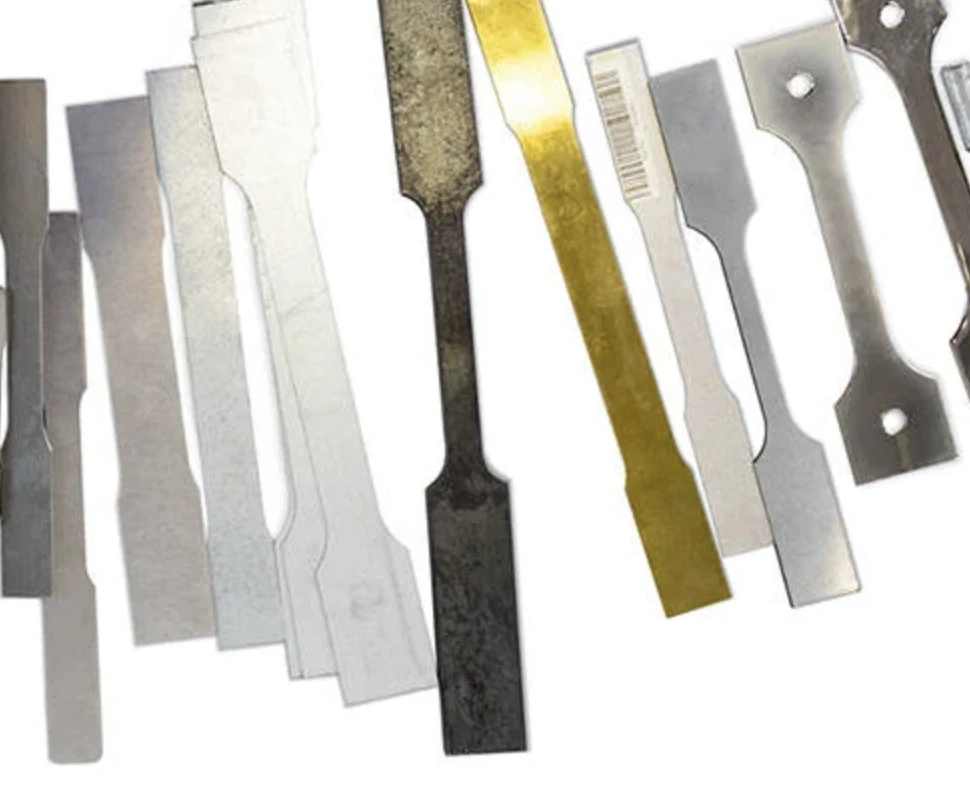
Before moving on to the next section on product quality control, let's summarize the above:
1. What is extrusion?
Extrusion is a method of forming materials by forcing them through a hole of a certain geometry that defines the profile of the formed oblong product.
2. Can all materials be processed by extrusion?
The necessary properties of materials that can be processed by extrusion are plasticity, which increases at elevated temperatures, allowing the mass to be pushed under the action of a press through the molding hole of the extruder. The material must retain its shape and not become brittle when cooled. For example, high-strength steels, tungsten alloys, chromium, or copper-nickel alloys are very hard but brittle materials and can be difficult to process by extrusion.
3. What are the advantages and disadvantages of extrusion for metal processing?
Among the available metalworking methods, extrusion is the most suitable for producing extended profiles of various cross-sectional shapes based on the use of different alloys. Due to the low material loss and ease of adaptation to conveyor production, extrusion makes production more environmentally friendly, efficient and cost-effective. The dimensional accuracy of the extrusion process is sufficient for most applications. In cases where greater precision is required, extrusion can be combined with other metalworking methods. The disadvantages of the process include high energy consumption and limitations on the processing of some brittle metals and alloys.
4. What are the features of the aluminum extrusion process?
Aluminum and its alloys acquire the ductility required for extrusion at temperatures in the range of 400 and 550°C (750 - 1025°F). It does not become brittle, so the profile does not crack or break after cooling, making aluminum extrusion a near-perfect process.
5. What is it about aluminum that makes it so popular in the aerospace and aircraft industries?
Lightness! Strength! Corrosion resistance!
These properties make aluminum an almost ideal material for use in the aerospace and aircraft industries. A large number of well-known aluminum alloys are available for choose based with a wide variety of specific properties.
6. What are the disadvantages of aluminum as a structural material?
The strength of aluminum is still inferior to steel or titanium. This issue is solved by using a greater wall thickness. A significant disadvantage is its low resistance to high temperatures: aluminum quickly loses its strength at high temperatures and can even burn in the air. Therefore, other materials, such as more expensive titanium, are used for high-temperature applications, such as aircraft engines. Aluminum is more expensive than steel and has a greater tendency to interact with acid and alkaline agents, which can reduce structural reliability, especially in aggressive environments. Damage to aluminum parts is more difficult to repair. Welding of such structures is complicated due to the high thermal conductivity of the metal and loss of strength at elevated temperatures. However, there are still reliable technological solutions for welding aluminum.
7. How is the quality of aluminum products controlled?
Quality control procedures take place at two stages of industrial product development:
- at the stage of material selection to check its mechanical properties, which must meet the design requirements;
- during the ongoing quality control of manufactured products.
Read more about how quality control is performed in the next part of the blog.
In-line Quality Control of Aluminum Extrusions
Quality control of the aluminum extrusion process involves a thorough inspection of each stage of the extrusion process, from the selection of raw materials to the completion of the part. This ensures compliance with design, quality and safety requirements. Quality control involves a variety of methods, such as measuring the dimensions and geometry of the part and visually assessing the surface condition. In addition, more instrumented methods are used, such as flaw detection and mechanical property testing.
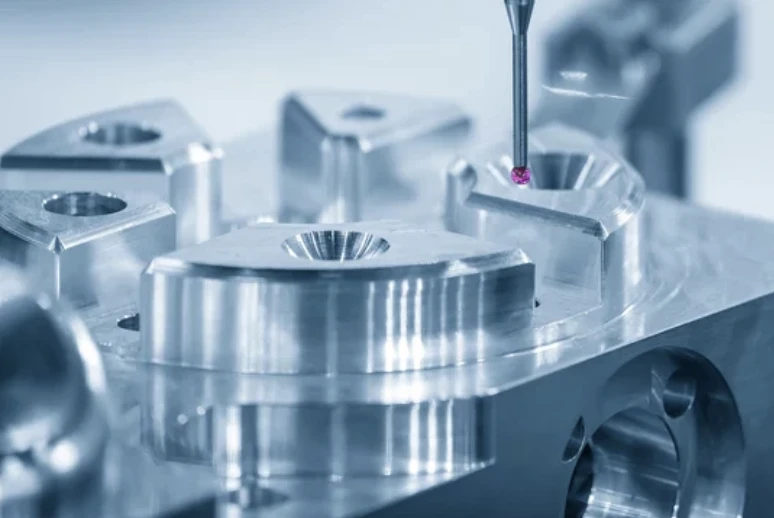
Mechanical property inspection is an important part of the quality control of the aluminum extrusion process. These tests are performed to determine the strength, stiffness, ductility, and other mechanical properties of the material. Depending on the product, it may include tensile, compression and bending tests to determine the strength, ductility and stiffness of the material. For this purpose, special test devices are used that apply a mechanical load to a material sample, measuring changes in its geometry. Impact tests help determine the material's ability to absorb impact energy. After the test, the results are compared with the established standards and requirements for the material. If any deviations are detected, additional research is conducted to find out the cause.
Tensile Testing of Aluminum Extrusions
Tensile Testing is the most common type of mechanical testing performed on standard round or flat specimens. Testing takes place under conditions of axial tensile force, mostly using special tensile testing machines. From the changes in the geometry of the part during tensile testing up to the moment of rupture, parameters such as tensile strength, maximum elongation and maximum cross-sectional area contraction are obtained. These measurements allow for evaluation of the strength and ductility of the material under static loads and can be used in comparison with the corresponding data of other materials at the stage of material selection for product development. For the ongoing quality control of aluminum profiles, the data obtained is compared with defined standard values.
Accurate reproduction of the tensile material sample is critical to obtaining reliable mechanical test results for aluminum extrusions. Therefore, we will pay more attention to this process.
Making Tensile Specimens From Aluminum Profiles
Flat specimens for tensile testing of aluminum extrusions are much more convenient to make from the walls of aluminum profiles. They have a dog-bone shape with a tapered part in the middle and wide ends, which are used for fixing in the testing machine. The quality of the produced tensile specimen is guaranteed by the use of program-controlled milling machines. Such flat sample preparation machines are manufactured by TensileMill CNC Inc.
A whole line of equipment for preparing flat tensile specimens, such as dog bones is now available. These machines are designed with the idea of ease of use for operators of all levels while maintaining the speed, accuracy, and reliability of our tensile specimen preparation machines.
With this equipment, every CNC run will result in a perfect tensile specimen! Learn more about the TensileMill CNC line of flat tensile specimen preparation equipment by contacting us today!