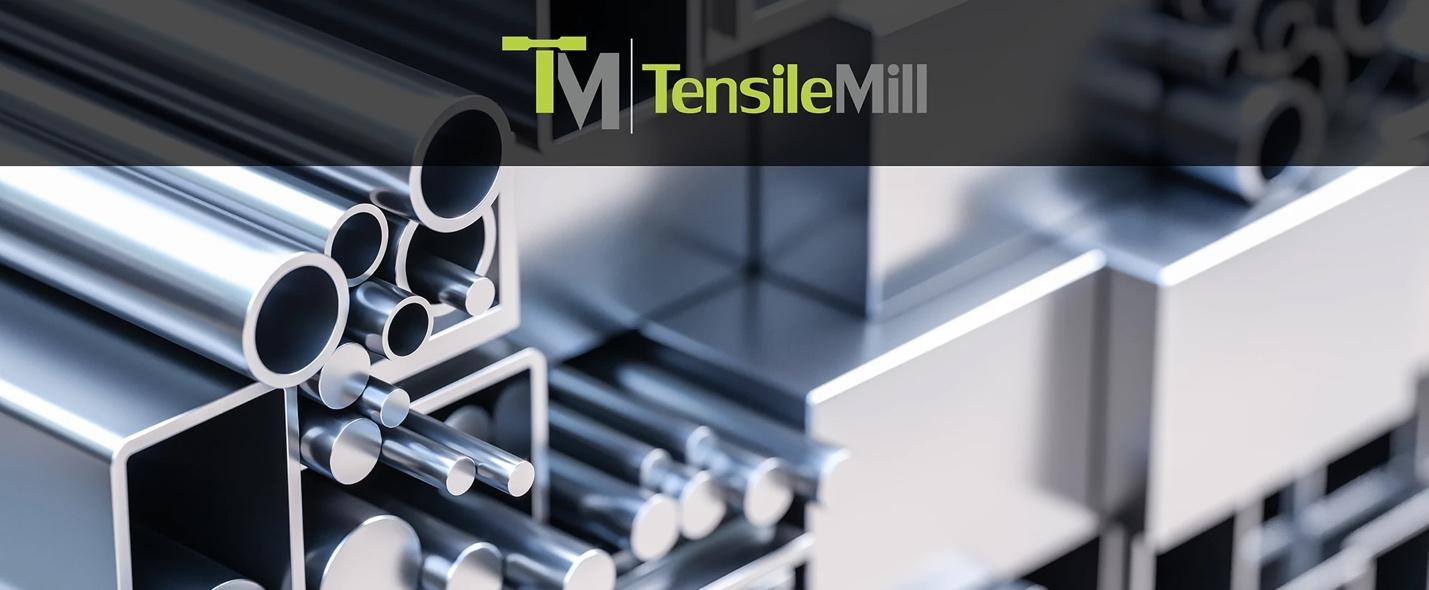
Heat treatment is the process of high-temperature workup of starting materials and products to change their structure and properties in a desired direction. The process involves heating at a specified rate to a certain temperature, holding at that temperature for a certain time, and then cooling at a specified rate. The original shape of the working metal is preserved.
If you are interested in the nuances of this process and the benefits of heat treatment in metalworking, this blog is for you!
Introduction
The fact that metal properties depend not only on its composition but also on how it has been processed was known more than three thousand years ago. An interesting pattern was noticed: if a carburized iron product was heated to a red color and then quickly cooled in water or other liquid, the metal acquired greater hardness. This was quenching, which to this day remains the most important steel heat treatment operation. At the time, no one understood why metal became stronger and harder, but there were many recipes for hardening: almost every master had his own secret. Of course, there were many secrets, myths and superstition surrounding this process.
Nevertheless, the ancient hardening technologies used by Damascus weaponsmiths at the end of the first millennium BC allowed them to produce steel blades that gave a significant advantage to the owner of such weapons. According to descriptions, they quenched their blades in a mountain gorge where a strong wind blew. It was believed that the elasticity and strength of the wind were transmitted to the weapon. Blacksmiths of ancient Georgia also treated steel products in a similar way. The technology of making steel swords in Japan is considered an art. Homer in his Odyssey describes the hardening process as follows: "as a blacksmith plunges a glowing axe or adze into an ice-cold bath and the metal screeches steam and its temper hardens - that's iron's strength."
So let's start looking at the benefits of heat treatment of metals and how it works. But we need to start by studying the processes that happen to metal when it is heated.
What happens when metals are heated?
Metal heating leads to several consequences at once, here are the main ones.
- The metal expands thermally in all directions, i.e. its length, width and surface area increase. When a metal is heated, its atoms and molecules begin to move faster, interatomic bonds weaken, which leads to an increase in the distance between them and an increase in the volume of the metal. When cooled, the dimensions are restored.
- The vast majority of metals and alloys increase their ductility with increasing temperature, including iron, steel, copper, aluminum and its alloys, magnesium, brass, and others. At the same time, these metals acquire the ability to be forged, i.e., to change shape without breaking under the influence of an external force. For example, steel heated to 700°C (1292°F) requires 4.5 times the forging force as steel heated to 1200°C (2192°F). Other metals and alloys, such as gray cast iron, tin bronze, and zinc alloys, do not deform when heated; they are brittle and fracture on impact.
Metal crystals usually have a regular structure, with atoms arranged in a certain order. However, when a metal is heated, the atoms become more mobile and the metal becomes more ductile. Heating a metal can also cause a change in the type of its crystal structure. Changing the structure will lead to a decrease or increase in ductility, because the type of structure has a decisive influence on the properties of metals. This explains why the effect of plasticity changes during heating is observed differently for different metals. - The thermal radiation of metals when heated causes the dark cherry glow of steel, which is noticeable already when heated to 550°C (1022°F), and at 850°C (1562°F) it turns into bright red, and then into orange (950°C, 1742°F), yellow (1000°C, 1832°F), and white (1300°C, 2372°F and above).
As you can see, the spectrum of thermal radiation depends on temperature, so observing the colors of quenching can be used to estimate the temperature of the metal, which is often used in heat treatment and forging, especially before the invention of non-contact thermometers. Names of glow colors: "red heat", "white heat", are often still used by metallurgists instead of determining the exact temperature.
The change in radiation color is due to an increase in the energies of internal interactions, excitation and relaxation of metal atoms, with increasing temperature. The higher the temperature, the more intense this radiation. Its spectrum is gradually enriched with short-wave radiation resulting from interactions with increased energy. Therefore, the main contribution of infrared radiation at low temperatures changes with increasing temperature to the visible light range and to ultraviolet radiation at very high temperatures. - An increase in temperature can cause oxidation of metal surface and the formation of an oxide layer on it. In the case of steel, such a layer can form a thin transparent metal film that remains when the temperature drops to room temperature. In this case, the surface of the metal acquires a rainbow colors. This is due to the fact that the surface is covered with a thin transparent layer and works like a mirror. When this layer is very thin, it reflects only certain colors from daylight, which is the result of interference.
Before the advent of pyrometers, this effect was also used as an indicator of the heating temperature of iron and steel. The colors were used to judge the heating temperature of steel chips and, consequently, the cutter during drilling and cutting operations. In modern times, it is used to create markings on the surfaces of ferrous metals and titanium by localized heating, including laser annealing. - If the steel is heated further, above 1300 °C (2372 °F, the specific temperature depends on the steel grade), melting of the metal can begin. Melting occurs because atoms acquire high energy and interatomic bonds are destroyed, and atoms lose their static positions in crystals and can travel around the material volume. This leads to the loss of the original shape and should be prevented during heat treatment of metals.
So we have briefly reviewed the obvious processes that occur with a metal when it is heated. However, changes in the properties of metals caused by heat treatment are due to a number of not so obvious reasons. These changes are due to changes in the metal structure, and we will discuss this in more detail.
What is the structure of metals and what depends on it?
Metals consist of totality of atoms arranged in an orderly crystal structure. Metals usually do not form a single crystal when solidified from the melt, but rather form a structure consisting of many small crystals. This is because there are a huge amount of crystallization centers inside the molten metal near the melting point. They begin to form when there is a significant loss of heat energy.
Four atoms are enough to form an elementary crystal unit cell. The number of such centers increases with cooling as more and more of them lose energy and begin to unite. Further, the crystallization centers themselves begin to grow, forming many microcrystals. They grow to a certain size depending on the cooling rate, the amount and nature of impurities, mechanical stress, and other factors. Crystals of the correct geometric shape are not formed because collisions with neighboring crystals prevent this, and their shape is distorted. Before complete solidification, the free growth of crystals stops, so in the fracture of a solidified metal we see irregularly shaped crystals called grains.
The properties of metals depend on the shape of these grains, and especially on their size, the arrangement of atoms in the crystals, and the relative position of the crystals. Additionally, the properties are affected by the composition and amount of alloying elements and various impurities that are inevitably present in metals such as steel, as well as affected by the cavities formed. Such grains can be visible or examined with a metallographic microscope or an electron microscope.
As the structure changes, the mechanical properties of the metal change too. The larger the grains, the lower the strength of the steel, not only due to the metal itself, but also due to the intracrystalline space in which contains less strong non-metallic impurities, such as sulfur and phosphorus, where they are concentrated during solidification. On the contrary, metals and alloys with a fine-grained structure have greater strength and higher hardness.
The transition of metals from liquid to solid is not always the final process of their structure formation. In many cases, secondary crystallization occurs, i.e. a change in the internal structure in the solid state. Secondary crystallization means that at a certain temperature, atoms rearrange and form a new crystal structure. To retain this or that structure in the final product, the part must be cooled. The cooling rate will also have a significant impact on the final state of the product. The change in steel properties during heat treatment is due to changes in the structure of the metal in the solid state.
Therefore, heat treatment is the process of heating the metal, holding it at a certain temperature and cooling it. The nuances of these simple steps create a variety of heat treatment methods that change the structure of the metal and, as a result, its properties.
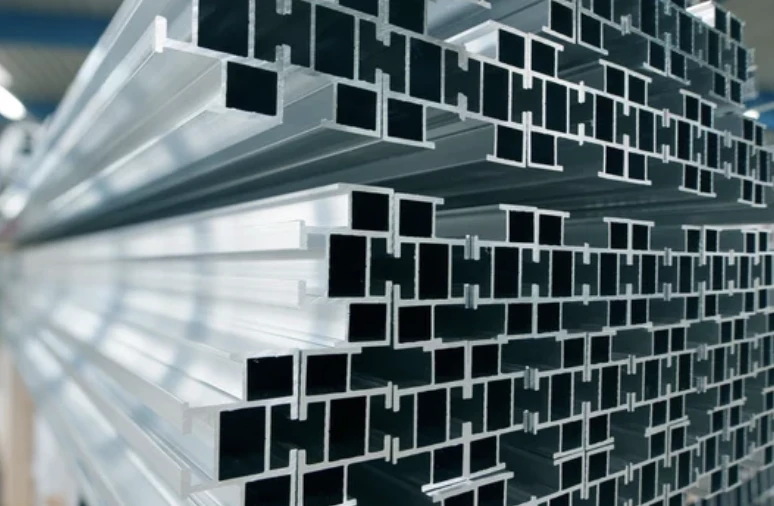
Benefits of Heat Treating
Heat treatment can make the final product more efficient in performing its tasks and more resistant to wear, and therefore more competitive. So below we list the benefits of heat treatment of metals.
1. Increase in strength and toughness
Heat treatment can change the microstructure of a metal, reduce grain size and increase grain number; under certain conditions, the crystal structure of the grains can also change (polymorphic transformation), which leads to changes in the mechanical properties of the metal.
For example, during quenching, a metal is heated to a high temperature and then rapidly cooled. This leads to crystal size and the formation of martensite, a microstructure with densely packed atoms that is the basis of hardened metal alloys. This structure provides greater hardness and strength of the metal.
Another way to increase metal strength is to temper it. After quenching, the metal is heated to a certain temperature and then cooled. This process reduces the excessive stiffness of the metal that can occur after quenching and preserves its strength.
There are also many other heat treatment methods that can affect the microstructure of the metal and its mechanical properties. For example, the heating and cooling cycle can be changed to achieve the desired result. The result of properly applied heat treatment processes can increase the tensile strength of steel by up to 50%.
2. Heat treatment can make steel softer
There is nothing paradoxical here. Changing the modes in the heating and cooling cycle can have a significant impact on the final result, so it is clear that levers of influence on the material structure can be applied in such a way as to achieve lower metal strength if this is the desired outcome. An example of this is hardening the surface of the metal while allowing the metal deeper in the product to remain soft. thus creating a thin layer of hard metal on the outside. This soft core makes the part resistant to breakage, absorbing stresses without cracking, while providing adequate wear resistance to the surface of the part.
3. Increased flexibility, reduced brittleness
One of the heat treatment methods for increasing the flexibility of metal is tempering. It is usually performed after metal hardening to reduce its rigidity and increase its flexibility. During quenching, the metal is heated to a high temperature and cooled rapidly to change its microstructure and increase its strength. However, this process can also make the metal brittle and easily breakable. Tempering is accomplished by heating the metal to a moderate temperature (typically 300 °C or 572 °F) and holding it at that temperature for a period of time. This process reduces the stiffness and increases the flexibility, ductility, and strength of the metal sample. Tempering is used in applications where it is important to have a metal that has a certain level of strength but is flexible and ductile enough to avoid tearing or brittleness during service. This procedure can also relieve stress and facilitate further machining.
4. Increased wear resistance
Gears, shafts, cutters, bearings, car body parts, tools, such as jackhammers, are just a short list of products where hardened metal adds extra strength and wear resistance, allowing them to operate under high stress without losing their functional properties. Heat treatment operations increase resistance to fatigue, allowing such steel components to work more efficiently over a longer period of time.
Extremely hard steels are often used as cutting tools that require sharp edges - heat treatment here is a critical operation to achieve long service life and shape retention. As noted, hard surfaces with ductile base materials can also be produced by heat treatment. Therefore, heat treatment returns a significant economic benefit due to the long service life of the resulting products.
5. Surface modification
In the process of heat treatment of metal, the surface may come into contact with air or other external gases and coolants at different temperatures. This inevitably leads to changes in its properties, which is also used in metalworking. In the case hardening process, metal is heated to high temperatures in an atmosphere of gas containing carbon (endothermic gas, natural gas, etc.) or nitrogen (ammonia), which react with the metal's surface to harden it. This process results in a hard, wear-resistant surface layer that also improves corrosion and abrasion resistance, while the core is relatively strong, allowing the steel to withstand impact loads.
6. Changes in thermal conductivity
The smaller the grain, the greater the thermal conductivity. An increase in the thermal conductivity of a metal is usually a side effect of heat treatment aimed at increasing the hardness of the metal. However, when thermal conductivity is a key property, quenching can be used to improve it in a targeted manner. For aluminum alloys used in the creation of radiators, the method of secondary phase hardening - planar hardening - is used. This method involves heat treatment of the alloy in such a way that secondary phases are formed in it, arranged in the form of flat dislocation walls. These walls provide excellent thermal conductivity of the material.
7. Changes in electrical conductivity
Reducing the grain size in general also improves electrical conductivity. Therefore, quenching and tempering methods are used in the creation of wires, contacts, soldering irons, electronic components, and other products where high electrical conductivity is important. Additionally, heat treatment processes are used in the production of electronic components to improve electrical and oxidation resistance or to produce thermocouples, where the accuracy of temperature measurement is important, which depends on the electrical conductivity of the metal.
8. Magnetic properties
Heat treatment can change the magnetic properties of metals. For the manufacture of permanent magnets, special materials are used that are heat-treated to improve their magnetic properties.
Heat treatment can also be used to reduce the magnetic permeability of metals, which is important in electrical devices where magnetic fields can cause undesirable effects such as inductance and magnetic losses.
9. Repair heat treatment
Heat treatment can be used to restore the structure of a metal after it has been worn or damaged. Metal wear is a complex process that results in a decrease in the strength and stability of parts due to external factors such as friction, corrosion, impacts, and others. In addition, during the operation of metal products made of hardened steel, a gradual destruction of the martensite structure can occur, which leads to a decrease in strength.
The process of restorative heat treatment may include quenching, normalizing, tempering, etc. It is used to restore metal products such as gears, shafts, pump wheels, and other complex parts that are subject to wear or damage due to operation. The rational use of this method can significantly increase the durability and reliability of long-term operation of metal products.
10. Variability of procedures and combinations of methods
Heat treatment of metals provides a variety of approaches that seem innumerable. However, they can be customized to achieve specific results. In addition, this process is well combined with other methods, such as mechanical or chemical processing. In some cases, a metal part may undergo several heat treatment procedures and other types of processing. The choice of the ideal method, however, really depends on the type of metal and the properties required, but in any case, it is necessary to test these properties to assess the effect of heat treatment on the mechanical properties of materials.
Recommendation for monitoring mechanical properties
When we talk about changes in metal properties, we primarily mean its mechanical properties, such as durability, tensile strength, wear resistance, dimensional stability, and toughness.
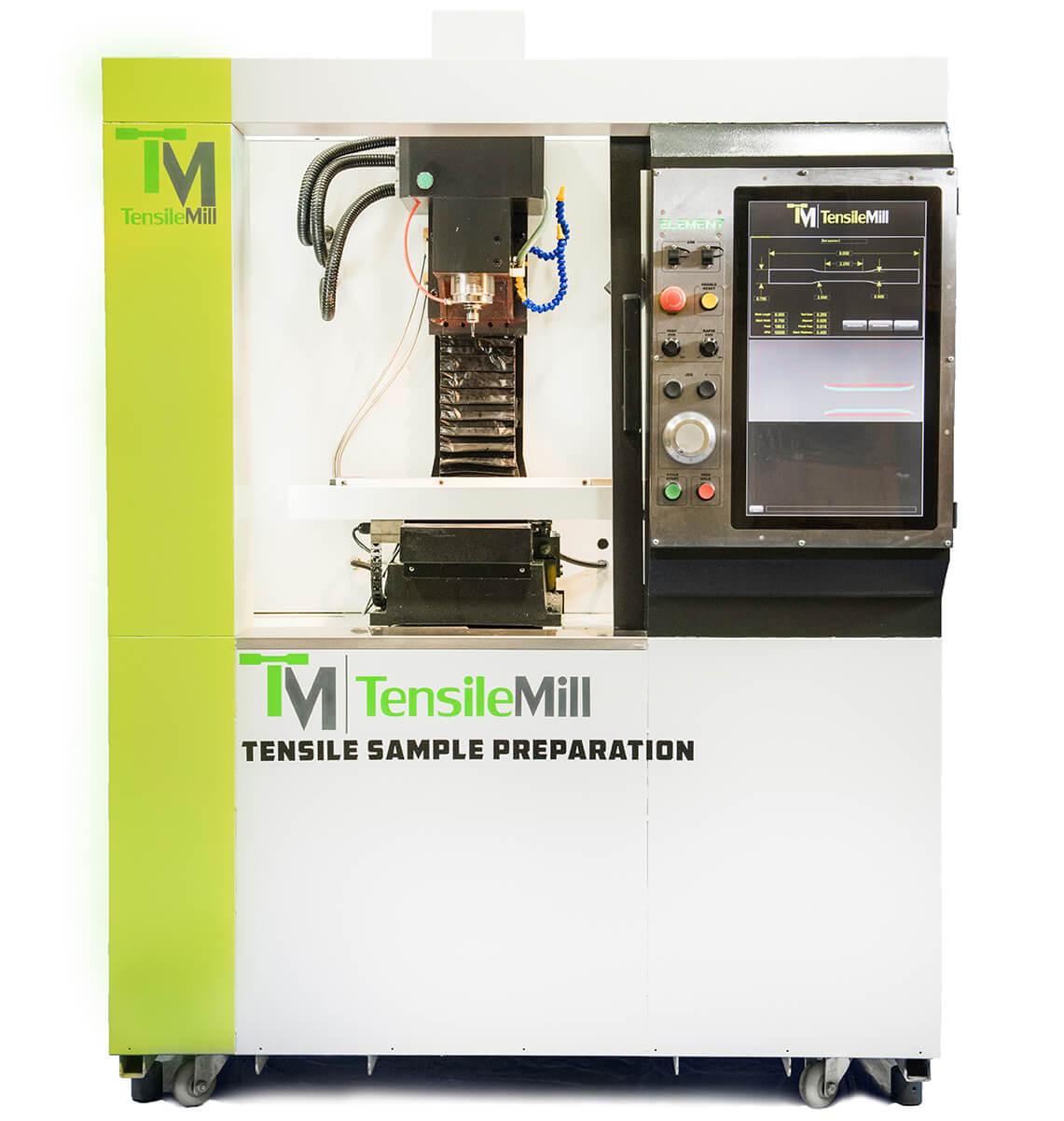
Recently, TensileMill CNC Inc., which is well known for its Flat Specimen Preparation Equipment Lineup (for dog bones) and Round Specimen Preparation machines, has entered the market with a new offer of its Tensile Testing Equipment. So now it supplies a complete set of equipment for the full-fledged testing of the main mechanical properties of metal - tensile testing. The TensileMill CNC Inc. equipment is well known for its reliability, ease of use and compliance with all manufacturing standards. We suggest that you consider adding Perfect Tensile Tester to your equipment fleet, as well as purchasing well-known machines with programmable control for Flat Specimen Preparation and Round Specimen Preparation. If you have any questions, please contact us.