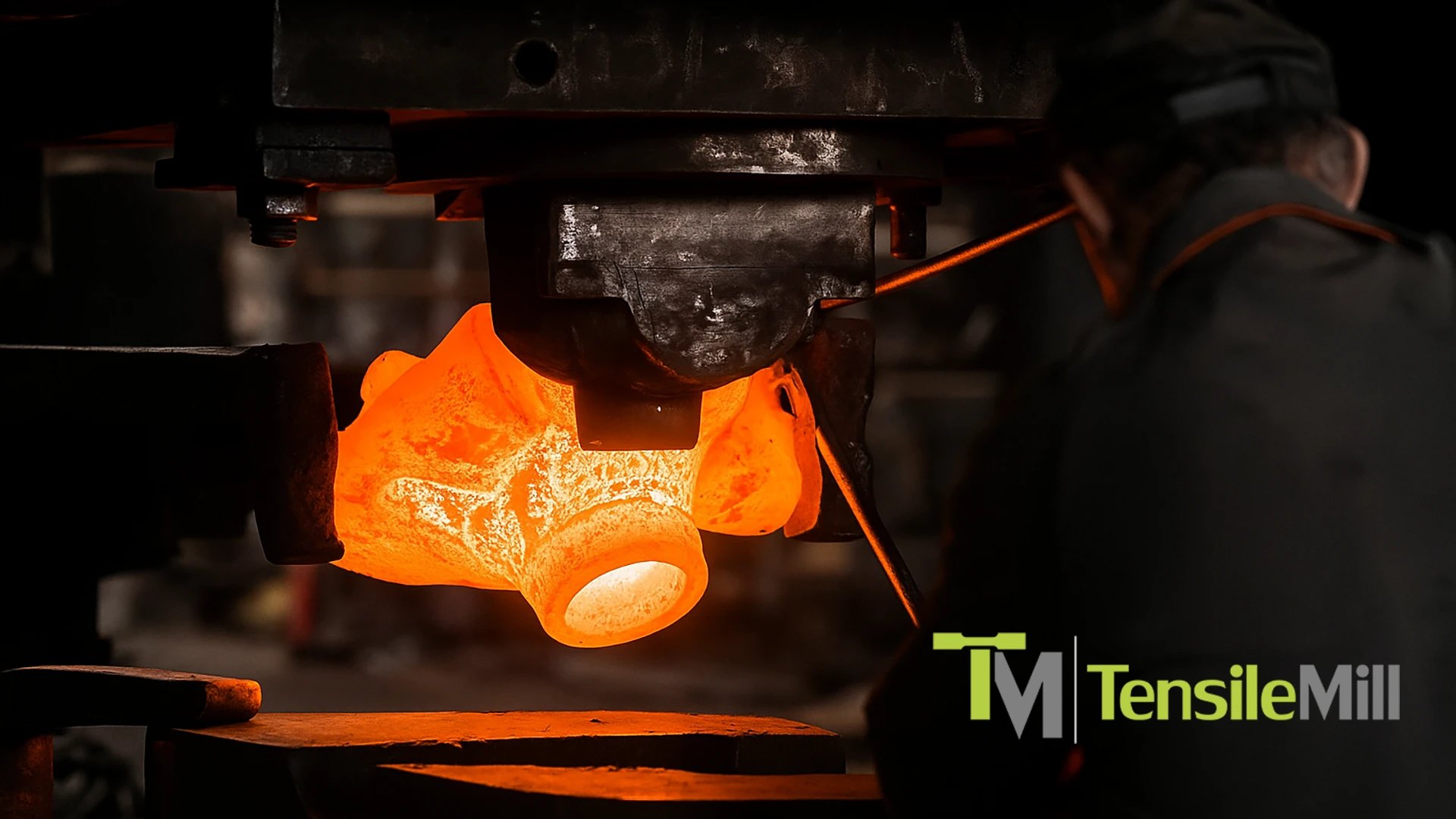
The strength of forged metal components can exceed that of comparable cast parts by as much as 26%. The metal is reshaped under high pressure during the forging process, resulting in an increase in strength. The process aligns the internal grain structure with the shape of the part, improving its mechanical properties. As a result, forging is often used to manufacture components for high-stress applications in the aerospace, automotive, oil and gas, and heavy machinery sectors.
Forged parts are not guaranteed to be defect-free, despite their high strength. If the process is not properly managed, cracks, voids, or inclusions may develop. If the mechanical properties of a forging do not meet the necessary standards, it may fail, regardless of its appearance. That is why quality control must take place at every stage of the forging process, from the selection of materials and the regulation of temperature to the post-forging inspections.
Tensile testing is one of the most effective methods to determine the quality of a forged part. The part's strength and ductility are directly measured by this method. It verifies whether the forging process and any heat treatment steps have achieved the desired outcomes. Focusing on the demands of forging, this article outlines how tensile testing helps detect process inconsistencies and validate that forged parts meet mechanical property requirements.
Tensile Testing: Principles and First Steps
Tensile testing is a destructive technique used to ascertain the mechanical properties of a material. A prepared specimen is pulled in a straight line until it fractures during this process. The applied load and elongation are monitored during the course of the test. Yield strength, ultimate tensile strength (UTS), elongation at break, and reduction of area are all calculated from this data.
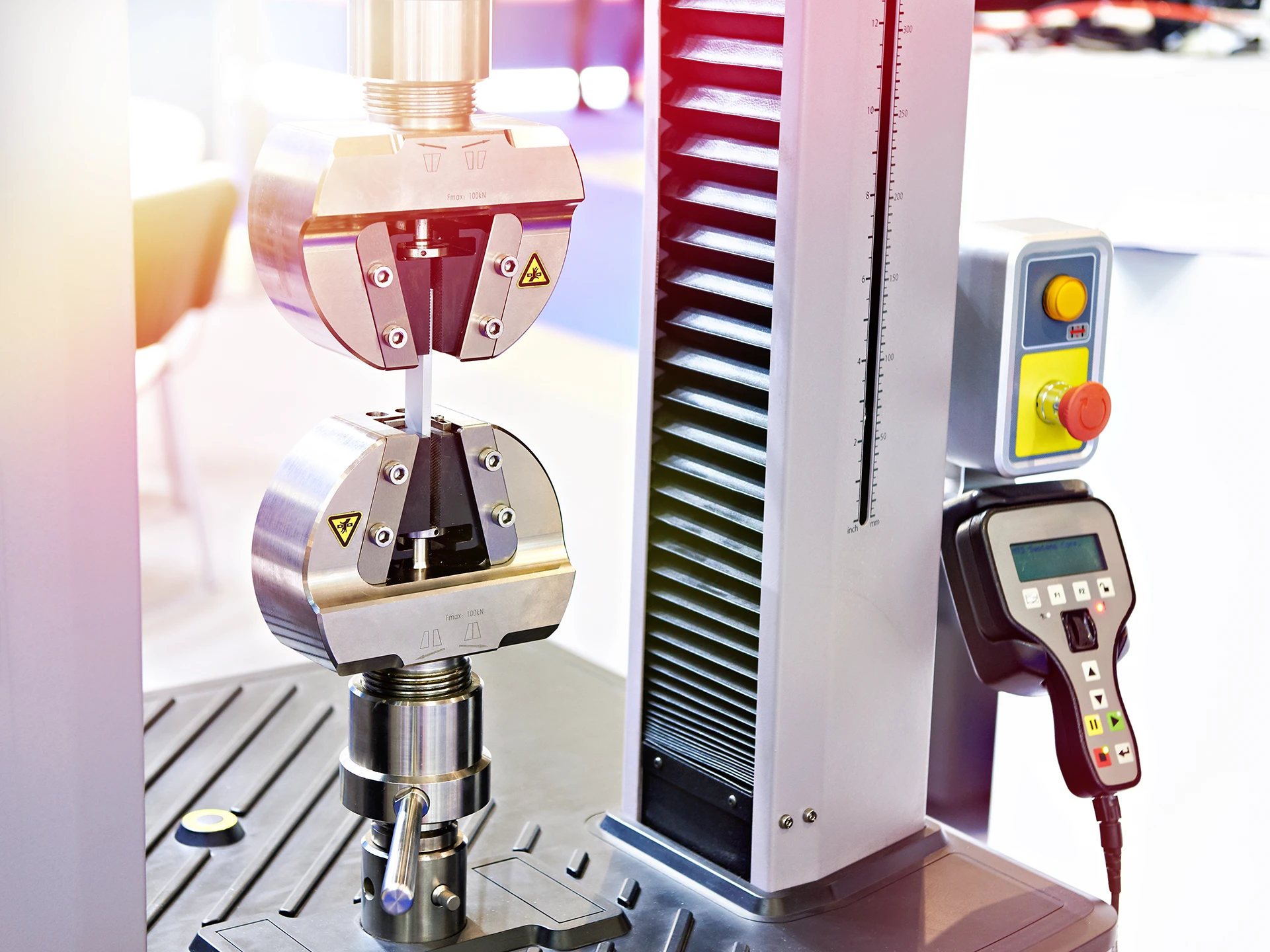
These values are indicative of the material's behavior under tension, including the maximum stress it can endure and the maximum distance it can be stretched before it fails. Typically, a universal testing machine (UTM) serves to conduct the test at room temperature. The specimen's shape, the test's speed, and the measurement system are all standardized to guarantee that the results are consistent and repeatable.
Before testing begins, the material must be cut and machined into a standardized specimen. This is usually done through the use of a CNC specimen preparation machine to make sure surface quality and tight dimensional tolerances. The objective is to develop a test piece that accurately represents the material's actual structure without the introduction of any artificial defects.
In industrial environments, tensile testing is conducted on a representative sample rather than the final product. This method enables engineers to evaluate the material's performance without causing any harm to the actual component.
Why Tensile Testing Matters in Forging QA Processes
In forging, each stage—from billet selection to final heat treatment—affects the mechanical properties of the part. Tensile testing is used at the final stage to verify whether the entire process has delivered the required performance. It is more than a test; it is a control point that determines whether or not a forged component is accepted.
Material flow, die behavior, and thermal gradients are variables that are challenging to accurately monitor in real time during forging. The internal grain structure and final strength can be influenced by these factors. The part may still fail under load if the mechanical properties are inadequate, even if the dimensional tolerances are met. Tensile testing provides the direct measurement to confirm those properties.
Tensile results are used by quality control teams to assess the consistency of the process. The forging, thermal treatment, and cooling have been executed correctly when the test meets all target values. Immediate investigation is initiated in the event of a test failure, regardless of whether it is a thermal imbalance, material issue, or process deviation. This feedback loop is valuable in production, particularly when managing high volumes or safety-critical components.
Tensile testing is also a compliance requirement in many sectors. Certified reports may be requested by clients to verify that each batch meets the minimum ductility and strength standards. For instance, a forged gear may be required to satisfy a UTS of 950 MPa and 14% elongation.
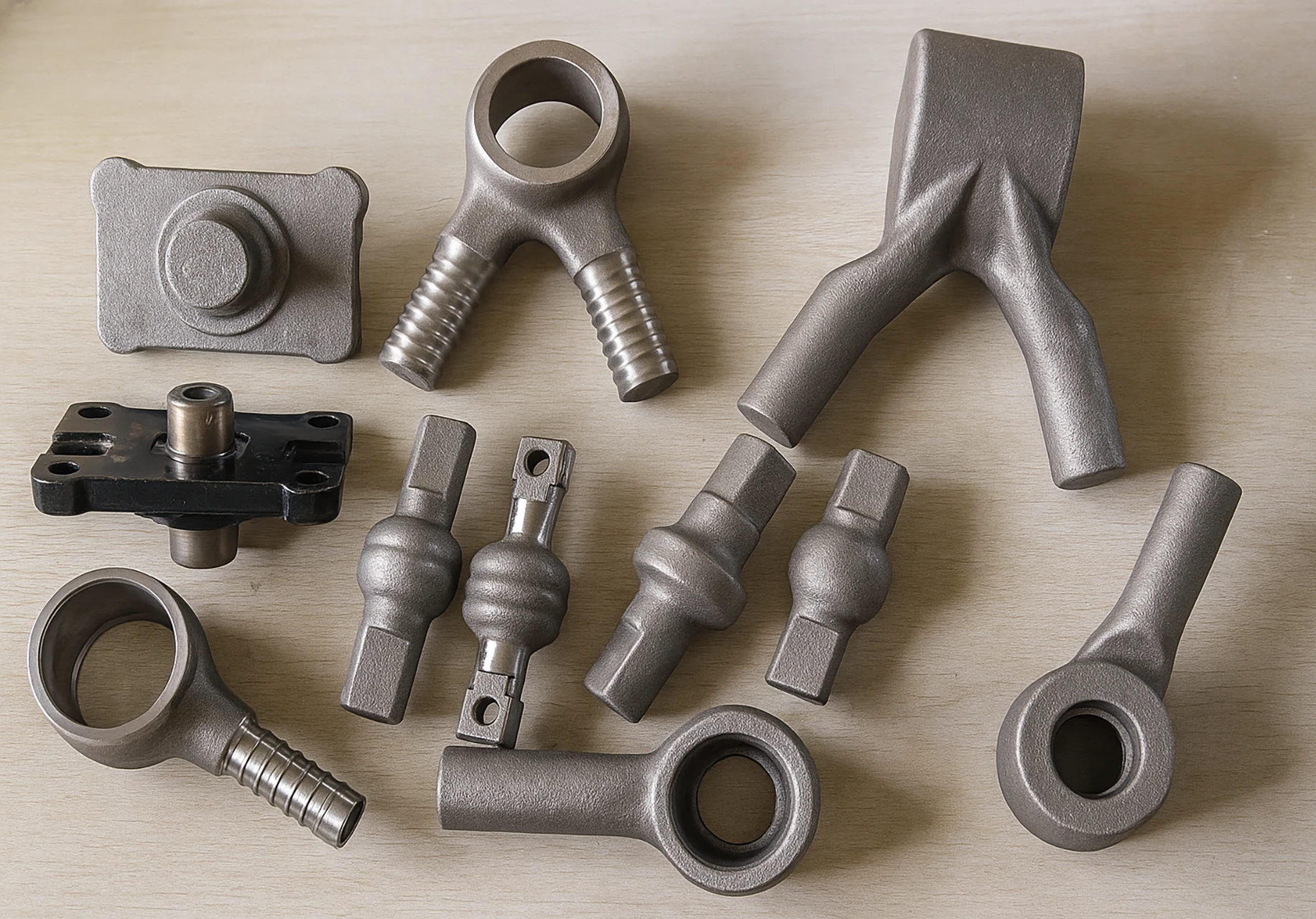
Applying Tensile Testing in Forging Production
In practical forging operations, tensile testing is not performed on every part. Instead, manufacturers implement strategic testing routines to balance quality assurance with production efficiency.
Sampling Frequency and Lot Testing
Tensile tests are generally scheduled for each heat treatment batch, alloy melt, or production lot. Tensile tests take place during each of these critical production stages to comply with standards such as ISO 15461. In open-die or ring rolling forge processes, it is common to conduct one test per melt or per heat treatment charge. Sampling plans, which are frequently statistical in nature, specify the number of samples to be tested for high-volume components such as automotive gears, typically 2–3 per 100 units.
Role of Sacrificial Forgings
When it is impractical to add test coupons on every component, manufacturers create sacrificial forgings under identical forging and thermal conditions. Some standards require materials to be tested at one-quarter thickness from the surface, with specimens reflecting the actual production geometry. This approach guarantees representativeness without causing harm to end-use components.
Managing Scrap vs. Test Yield
QA teams are obligated to maintain a balance between quality assurance and scrap cost, as tensile testing results in sample destruction. Prolongations or test lugs that can be removed after forging are frequently included into designs for large or valuable forgings. This helps preserve the value of the main component by avoiding unnecessary waste. In batch production, sacrificial specimens are allocated to minimize cost while maintaining traceability.
Integration into QA Workflows
Tensile testing forms a key part of the broader forging QA system:
- Process planning defines test frequency and melt validation steps.
- Production includes forging with provisions for coupons or sacrificial pieces.
- Heat treatment is documented per batch.
- Tensile testing follows, with specimens taken from representative sources.
- Results are logged and compared against specifications (e.g., UTS ≥ 900 MPa and elongation ≥ 15%).
- Outliers prompt investigation, leading to process adjustments or batch rejection. This creates a controlled loop that maintains production integrity even at high volume.
Tensile Testing Equipment for Forging Applications
At TensileMill CNC, we specialize in providing high-performance tensile testing equipment built to meet the rigorous demands of forged material testing. Our product line includes universal testing machines for executing tensile test procedures, CNC tensile specimen preparation systems, and polishing machines designed specifically for surface preparation of tensile samples.
If you are interested in acquiring dependable, standards-compliant equipment for testing forged materials, we invite you to explore three of our most reliable solutions below:
Servo Hydraulic Universal Testing System – TM-SHM Class A
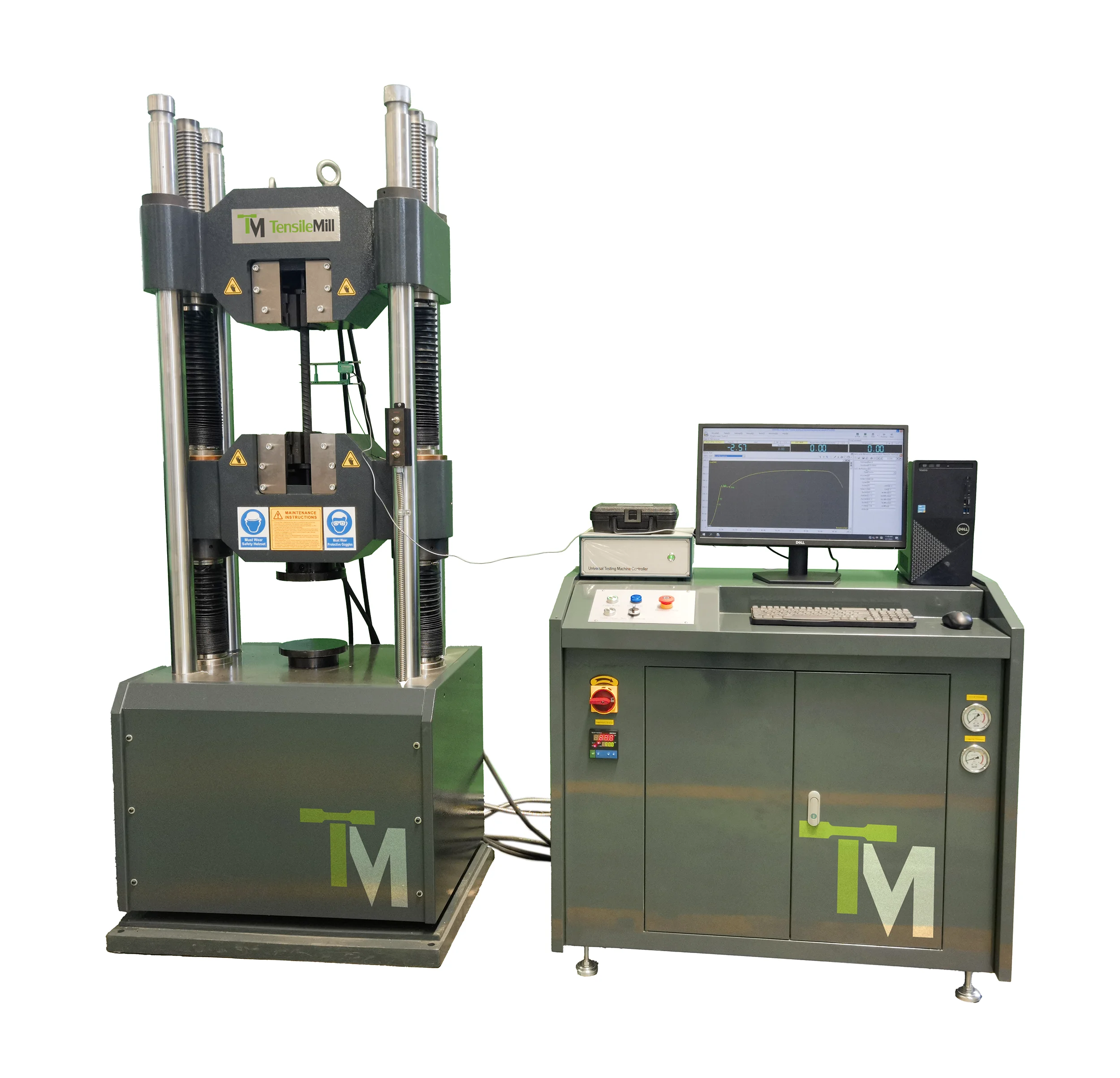
The Servo Hydraulic UTM Series is an excellent choice for testing forged shafts, gears, and structural parts, as it is primarily made to handle heavy-duty forged components with capacities of 600 kN and 1000 kN. This system relies on a high-precision load cell to directly measure force, surpassing oil-based systems used in lower-grade machines with an accuracy of ±0.5%. The rugged 4-column frame guarantees long-term stability, while the dual test space supports both tensile and compression procedures. It is a key element of quality control workflows due to its support for all major international standards (ASTM, ISO, JIS, BS), advanced software, and integrated safety systems.
TensileMill CNC – Classic Upgrade
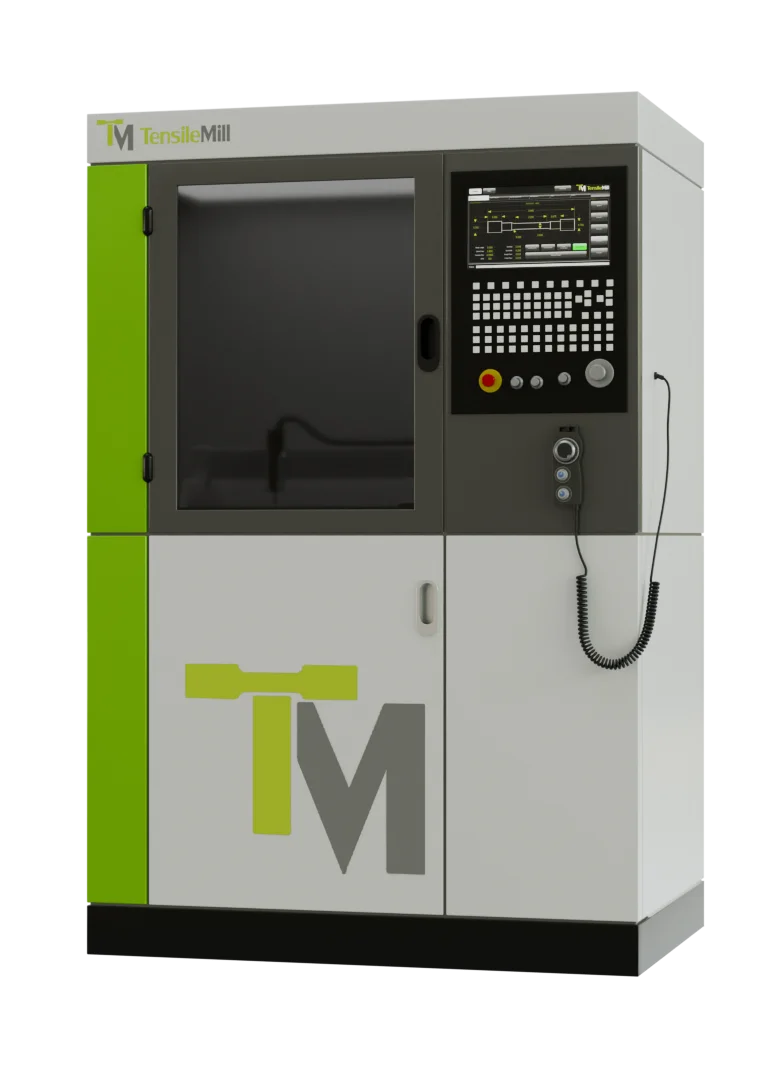
The Classic Upgrade is a hybrid CNC system that is meant to prepare flat tensile and impact specimens and is fully compliant with ASTM E8 and ASTM E23. It can process up to 8 metal samples at once and guarantees repeatability to within 0.0003” in conjunction with an industrial-grade servo motor and FANUC control system. The system is capable of accepting specimens with a hardness of up to 60 HRC and provides a rapid setup process for U- and V-notch impact samples. The Classic Upgrade is the optimal CNC solution for forging labs and production environments, as it greatly minimizes prep time and operator error due to its rugged cast iron frame, integrated specimen libraries, and automated clamping.
Automatic Longitudinal Polisher – TensilePolish GR04

The TensilePolish GR04 is a fully automated polishing system that is configured to prepare both cylindrical and flat tensile specimens for final testing. It performs longitudinal, low-stress polishing to remove surface artifacts that could affect test outcomes. The system offers the ability to adjust the polishing length, speed, and pressure to meet standards such as ASTM E466, ASTM E606, and NADCAP. To prevent surface damage, it maintains one-time contact per area and automatically switches between up to four grades of sandpaper. This unit stands out by its intuitive touchscreen interface and model adaptability for large, small, or flat samples.
Final Thoughts on Tensile Testing in Forging
Tensile testing is critically important for guaranteeing the mechanical reliability of forged components. As one of the most direct and trusted methods for validating the performance of forged parts, tensile testing is capable of identifying inconsistencies introduced during heat treatment or deformation, as well as confirming material strength and ductility.
The modern forging quality control process integrates easily into this method through precise data interpretation, controlled testing environments, and standardized specimen preparation. Whether used in high-volume automotive gear manufacturing or large-scale structural part production, tensile testing offers manufacturers the necessary data to satisfy internal specifications and external compliance requirements.
Tensile testing supports both production efficiency and safety assurance when combined with strategic sampling practices, the use of sacrificial forgings, and reliable test equipment. It facilitates the integration of material design and real-world application, enabling forged components to satisfy the rigorous requirements of contemporary industries.
Should you require any further information regarding our tensile testing equipment or require assistance in determining the optimal solution for your forging application, please do not hesitate to reach out to us. We are here to help you choose the right solution for testing.