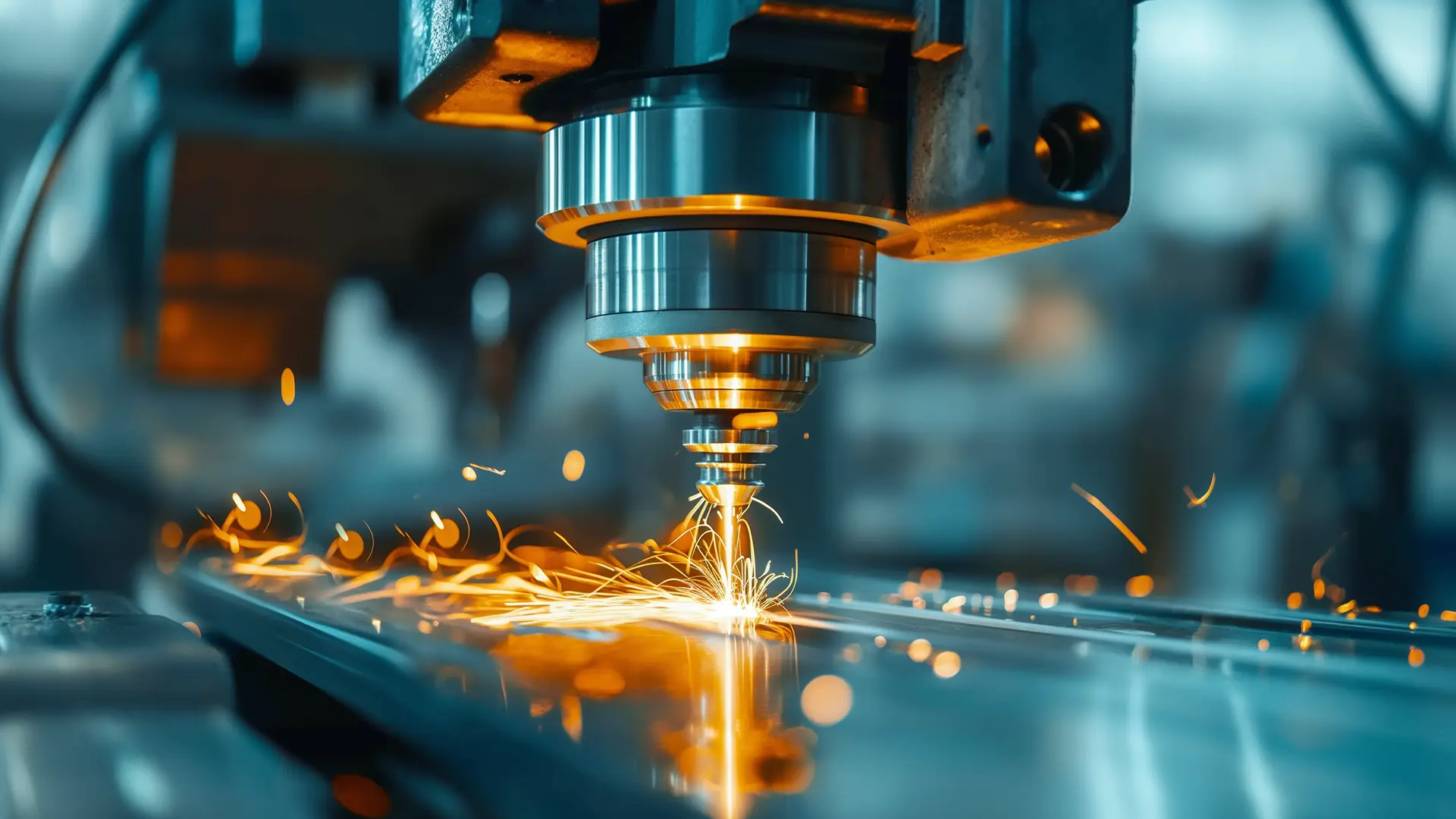
From milling to laser cutting, CNC (Computer Numerical Control) machines have become indispensable in the fabrication of items in nearly every sector - from constructing spacecraft to producing furniture that fills our homes and offices. These machines are present in virtually every facet of modern manufacturing, undertaking tasks that would be almost impossible for human hands alone.
The history of CNC machining dates back to the 1940s, spurred by computer technology and production automation. Since then, each year has brought remarkable advancements that directly influence global manufacturing processes. Considering the capabilities of current CNC machines, it is intriguing to contemplate how this sector will evolve in the future and what we can expect in terms of manufacturing processes and beyond in the coming years.
Today's discussion will explore what the near future may hold for CNC technologies. We will focus on how numerical control can benefit production processes in a variety of industries and also focus on how future machining technologies will behave in one of the initial stages of production - material testing.
Understanding CNC Machining and Its Broad Applications
CNC machining represents a method of manufacturing that uses computerized controls to manage machine tools with high precision. This approach automates the production process, allowing for the efficient creation of parts and components with intricate designs and tight tolerances. CNC machining operates in a broad range of materials, including metals, plastics, and composites.
The adoption of CNC machining has revolutionized many industries by providing an effective method for producing complex geometries that are difficult or impossible to achieve through manual processes. For instance, in the aerospace sector, CNC machining is fundamental for fabricating components that must endure harsh operational environments. Similarly, the medical field relies on this technology for manufacturing vital surgical instruments and custom implants, providing both precision and adaptability to diverse medical requirements.
The broad application of CNC machining is supported by an array of machine types. CNC milling machines, for example, are incredibly adaptable and widespread. They operate by rotating a cutting tool to remove material, which is ideal for creating all kinds of shapes and surfaces. Lathes, another common type of CNC equipment, produce flat and round parts. CNC grinders provide exceptional surface finishes, grinding down materials to achieve fine, detailed shapes and features with high accuracy.
CNC routers extend the capabilities of traditional milling machines by accommodating a greater range of materials, including wood and plastics. They serve industries like furniture making and general carpentry with the same level of precision and efficiency attributed to metalworking. The advent of multi-axis CNC machines, including 5-axis and 6-axis variants, opens up new possibilities, allowing for the production of parts with complex topographies that were previously unattainable. The ability of these machines to pivot and rotate around multiple axes reduces the need for multiple setups, increasing production speed and reducing errors.
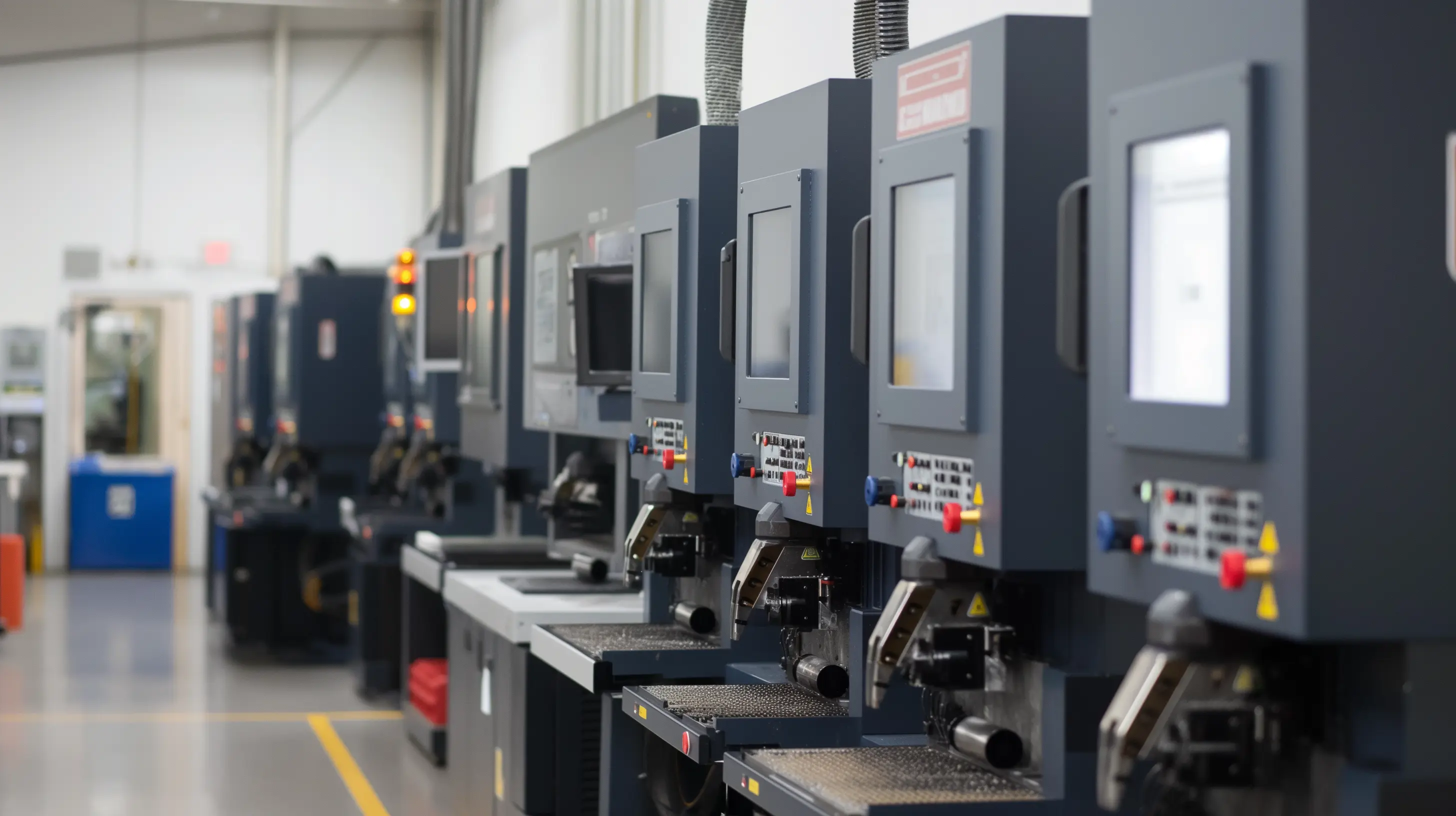
The Growing Importance of CNC Machining in Modern Manufacturing
During the past several decades, CNC machining has dramatically transformed manufacturing by automating processes that were once manual, labor-intensive, and prone to error. This automation is powered by sophisticated computer software that directs machine tools with precision, allowing for the production of complex and highly detailed parts that manual techniques could not achieve. CNC machines' ability to operate continuously with minimal human intervention improves productivity and reduces errors, leading to more consistent and higher-quality output.
Financially, CNC machining proves to be highly cost-effective in the long run. Despite the high initial investment in CNC equipment, it significantly reduces production costs by minimizing waste, optimizing raw materials, and decreasing the need for frequent tool changes and maintenance. This cost efficiency is further bolstered by the technology's capability to execute multiple manufacturing processes simultaneously. This not only speeds up production but also reduces energy consumption compared to traditional machining methods.
Moreover, CNC technology plays a key role in fostering rapid prototyping, allowing businesses to iterate and refine products swiftly. This capability is invaluable in industries where being first to market with an original or improved product can be a critical competitive advantage. Prototyping, which once took weeks or even months, can now be accomplished in days or hours.
Insights into AI's Role in CNC Machining
As of 2024, artificial intelligence (AI) has become one of the most prevalent topics, particularly within CNC technologies. AI is perfectly suited to integration into CNC machines, offering new capabilities and functionalities that continue to evolve and expand.
There is no doubt that AI's introduction to CNC machining has profoundly increased their efficiency and precision. For instance, AI algorithms enhance automation by optimizing g-code and m-code programming, integral components of CNC operations. This optimization allows CNC machines to operate at peak efficiency, drastically reducing cycle times and minimizing material waste. Moreover, AI assists in simplifying the CNC workflow by automating tedious tasks such as tool path creation and code post-processing.
Looking into the future, AI's role in CNC machining will continue to grow. Innovations continue to take place, such as real-time data analytics for predictive maintenance, which minimizes downtime by anticipating machinery maintenance needs before they arise. Furthermore, AI significantly improves initial machining processes by automating and optimizing CNC programming, cutting down on programming time significantly and increasing output accuracy. It is not only about speed but also about increasing CNC machining precision through the use of artificial intelligence, suggesting possible strategies and predicting challenges to prevent errors and reduce waste.
These advancements are setting the stage for a future where AI-driven CNC machines can operate continuously, maintaining high levels of production without human intervention. AI is indeed reshaping CNC machining, making it a key player in the manufacturing sector's ongoing evolution towards more automated and intelligent systems.
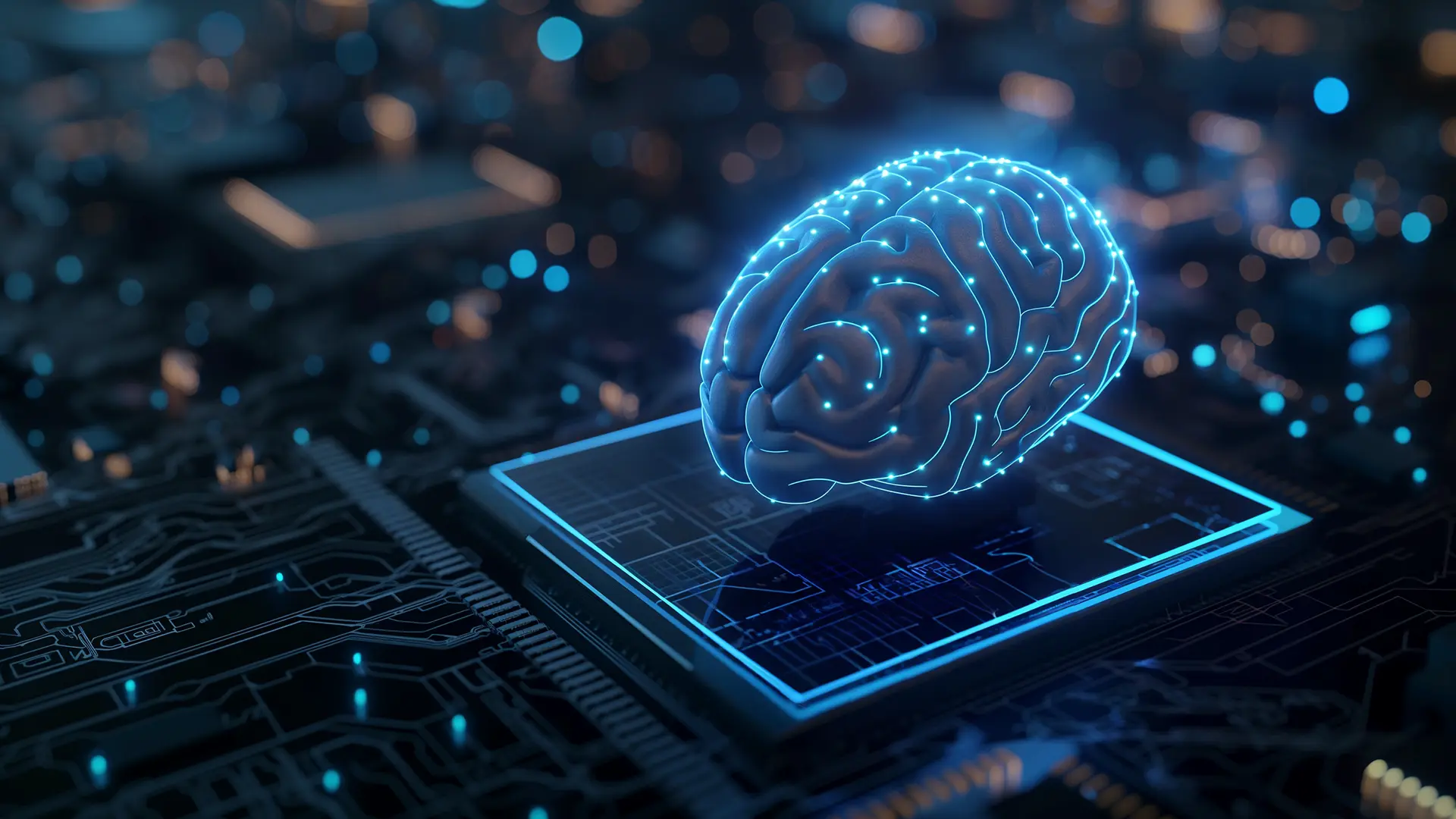
Future Technologies in CNC Machining
Building on the trend of AI's integration into CNC machining, the future of this technology is set to be redefined by several other promising trends that are expected to boost efficiency, precision, and sustainability in manufacturing processes.
Predictive analytics is becoming a cornerstone of CNC operations, leveraging large amounts of data to forecast machine maintenance needs. Thereby, in its turn, minimizing downtime and extending equipment lifespan. In addition to improving operational efficiency, this proactive approach also significantly reduces the costs associated with unexpected machine failures.
Internet of Things (IoT) integration is another transformative trend on the horizon. IoT devices collect and transmit real-time data, allowing for more precise monitoring and control of CNC machining processes. This connectivity enables a smooth flow of information between machines and operators, leading to more informed decision-making and optimized production processes.
Moreover, machine learning continues to refine CNC technology by providing the capability for machines to adapt their operations in real-time to different conditions and requirements. This adaptability makes it possible to manage complex production lines and customize manufacturing processes to specific project needs without extensive manual reprogramming.
Looking further ahead, the combination of additive and subtractive manufacturing methods is set to reshape CNC shops. This hybrid approach allows for the fast prototyping and production of complex designs with high precision, while also minimizing material waste and energy consumption.
Additionally, as digital twin technology advances, it will become increasingly important in sustainable CNC practices. By creating accurate virtual models of physical CNC systems, manufacturers can simulate and optimize operations without physical trials. As a result, not only is material conservation optimized, but process adjustments can also be tested in a risk-free virtual environment, resulting in more sustainable and efficient manufacturing workflows.
CNC Machining Future Innovations in Material Testing
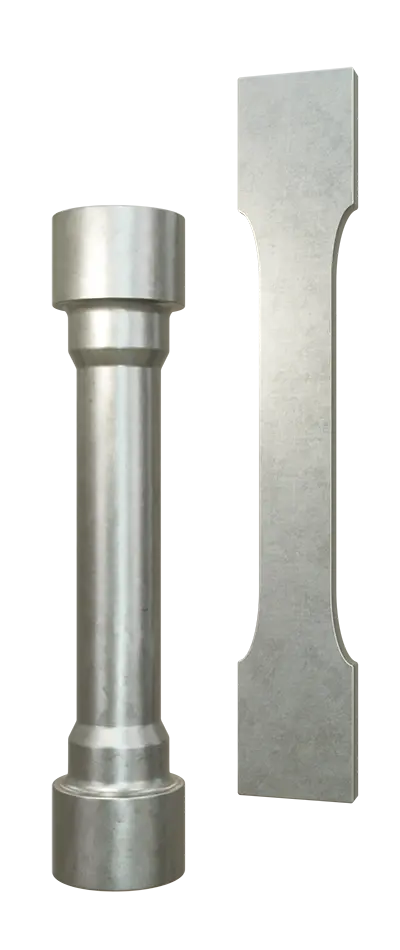
CNC machining is also rapidly becoming more and more relevant in material testing, particularly in the preparation of test specimens. This is most evident in tensile testing, which requires specific specimen shapes, such as flat (dog bone) and round specimens. A CNC machine is indispensable in the production of these samples, as they must meet precise dimensional standards in order to yield accurate results.
For flat tensile specimens, which are often used to test materials in sheet, plate, or thin film forms, CNC milling machines or laser cutters are typically used. These tools are ideal for creating detailed, precise cuts for materials used in critical applications such as aerospace or automotive parts. CNC milling provides the robustness needed for handling hard materials. Laser cutting offers a contact-free method that minimizes physical stress and material deformation, which could skew testing results.
Round tensile specimens are usually crafted from cylindrical stock, making CNC lathes for turning centers the equipment of choice. These machines are particularly effective at producing uniform, cylindrical shapes by rotating the material against a cutting tool, achieving high dimensional accuracy is essential for consistent testing outcomes.
Moreover, the development of universal CNC machines that integrate both milling and turning capabilities could significantly streamline operations in material testing labs. Such machines would not only economize space but also provide the flexibility to switch between preparing flat and round specimens without multiple setups. Enhanced with AI and machine learning, which we have already mentioned, these hybrid machines could autonomously adjust machining parameters in response to real-time feedback on material properties and desired outcomes.
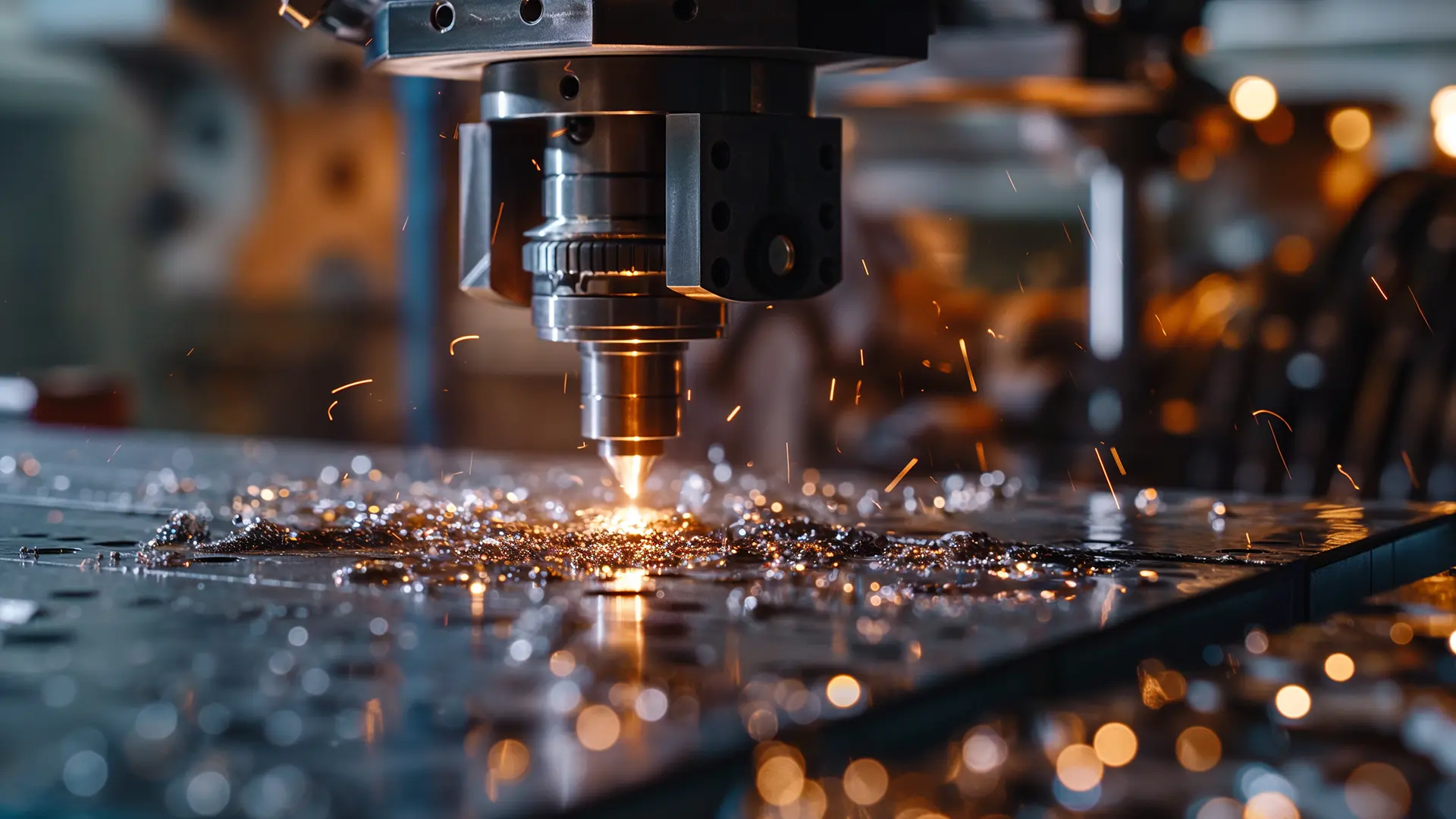
Will CNC Machines Become More Expensive Over Time?
The continuous evolution and integration of modern technologies such as automation, advanced sensors, and artificial intelligence are driving up CNC machine initial costs. For example, the incorporation of these high-tech components and the complex software needed to operate them contribute to the overall cost increase.
However, these advancements also make CNC machines more capable and efficient. The use of automated processes and intelligent systems within CNC machines speeds up production but also maximizes precision and reduces waste and energy consumption. This means that while the upfront cost of a CNC machine might be higher by, say, 30% due to these enhancements, the return on investment could be significantly greater due to a 50% increase in operational efficiency. This efficiency comes from faster production times, lower energy costs, and reduced material waste, which collectively contribute to a lower total cost of ownership in the long run.
Thus, while the sticker price of CNC machines may increase, the expansion in capabilities and the subsequent increase in production efficiency and market reach justify the higher initial expenditure. This makes it a worthwhile investment in manufacturing's future.
Will AI Fully Replace Humans in Manufacturing?
As of now, AI has been shown to significantly increase productivity and operational efficiency in manufacturing, but it cannot fully replace human labor. The key reasons stem from a number of innate human qualities and workplace dynamics that AI currently cannot replicate or substitute for.
Firstly, AI and robots excel at routine, structured tasks where predictable outcomes are derived from defined variables. However, they lack the emotional intelligence, creativity, adaptability, and personal judgment humans bring to more complex and nuanced tasks. Jobs that require a deep understanding of human emotions, cultural nuances, or ethical considerations remain poorly suited to full automation.
Secondly, AI depends entirely on the data provided to it and lacks the ability to think beyond its programming. This becomes a significant limitation in situations that require on-the-spot problem-solving or decision-making based on new and unforeseen circumstances. Moreover, in the creative fields, human insight and the ability to connect disparate ideas in innovative ways are capabilities that AI has not been able to emulate effectively.
Furthermore, while AI can automate many operational processes, the interaction between automation technology and skilled workers is extremely important. The human workforce is still needed to manage, maintain, and provide oversight over AI systems. The role of humans in interpreting complex AI outputs, ensuring ethical AI usage, and providing a personal touch in customer interactions remains irreplaceable. Jobs that entail building relationships, negotiating, and empathizing are areas where AI falls short compared to human capabilities.
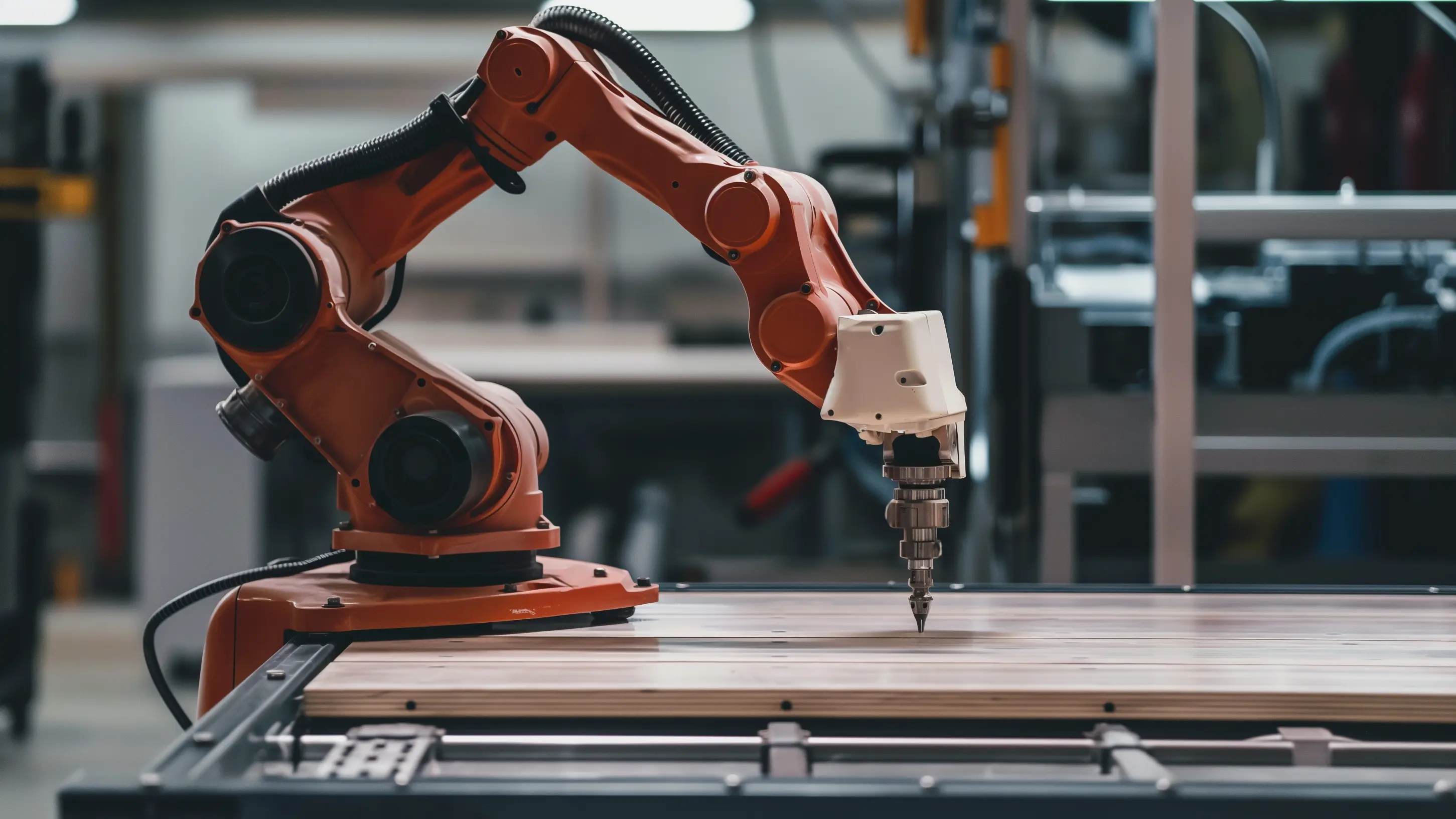
Innovative Equipment for Tensile Sample Preparation
While a universal machine that can perform all tasks has not yet been invented, and since we have touched on the topic of tensile sample preparation, we want to introduce you to our products. These machines are among the most suitable choices for preparing flat and round specimens of our time. Therefore, they are highly likely to be your preferred solution if you are looking for CNC machines for tensile sample preparation, whether for round or flat specimens.
TensileMill CNC MINI for Flat Tensile Specimen Preparation
Transitioning from general advancements in CNC machining for tensile sample preparation, we highlight a specific product that exemplifies these technological strides - the TensileMill CNC MINI. This compact flat tensile test sample preparation machine has been specifically designed to offer ultimate flexibility and full CNC machining capabilities, all within a notably small footprint. Despite its size, the MINI model is a powerhouse, recently upgraded to surpass our Classic model in virtually every parameter. It now features a larger table size, higher power, and improved precision & repeatability, all at a competitive price.
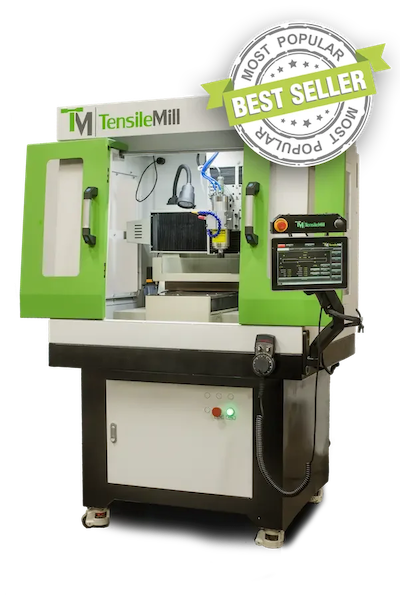
The TensileMill CNC MINI is ideal for laboratories or facilities with limited space but requires high-quality tensile specimen preparation. It is especially suited to untrained CNC machinists due to its user-friendly interface. Equipped with a 10" LCD screen and our renowned Tensile Software, the machine simplifies preparation. Operators can quickly input the required tensile specimen dimensions according to ASTM, ISO, DIN, JIS, or other industry standards through its intuitive interface. Once the parameters are set, the machine is ready to mill in seconds, handling materials ranging from soft metals to hard Inconel with its robust 2.2kW (3hp) Water Cooling Spindle.
TensileTurn CNC - Industrial Upgrade for Round Tensile Samples
Building on the strengths of the TensileMill CNC MINI, the TensileTurn CNC - Industrial Upgrade is another example in our lineup, specifically engineered for round tensile sample preparation. This compact CNC lathe, designed for industrial use, is built to craft precise round tensile specimens, providing the highest accuracy in tensile testing results. The machine's interface is remarkably user-friendly, equipped with a touchscreen that allows operators, regardless of their experience level, to easily select and prepare specimens in compliance with a number of standards, including ASTM, ISO, and DIN.
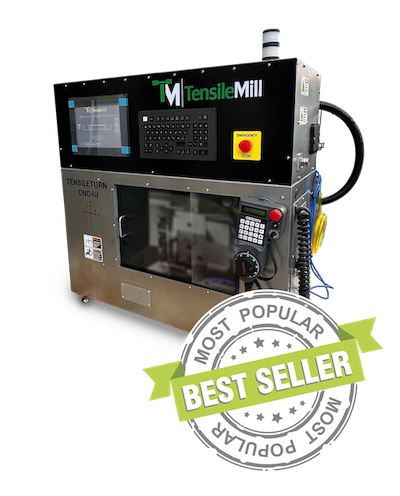
The TensileTurn CNC - Industrial Upgrade is not only known for its operational simplicity but also for its comprehensive capabilities. It can work with an array of materials and specimen shapes, from standard round to sub-size and threaded specimens, even complex shapes like button-head tensile bars and fatigue specimens. This degree of flexibility is backed by automation features like automatic center drilling, which simplify the specimen preparation process, significantly reducing the turnaround time from stock to testing.
What truly sets this machine apart is its ability to integrate easily into any testing laboratory or industrial setting. With its small footprint, it occupies minimal space while delivering performance that rivals larger, more cumbersome equipment. This model represents a turnkey solution for high-quality specimen preparation, promising consistent and repeatable results that can profoundly impact tensile testing outcomes.
Concluding Thoughts on CNC Machining in the 21st Century
CNC machining continues to be a cornerstone of modern manufacturing, revolutionizing the production process from aerospace to medical sectors. With the integration of advanced technologies like AI and IoT, CNC machines have not only become more efficient but also more capable of handling complex tasks with precision and minimal waste. These technological advancements, while potentially increasing initial costs, offer significant improvements in speed, energy efficiency, and overall productivity, which can offset the higher investment required.
Furthermore, the role of CNC machining in material testing, particularly in the preparation of tensile specimens, highlights its adaptability and relevance to the guarantee of the reliability of different materials. The future points towards even more integrated and multi-functional CNC systems, increasing their usefulness and indispensability in modern manufacturing setups.
At TensileMill CNC, we remain at the forefront of these innovations, particularly in tensile testing. Whether you are looking for top-tier equipment or specialized services, we invite you to contact us directly or request a quote. We are prepared to offer solutions that are customized to meet your specific needs, making certain that you receive the most effective and efficient tools for your manufacturing and testing requirements.