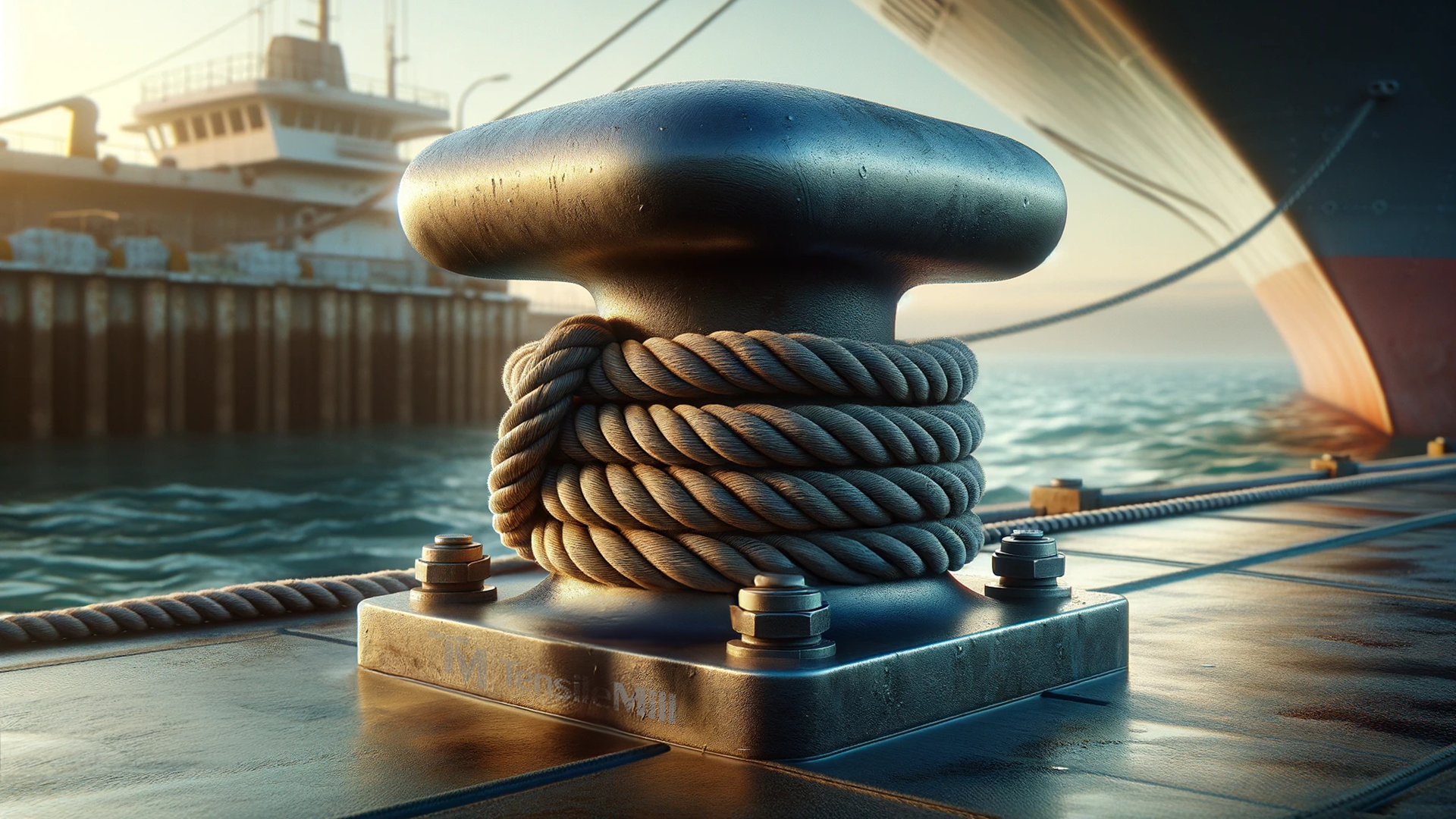
Have you ever thought about how gigantic ships withstand powerful waves and strong storms, continuously traveling across our huge oceans? It reaches beyond bolting metal parts together. It's about a complex strategy aimed at providing exceptional strength from the beginning of the shipbuilding process. The objective is clear: to create structures that not only withstand but also succeed under the mighty ocean's demands, ensuring secure and effective transportation across the vast expanses of water that connect our world.
Delivering approximately 11 billion tons of goods via sea yearly requires ships to be more than just massive. They must also be characterized by exceptional strength and reliability. Crafting a ship demands detailed and meticulous efforts, focusing on creating a ship capable of enduring the relentless conditions of the sea.
Taking a closer look, we find that the manufacturing approaches used in shipbuilding are crucial to ensuring the longevity and safety of maritime structures as well as maintaining the efficiency of global trading networks on a global scale. The metals selected for ship construction are subjected to strict testing and quality assurance from the start. This ensures they can withstand decades of the ocean's punishing conditions without becoming damaged.
In this article, we'll explore the crucial role of ship strength in manufacturing processes, spotlighting the key elements of smart design, cutting-edge manufacturing, and rigorous material testing. These factors collectively guarantee that the giant ships of the sea are prepared and well-equipped to meet and overcome the challenges of the ocean. Specifically, we'll highlight the indispensable role of metal testing in ensuring the integrity and durability of these maritime giants. We will take a look at the detailed processes behind the creation of impressive ships and how they maintain their sturdy and graceful performance across the oceans.
Understanding Ship Strength
When we think about a ship's strength, it's all about how it's built and what it's made of. Ships need to be strong - traveling across huge oceans is no easy task! So, how do we ensure that these massive vessels don't break under pressure and withstand the sea forces? Let's take a look.
In simple terms, a ship's "skeleton" is mostly made from tough metals, with steel often taking the lead. This is because steel is strong and doesn't easily bend or break, even when facing the powerful, salty ocean. The ship's body, or hull, is its first shield against tough sea waters. It has to keep everything - and everyone - inside it safe and sound while also cutting through waves, sometimes gentle, sometimes not.
Choosing the right metal is crucial and isn't just about picking the cheapest or most available option. Metals are tested to see if they can resist rust and handle heat without losing their toughness. This is especially critical for parts like an engine that runs hot. Some metals need to be light, like aluminum, which resists rust. Others, like iron, need to handle heat and pressure, especially in engine parts.
In short, ships are built from a mix of different metals, each chosen for its special characteristics. This ensures they're able to tackle sea travel challenges but also do it successfully, trip after trip. The tests these materials run through before becoming part of the ship are crucial, ensuring they're up to the task and won't let the vessel down when it's out on open waters. Moving forward, we'll see how these materials are chosen and tested to build reliable, ocean-conquering ships.
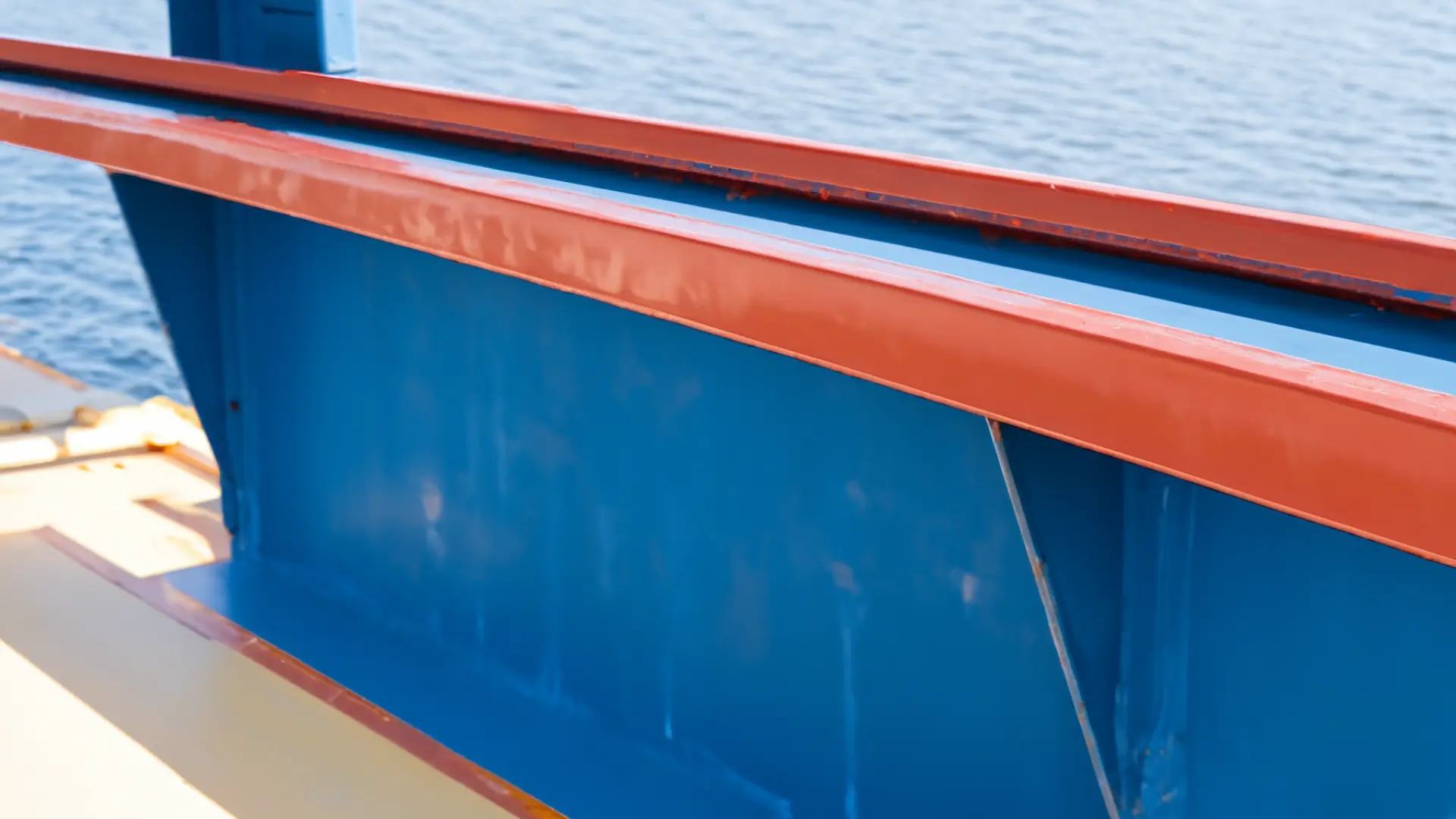
A Detailed Analysis of Ship Manufacturing Processes
The ability of colossal ships to successfully navigate vast oceans is the result of an intricate confluence of well-coordinated manufacturing processes. In the development of a maritime leviathan, every step is characterized by careful planning and meticulous execution. Here, we explore the foundational processes involved in ship manufacturing. We would pay particular attention to the importance of metal testing, especially tensile testing, in shaping manufacturing processes, regardless of ship production scale.
1. The Design Phase
Marine Architecture: Utilizing marine architects' expertise to conceptualize ship designs, ensuring aerodynamic, hydrodynamic, and structural sound.
3D Modeling: Implementing sophisticated software to visualize and modify designs.
Safety Protocols: Integrating global maritime standards and regulations to ensure safety and sustainability.
2. Material Selection
Metallurgical Analysis: Utilizing metallurgists to understand and select metals based on their physical and chemical properties.
Supply Chain Management: Establishing a robust supply chain to secure high-quality materials in a timely and cost-effective way.
Sustainability Considerations: Choosing materials and suppliers that align with environmental sustainability and corporate social responsibility.
3. Metal Testing
Tensile Testing: Testing metals to control tension until failure, providing data on strength and elasticity to predict how materials will behave under loading forces.
Microstructural Analysis: Utilizing microscopy to evaluate structural integrity and identify inherent vulnerabilities in materials.
Life Cycle Analysis: Predicting materials' longevity and degradation under a variety of operational conditions and environmental exposures.
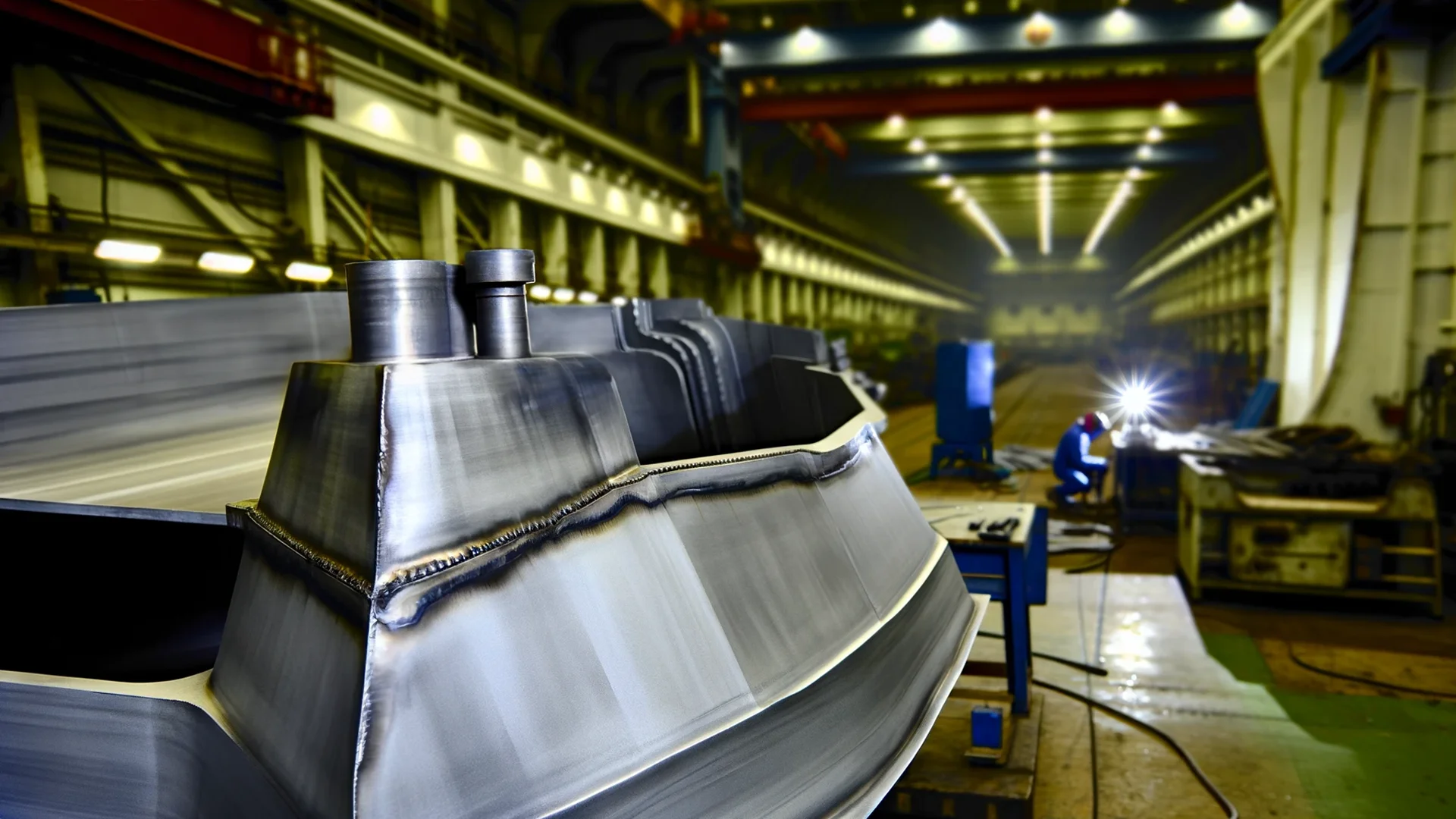
4. Frame Construction
Plating and Shaping: Deploying specialized machinery and techniques to mold and join metallic plates, ensuring alignment with design schematics.
Welding Techniques: Implementing advanced welding technologies to guarantee secure joints and eliminate weak points.
Structural Assessment: Conduct detailed examinations of the constructed frame to validate its stability and conformity to the requirements of the design.
5. Hull Formation and Testing
Anti-fouling Systems: Incorporating hull coatings and technologies to prevent biofouling, which reduces performance and increases fuel consumption.
Hull Stress Tests: Utilizing both numerical methods and physical testing to validate the hull's resilience to dynamic ocean forces.
Buoyancy Checks: Ensuring that the hull adheres to precise buoyancy and stability criteria, safeguarding against capsizing and ensuring optimal navigation.
6. Engine Installation and Propulsion Testing
Mechanical Integration: Ensure flawless incorporation of engines and propulsion mechanisms into the ship's structural framework.
Energy Efficiency Optimization: Implementing technologies and practices to optimize fuel consumption and minimize emissions.
Mechanical Safety Checks: Examine all moving parts to certify safety and reliability.
7. Fitting and Outfitting
Technological Installation: Integrating navigational, communication, and operational technology, ensuring functionality and redundancy in critical systems.
Interior Arrangement: Designing and constructing interior spaces, considering functionality and the needs of the crew.
Emergency Systems: Installing and validating emergency systems, ensuring rapid and effective response capabilities in crisis situations.
8. Sea Trials
Navigational Testing: Verifying ship navigational capabilities and ensuring adherence to predefined routes and operational parameters.
Operational Verification: Confirming that all installed systems function correctly and cohesively under real-world maritime conditions.
Performance Analysis: Collecting and analyzing data to assess the ship's performance, making any requisite adjustments prior to finalizing construction.
Ship manufacturing involves an integration of these highly specialized processes, resulting in vessels capable of navigating the unpredictable conditions of the vast seas. Human ingenuity, commitment, and careful attention to detail result in engineering masterpieces that traverse the wide expanses of the oceans, connecting continents, and facilitating trade worldwide.
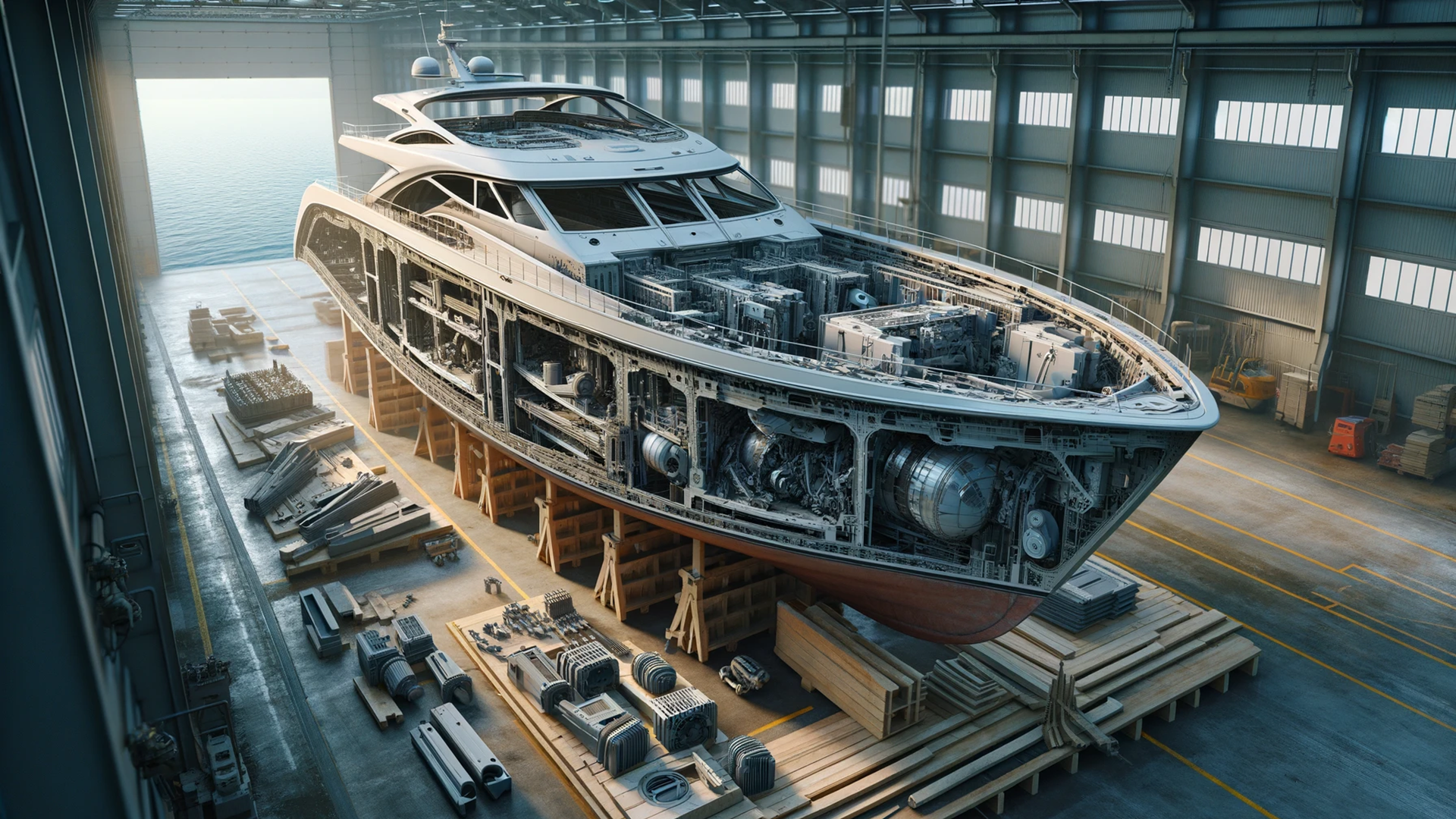
Selecting and Testing the Right Metals
As we understand the vital components that build our dependable sea giants, materials selection and testing play a crucial role. Remember, each metal gets a pass only after proving itself! So, how do shipbuilders decide which metals to use, and what tests, like tensile testing, ensure they're fit for the voyage?
Metal selection begins with understanding the destination and the tasks the ship will undertake. Different metals have their own special qualities that make them suitable for a variety of parts of a ship. A ship's hull and structure are often constructed from steel, which is renowned for its strength and durability. Meanwhile, other metals like aluminum, known for its lightweight and corrosion resistance, might find their place in parts of the ship where such characteristics are important.
Ensuring these metals can endure sea hardships without compromising ship safety and functionality is where testing plays a key role. Metals undergo rigorous tests to validate their strength, corrosion resistance, and durability under extreme conditions. One such test, as we briefly mentioned before, is tensile testing. It determines how much a metal can be stretched or pulled before it breaks. This isn't just about making sure the metal is strong, but also about ensuring it can handle the constant push and pull of the forces it will experience at sea.
Other testing methods, like impact testing, check how the metal reacts to sudden, forceful blows, simulating conditions such as sailing through waves during a storm. Corrosion testing is another vital checkpoint, especially considering the salty sea air and water the ship will be constantly exposed to. These tests together make sure that the chosen metal isn't just strong, but also capable of withstanding the test of time and the environment.
Then there's assembly - the meticulous process of putting these tested metals together to construct the ship. Different sections and components, each crafted from carefully selected and tested metals, are assembled. Welding, riveting, and bolting join these pieces together, creating a cohesive, secure, and sea-worthy vessel. All these steps, from selecting to testing, and finally, assembling, are guided by international standards and regulations, ensuring every ship that sets sail is not only built to last but also to safeguard its crew and cargo against the unpredictability of the ocean.
The Role of the Standards in Ship Manufacturing
During the process of shipbuilding, we reach a crucial point that ensures the quality, safety, and reliability of each vessel in compliance with international standards. These guidelines, established by organizations such as the International Organization for Standardization (ISO), the American Society for Testing and Materials (ASTM), and other regulatory organizations, form a robust system that ensures that shipbuilding manufacturing processes are accurate and reliable.
Navigating through the sea of shipbuilding while in compliance with these standards ensures that ships exhibit a level of safety and quality that is accepted and trusted around the world. Whether it's the selection of metals, manufacturing processes, or testing protocols, compliance with standards like ISO and ASTM provides a comprehensive method that is universally applicable and recognized.
ISO, with standards like ISO 9001, which relates to Quality Management Systems, and ISO 14001, focusing on Environmental Management, guides ship manufacturing towards maintaining high quality and ensuring environmentally responsible and sustainable processes. These standards establish criteria that require manufacturers to demonstrate their ability to consistently provide products that meet customer and regulatory requirements.
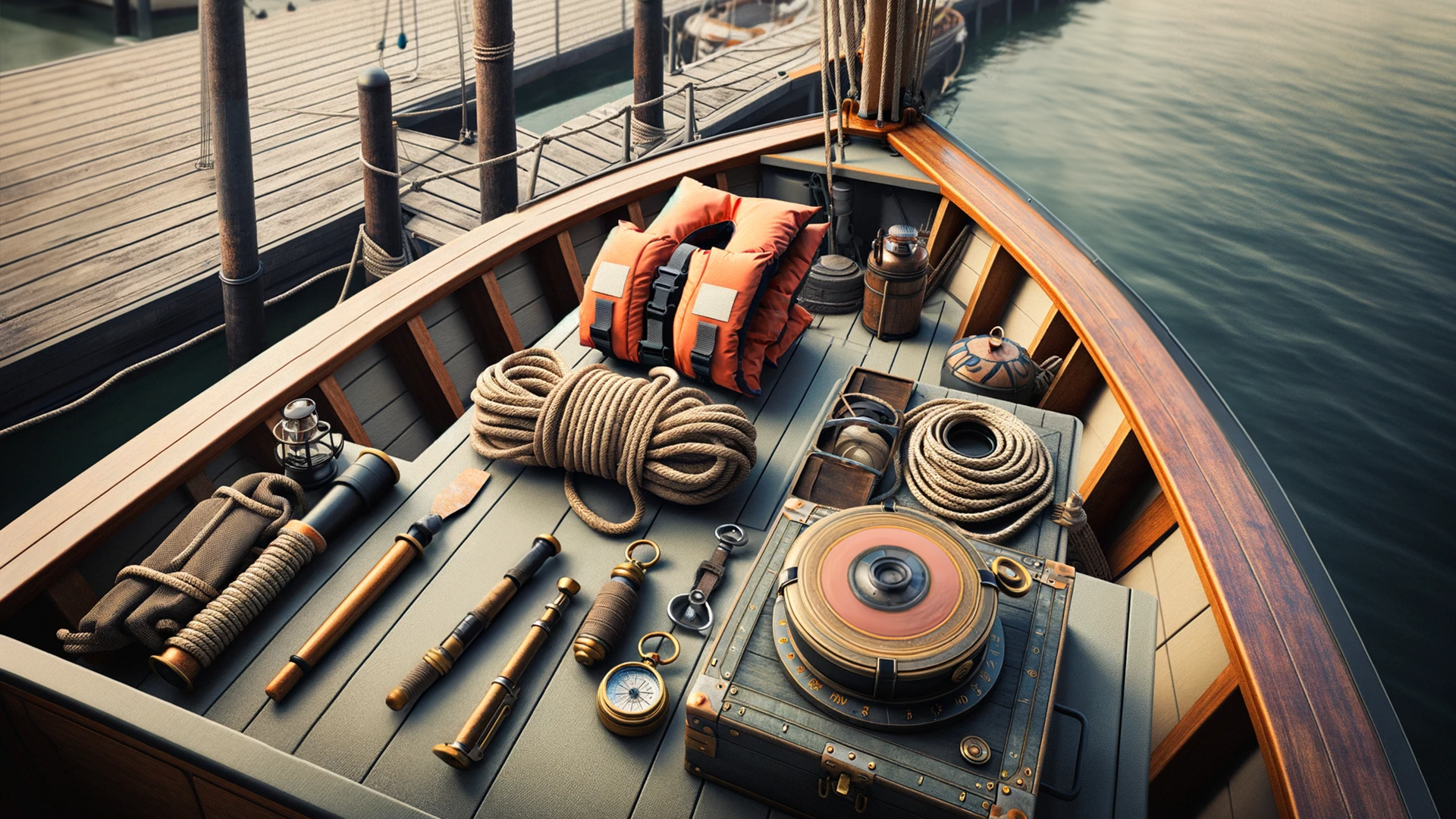
Similarly, ASTM standards, such as ASTM E8/E8M - which specifies tensile testing for metals - offer precise procedures to determine properties like yield strength, elongation, and tensile strength, ensuring the metals used in shipbuilding are rigorously tested and validated. The ASTM A370 standard is another vital benchmark that helps determine the mechanical properties of steel, stainless steel, and related alloy products, crucial in the shipbuilding industry.
These standards not only create a unified approach to manufacturing across global shipyards but also help maintain and elevate the safety, durability, and performance of the vessels produced. The strict compliance with these guidelines assures that every process, from the initial design stages to the final manufacturing and assembly, is conducted under a stringent quality management system.
The Fundamental Role of Tensile Testing in Shipbuilding
Navigating through the complex and detailed process of shipbuilding, tensile testing, which we already mentioned, plays one of the most significant roles. It helps to ensure the ship's strength and durability. There is no way manufacturers would use metal before it undergoes tensile testing. This mechanical test, which determines a material's ability to withstand loads in one direction without deformation, is vital in deciding the viability of materials, predominantly metals, in different applications throughout the ship. Nevertheless, where exactly is tensile testing most commonly utilized in shipbuilding, and why?
- Hull Construction: The hull, being the ship's primary structure, must demonstrate exemplary strength and resilience. Tensile testing helps ensure that the steel used in hull construction can withstand the high levels of stress and strain encountered during sea trips, ensuring it maintains structural integrity even in challenging conditions.
- Engine Parts: Engines are subject to intense heat and pressure, requiring materials that can endure these harsh conditions. Through tensile testing, materials like iron and steel are evaluated for their ability to handle these extreme conditions without losing their mechanical properties.
- Decking Materials: The deck, constantly exposed to the outdoors, requires materials that resist not only mechanical stresses but also environmental factors like corrosion from saltwater. Tensile testing helps in selecting materials that maintain their structural properties in the face of persistent external pressures.
- Mast and Rigging Components: For ships with masts and rigging, the materials used must be able to support significant loads, especially in windy conditions. Testing the tensile strength of these components allows them to withstand harshness while in the seas.
- Anchor Chains: Anchor chains play an integral role in ensuring the ship remains stationary when docked, which is why the materials used for anchor chains must be able to withstand the constant pulling forces exerted by the ship, particularly during rough weather conditions.
Tensile testing is a valuable tool, yet its accuracy and reliability depend heavily on tensile sample preparation. An incorrectly prepared sample can lead to inaccurate test results, making them unreliable and potentially compromising the integrity of the entire manufacturing process. In the following section, we will examine the importance of tensile sample preparation in shipbuilding, explaining how this process is fundamental to ensuring the durability of our ships.
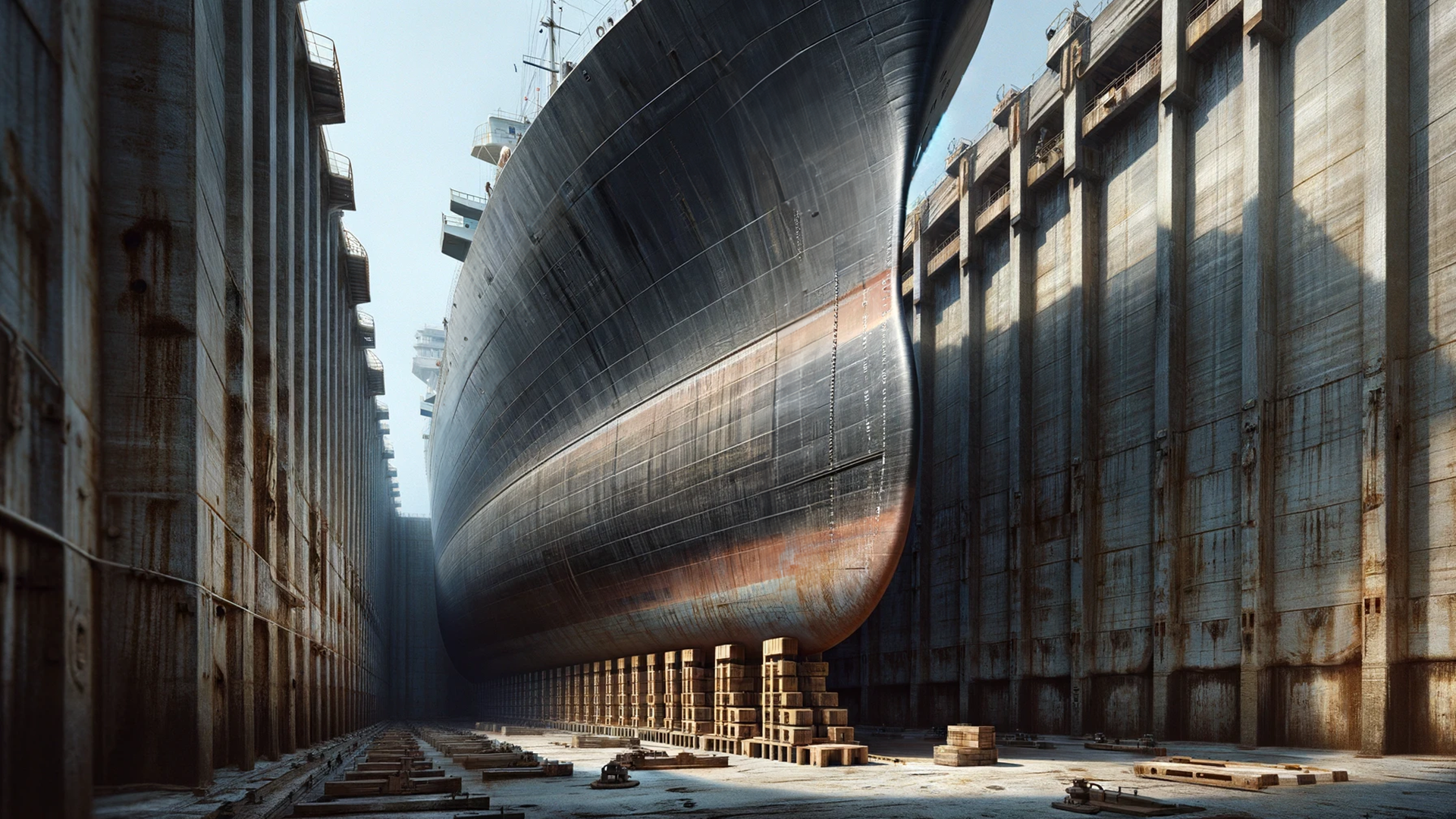
Tensile Specimen Preparation in Shipbuilding
Among the many stages involved in material testing within the shipbuilding industry, the preparation of tensile specimens is particularly important as a critical step, which connects theory and practice. Rather than simply understanding a metal's intrinsic properties, it is important to ensure that every test conducted to determine these properties is accurate, reliable, and replicable across a number of scenarios and applications. To ensure that the material's properties meet the stringent standards set by regulatory organizations, accurate tensile specimen preparation becomes essential.
A specimen, appearing to be an insignificant piece of metal, serves as a representative of the large sheets, intricate components, and gigantic ships that sail our oceans. This preparation requires a keen eye, meticulous precision, and, most importantly, reliable equipment. Here is where TensileMill's machines can prove useful.
Offering solutions to both flat and round tensile sample preparation, such machines combine speed and precision. With an average monthly sample capacity of over 10,000 specimens, serving 34 industries, and testing 39,879 different products, flat and round tensile testing machines are proving to be a source of the highest quality results.
TensileMill CNC MINI: Compact and Powerful
Despite its smaller footprint, the TensileMill CNC MINI is more than capable when it comes to delivering exemplary flat tensile sample preparation. MINI does not simply comply with tensile specimen standards but takes them to the next level so that the specimen test results are always accurate and consistent regardless of the material being tested.

Moreover, while compact, the MINI does not compromise on size. It accommodates medium to high volumes of tensile specimen preparation, even for materials with hardness values up to 60HRC. With its advanced software, ensuring accurate and repeatable milling results becomes a matter of pressing two to three buttons, distilling complex procedures into straightforward, user-friendly operations.
TensileTurn CNC: Making Round Specimens Easy with an Industrial Upgrade
Addressing the essential need for effective round tensile sample preparation, TensileTurn CNC machines offer unprecedented ease and precision. Especially, the TensileTurn CNC - Industrial Upgrade takes a significant step forward, capable of handling larger blank sizes, tougher materials, and irregular shapes.

With features like automatic center drilling and a robust granite frame ensuring stability and shock absorption, the Industrial Upgrade ensures maximum sample preparation accuracy. Also, it guarantees a longer system lifespan, offering a reliable ally in tensile specimen preparation. Beyond tensile preparation, it also accommodates a full range of CNC machining capabilities in one comprehensive package.
Advancing Maritime Engineering through Sample Preparation
Integration of TensileMill and TensileTurn CNC machinery demonstrates simplicity in tensile sample preparation. The rigid adherence to careful preparation provides evidence of the durability of the metals used throughout the vessel.
Material testing in shipbuilding requires anchoring practices in the reliability derived from accurately prepared tensile samples. This principle is transformed from concept to operational reality with the use of TensileMill and TensileTurn CNC machines.
The systematic preparation of tensile specimens coincides with an unwavering commitment to quality, safety, and reliability, which is extended from the micro-level tensile sample to the macro-level, magnificent maritime vessels. As a result, rigorous material testing helps to ensure the safety, precision, and high quality of each maritime trip.
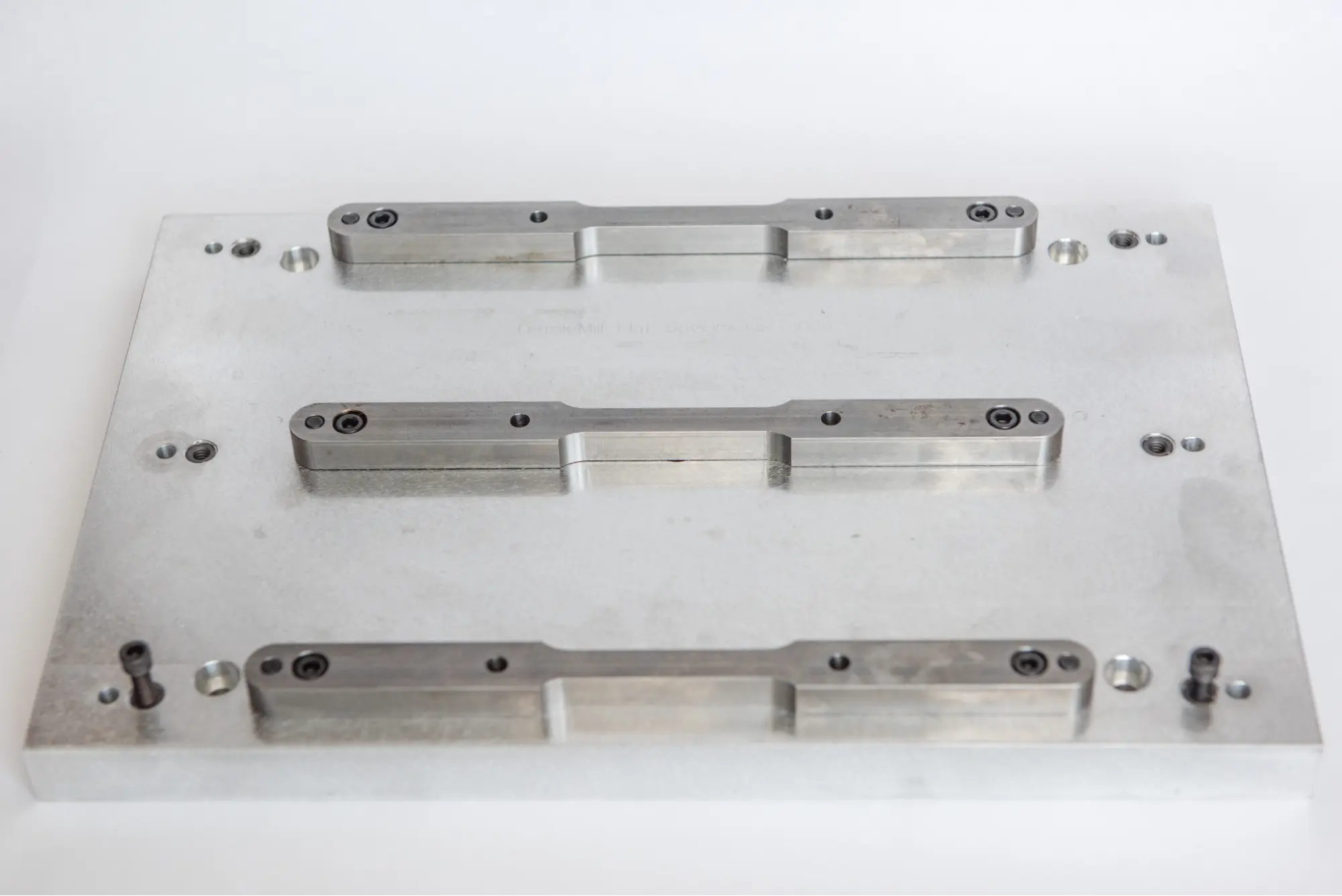
Crafting Unbreakable Giants with Precise Material Testing
When navigating through the precise waters of shipbuilding, it is clear that the structural strength of every sea giant depends on rigorous processes of material selection and testing. Having its origins in safety, durability, and precision, this industry is composed of engineering expertise and strict compliance with international standards, all of which are intended to ensure the complete integrity of the ships that sail the oceans.
From the selection of metals to the creation of ship components, material testing, such as tensile testing, serves as an essential element, which ensures that every part of the ship is robust enough to withstand the harsh marine environment and operational stresses. Steel and aluminum's strength and resilience are not simply assumed but rather are demonstrated through rigorous testing processes and standards.
Tensile testing, a crucial component of this evaluation, ensures that materials can withstand significant strains and stresses experienced during maritime travel. Using machines such as the TensileMill CNC MINI and TensileTurn CNC, material testing can become more than just a procedure, but a strong commitment to quality and safety.
In every aspect of the shipbuilding process, strict standards must be maintained, including the preparation of tensile specimens. Providing a solid foundation for metallurgical testing, these machines provide practical application in material testing.
If you require reliable and precise tensile testing and sample preparation equipment, please do not hesitate to contact us for a quote or to contact us directly. We are always ready to assist you with material testing!