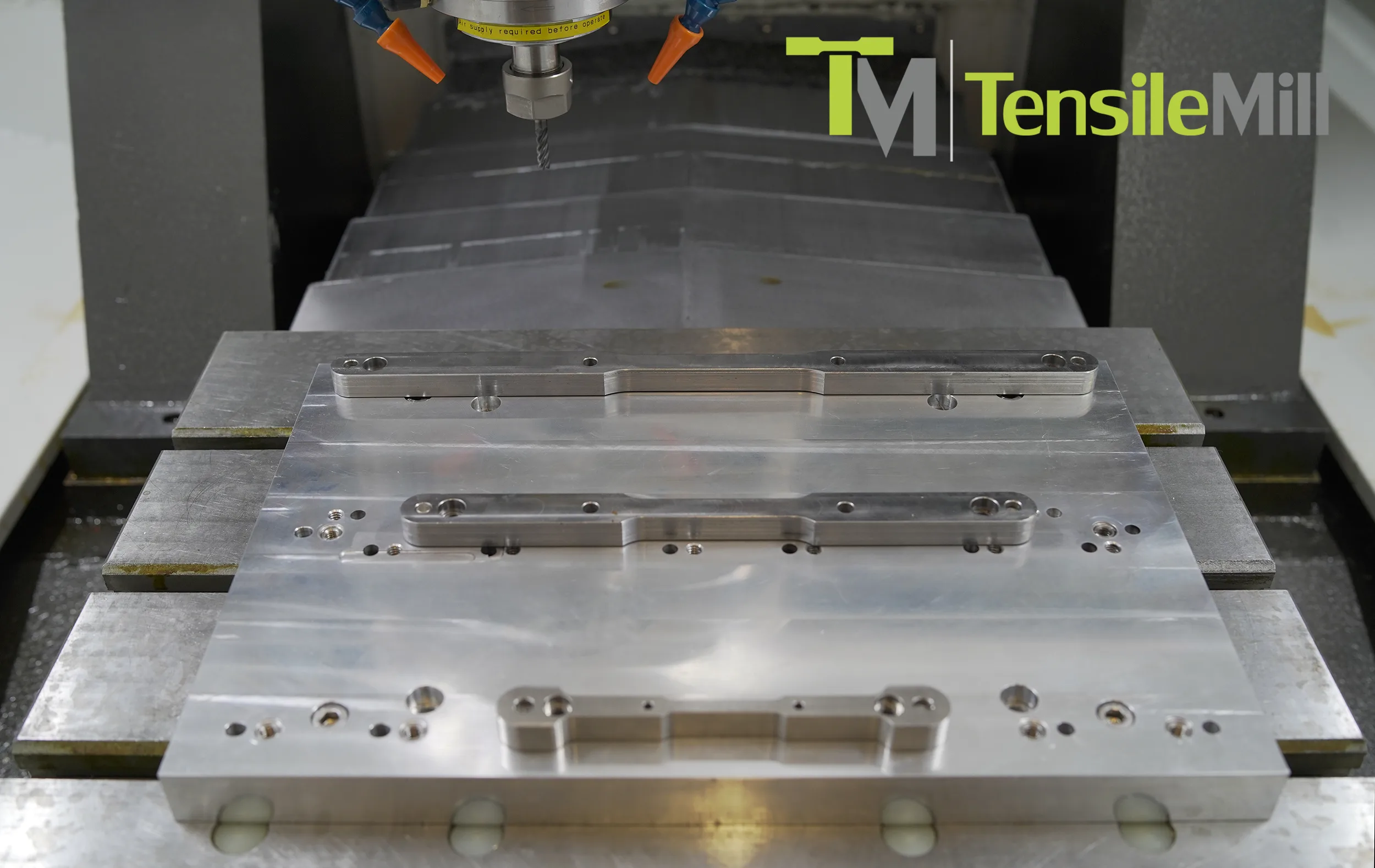
Tensile testing accuracy starts long before the universal testing machine ever applies a load – it begins with the test specimen itself. Even the most advanced test frame cannot compensate for a poorly prepared sample. If a tensile specimen’s geometry, surface finish, or dimensions are out of specification, the resulting data will be unreliable.
In fact, the accuracy of the tensile specimen is just as important as the quality of the testing machine. A poorly prepared specimen will conduct poor results, even on the most precise equipment. Cuts or flaws in the specimen, such as jagged edges or nicks, act as stress concentrators that can cause premature failure and skew the results.
This article is going to clarify the reasons why the CNC milling system is the starting point for tensile testing accuracy, rather than the test machine. We will look into the function of CNC machining in specimen preparation, compare it with other cutting methods, and highlight the significance of complying with international standards. Furthermore, we will present practical guidance on how to select the most appropriate gear for obtaining consistently accurate results.
Why the Tensile Testing Process Begins with the Specimen
In any tensile testing procedure, the specimen is not simply a piece of material; it acts as the foundation for the entire test. Although a universal testing machine may be extremely advanced, precise, or calibrated, it is only capable of generating accurate outcomes if the test specimen is properly prepared. However, even the most dependable test machine is incapable of providing valid information without the presence of dimensional accuracy, proper surface condition, and standard compliance.
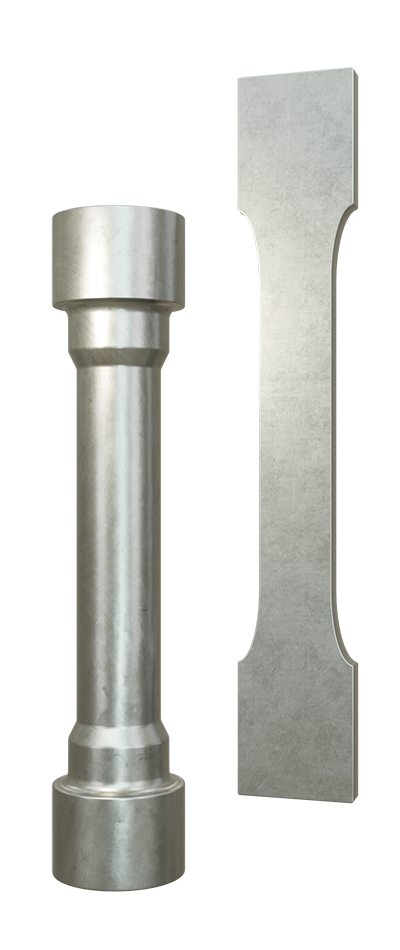
A tensile specimen's geometry plays a role in the distribution of stress during testing. ASTM E8, ISO 6892, and DIN 50125 are some of the standards that set precise parameters for gauge length, width, thickness, and fillet radii. These parameters are thoughtfully created to prevent gauge section failure under pure tension. The test may introduce unintended variables, such as stress concentrations or bending moments, that distort the mechanical performance measured if any of these dimensions fall outside the permitted tolerances.
A slight asymmetry in the shoulder areas or an uneven surface finish, for instance, can cause the stress distribution to deviate from the intended gauge section. A stress riser, known as a small burr, scratch, or notch on the edge, can result in premature fracture. The failure in these cases is not representative of the material's true tensile behavior but rather the imperfections that were introduced during specimen preparation. This process leads to invalid fracture modes, incorrect elongation values, or artificially reduced tensile strength.
CNC and Other Methods: Milling vs. Waterjet, Laser, or Manual Cutting
The degree of precision and uniformity of test results is heavily affected by the cutting and shaping method used to prepare tensile specimens. Manual machining, waterjet cutting, laser profiling, punching, and automated CNC systems are among the many methods that are often used in laboratories and production facilities. Now, we will look at each of those methods in greater detail:
Manual Machining and Grinding
Traditional preparation, which involves the use of lathes, milling machines, or surface grinders, is heavily influenced by the operator's proficiency. Precision by hand requires skill for each step, from workpiece alignment to depth control and finishing. This introduces variations: surface defects, misalignments, and inconsistent dimensions are frequent when manual operations are performed. Additionally, manual preparation is inefficient and time-consuming for high-volume workflows. The process is not repeatable, which is necessary for strict compliance with international standards or statistically valid testing, although skilled machinists may achieve acceptable results.
Waterjet Cutting
Abrasive waterjet (AWJ) systems offer a non-thermal cutting process that prevents heat-affected zones, thereby preserving the original material properties. Nevertheless, waterjet cutting can lead to non-uniform profiles, rough surfaces, and tapered edges. Waterjet-cut tensile specimens might show higher elongation and a lower ultimate tensile strength as a result of microstructural inconsistencies introduced at the edges. This frequently requires post-processing, such as surface grinding or polishing, to meet the surface quality and dimensional specifications defined by standards such as ISO 6892 or ASTM E8.
Laser Cutting
Laser cutting is a method that is commonly used for thin sheet specimens due to its speed and precision. However, the laser profiling process generates a heat-affected zone (HAZ) along the cut edges as a result of the high-intensity beam. This HAZ has a chance to induce microstructural changes, residual stress, or localized hardening, particularly in metals. These unintended modifications have the potential to cause premature failure during tensile testing or distort the stress-strain behavior. As a consequence, laser-cut specimens often require secondary edge treatment to mitigate thermal damage and remove dross, which increases the preparation process's complexity and time.
Punching and Stamping
Punching or stamping may be applied for the purpose of producing flat specimens at a rapid rate. Although this method is effective for volume, it introduces shear deformation at the cut edges, which can lead to burrs, cold-worked zones, or uneven radii. These edge defects pose a risk to invalidate the test by acting as stress concentrators, causing distorted test results. Furthermore, the flexibility of stamping is restricted by the need for specialized tooling (dies) for each specimen type and size. On the other hand, CNC systems can be reprogrammed on demand to prepare a variety of specimen types without the need for new hardware.
CNC Specimen Preparation
CNC tensile specimen preparation machines are intended to address the weaknesses of thermal and manual methods. These systems apply computer-controlled movements to precision-shape specimens at the micron level, resulting in gauge sections, fillets, and transitions that comply with global standards. CNC machining guarantees consistent geometry and surface finish for all specimens, minimizes human error, and reduces variability.
CNC systems produce specimens with smooth, burr-free edges, removing the need for additional polishing in most instances because of their optimized tool paths, feed rates, and cutting parameters. In contrast to thermal methods, CNC milling and turning do not affect the mechanical properties or internal structure of the material, thus preserving the integrity of the test material. Additionally, CNC machines have the capacity to prepare many specimens in a single session, which increases throughput and facilitates large-scale testing operations.
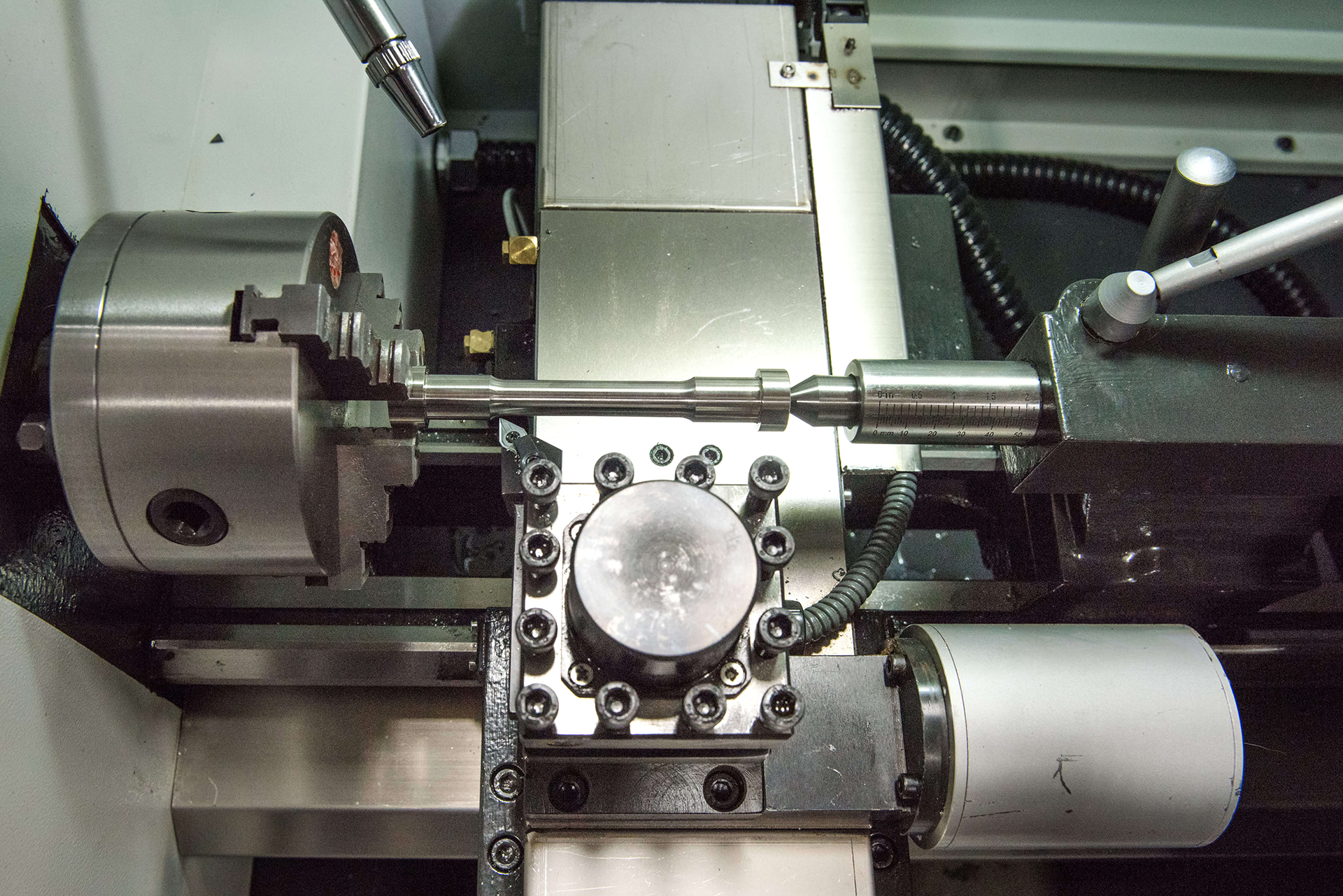
Selecting the Optimal CNC Sample Preparation Machine
The selection of the appropriate CNC specimen preparation machine matters greatly for the consistent, efficient, and accurate performance of tensile testing. The selection should be based on the specific requirements of your laboratory, the materials being tested, and the type of specimens that are needed. The following factors should be taken into account when assessing your alternatives:
Match to Your Specimen Types
Before anything else, determine whether you require flat, round, sub-size, or custom specimens. The CNC system must be capable of managing the transitions and geometries necessary for each type. Certain systems feature pre-configured templates, which facilitate a quick transition between shapes that comply with industry standards.
Material Capacity and Size Handling
Consider the machine's compatibility with the materials that you frequently test. This covers its capacity to cut a variety of hardness levels, lengths, and thicknesses. The machine should be constructed with an adequate amount of torque, rigidity, and fixturing capacity if your laboratory processes tougher alloys or oversized blanks.
Control System and Usability
Operational efficiency is greatly affected by the interface of the machine. Advanced industrial controls may be preferred by laboratories with skilled machinists, while simplified, touchscreen-based interfaces with preloaded profiles are advantageous for those who prioritize speed and user-friendliness.
Precision vs. Throughput
Systems that are optimized for speed, with minimal setup times and efficient toolpaths, should be sought in high-volume environments. In laboratories where precision is the primary concern, machines with ultra-fine resolution, stable cutting platforms, and controlled feed rates that generate consistent dimensional accuracy should be prioritized.
Automation Features and Add-Ons
Few of the models of modern CNC systems frequently come with optional upgrades that boost productivity and consistency. These might include notching modules for Charpy or Izod samples, automatic clamping systems, or integrated cooling for thermal control. Operator dependency can be mitigated, and turnaround times may improve through the implementation of an appropriate feature set.
Assistance and Instruction
Supplier support that is dependable is equally critical as the machine itself. Your team can take advantage of the machine to its fullest potential and sustain its performance for an extended period of time with the assistance of appropriate training.
Compliance with Specimen and Equipment Standards
Lastly, guarantee that the CNC system supports complete compliance in two key areas:
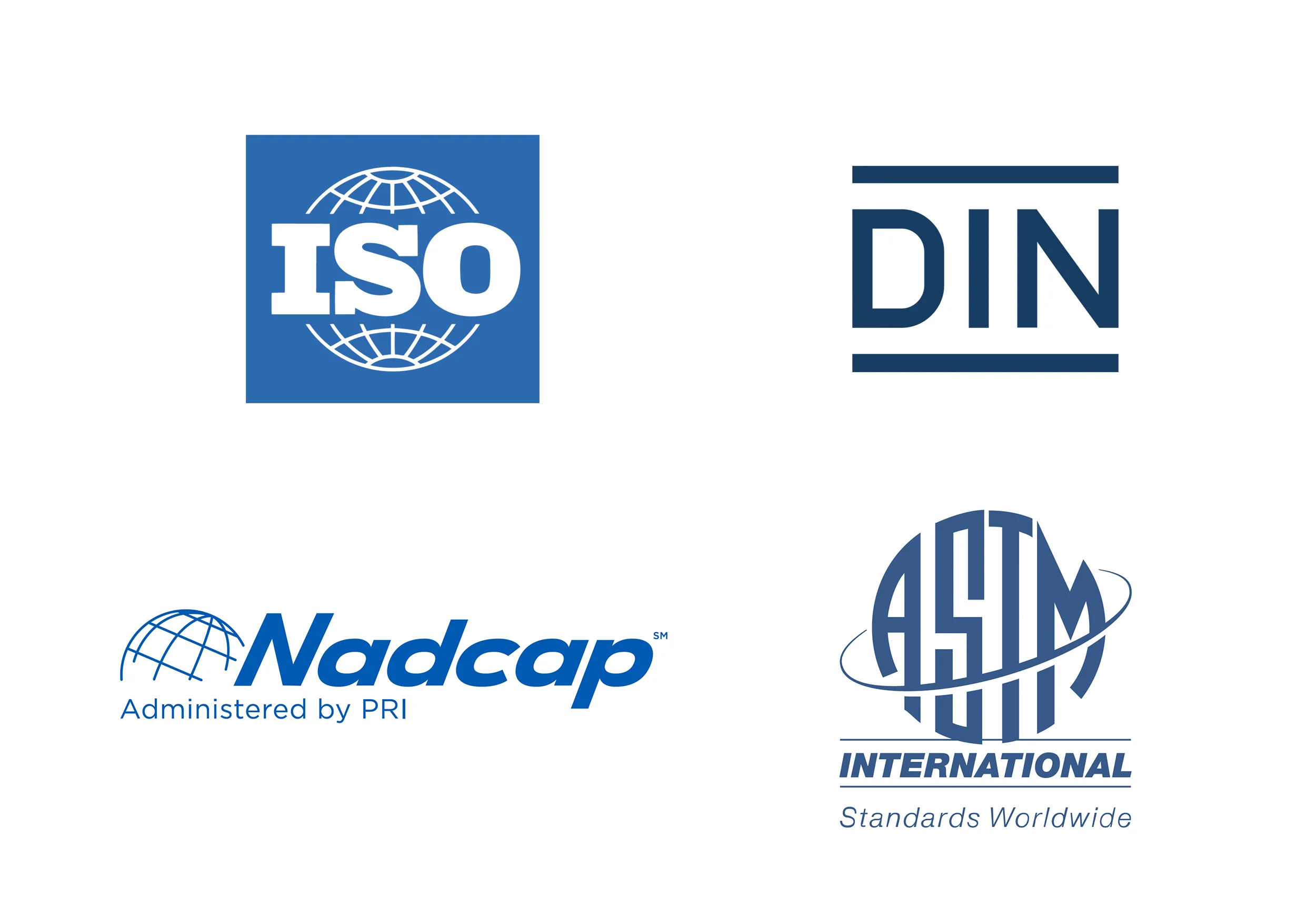
- Specimen compliance: The machine must generate samples that satisfy the dimensional and surface specifications of standards such as DIN 50125, ISO 6892, or ASTM E8.
- Equipment compliance: The system must be compatible with recognized calibration and verification protocols, such as ISO/IEC 17025:2017 or ASTM E1012, to guarantee accurate machine alignment and precision.
You can choose a CNC preparation system that not only meets your current testing requirements but additionally supports long-term reliability and standardization across all specimen batches by focusing on these core considerations.
Do You Require Accredited Certification for Your Testing Equipment?
Do you require standards certification for your laboratory or equipment? At TensileMill CNC, we offer comprehensive certification support services for machines purchased from us or third-party devices, in addition to precision testing and specimen preparation equipment. Our product line covers tensile testing machines, CNC specimen preparation systems, extensometers, and force measurement equipment.
We simplify the calibration and certification processes for standards such as ASTM E4 (force verification), ASTM E1012 (alignment calibration), ASTM E83 and ISO 9513 (extensometer calibration), and ISO 7500-1 by using our network of ISO/IEC 17025:2017-accredited partners. We also provide full traceability and regulatory alignment with NADCAP and ANSI/NCSL Z540-1-1994, which allows you to achieve the highest levels of performance required in accredited and regulated testing environments.
TensileMill CNC's certification facilitation services offer a documented, smooth path to compliance, whether you require certification for new equipment, maintenance of an existing system, or preparation for an industry audit. Preventative maintenance, operator training, and reliable recertification are frequently included in our packages at no extra cost, guaranteeing operational excellence and long-term reliability. Please reach out to us today to get a calibration quote or to learn more about how we can assist in making sure that your laboratory is fully industry-ready and compliant.
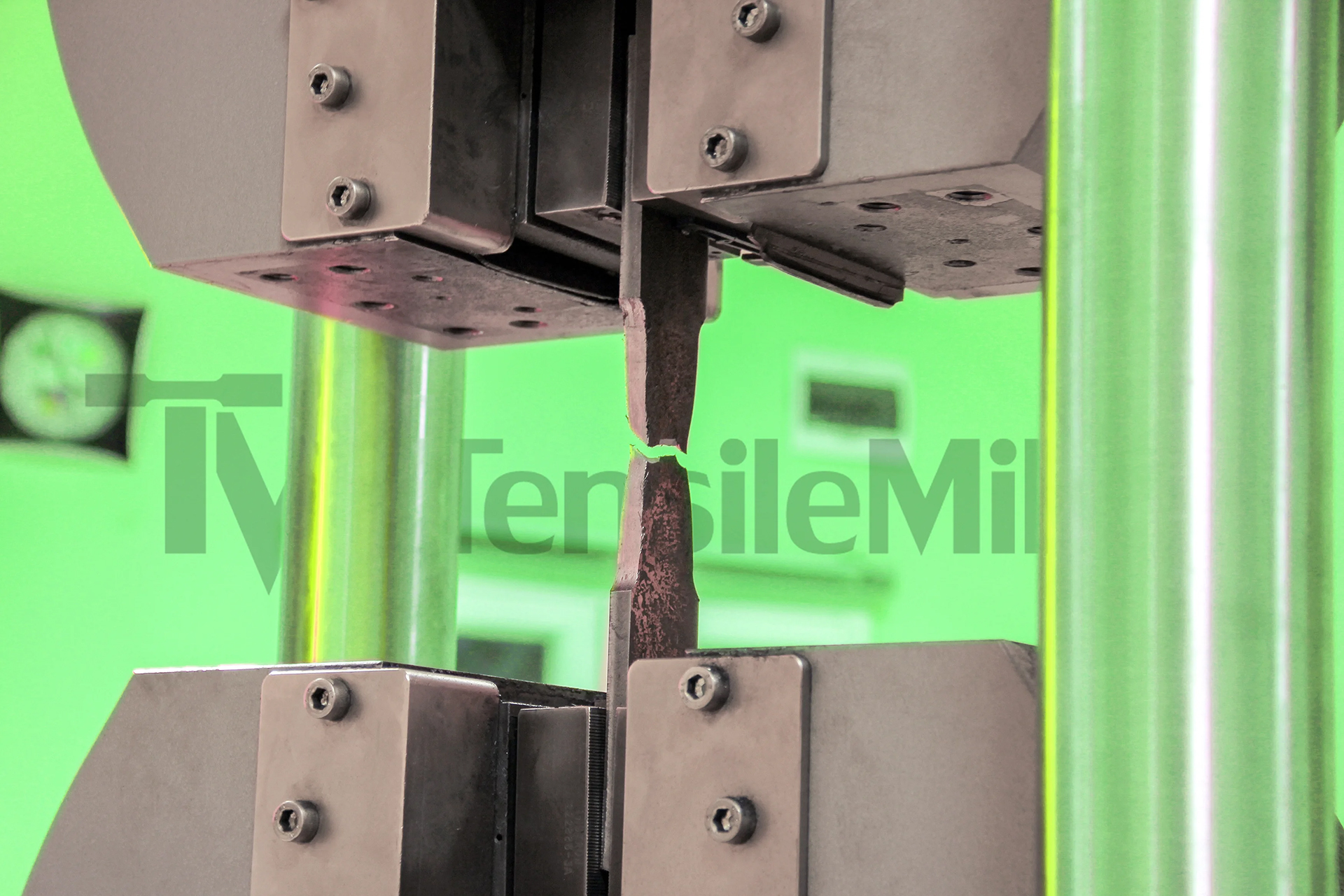
Precision Starts at the Source – Not at the Test Frame
The reliability of tensile testing is based on the specimen under examination. The process of obtaining accurate, repeatable, and standards-compliant tensile test results starts at the CNC milling system responsible for preparing the specimen. The validity of each measurement, including tensile strength and elongation, is directly affected by the geometry, surface quality, and dimensional accuracy of the sample.
CNC specimen preparation machines provide exceptional precision, repeatability, and surface finish, in contrast to manual machining, laser, and waterjet cutting. Their consistent production of specimens that comply with global guidelines such as ASTM E8, ISO 6892, and DIN 50125 renders them the preferred option for research institutions, manufacturers, and testing laboratories.
Selecting the right CNC system necessitates a comprehensive assessment of its compatibility with required standards, material handling, automation capabilities, and calibration support, in addition to its machine capabilities. Equally critical is guaranteeing complete adherence to both equipment certifications and specimen preparation standards, such as ISO/IEC 17025:2017 and NADCAP requirements.
We offer accredited certification services for tensile testing machines, extensometers, and related equipment in addition to state-of-the-art specimen preparation systems at TensileMill CNC. This guarantees that your laboratory is fully equipped to meet industry requirements with precision, assurance, and regulatory compliance.
If you have any inquiries or would like to learn more about our company or the certification services we offer, please feel free to request an online quote or contact us directly. Our team is available to support your needs at any stage.