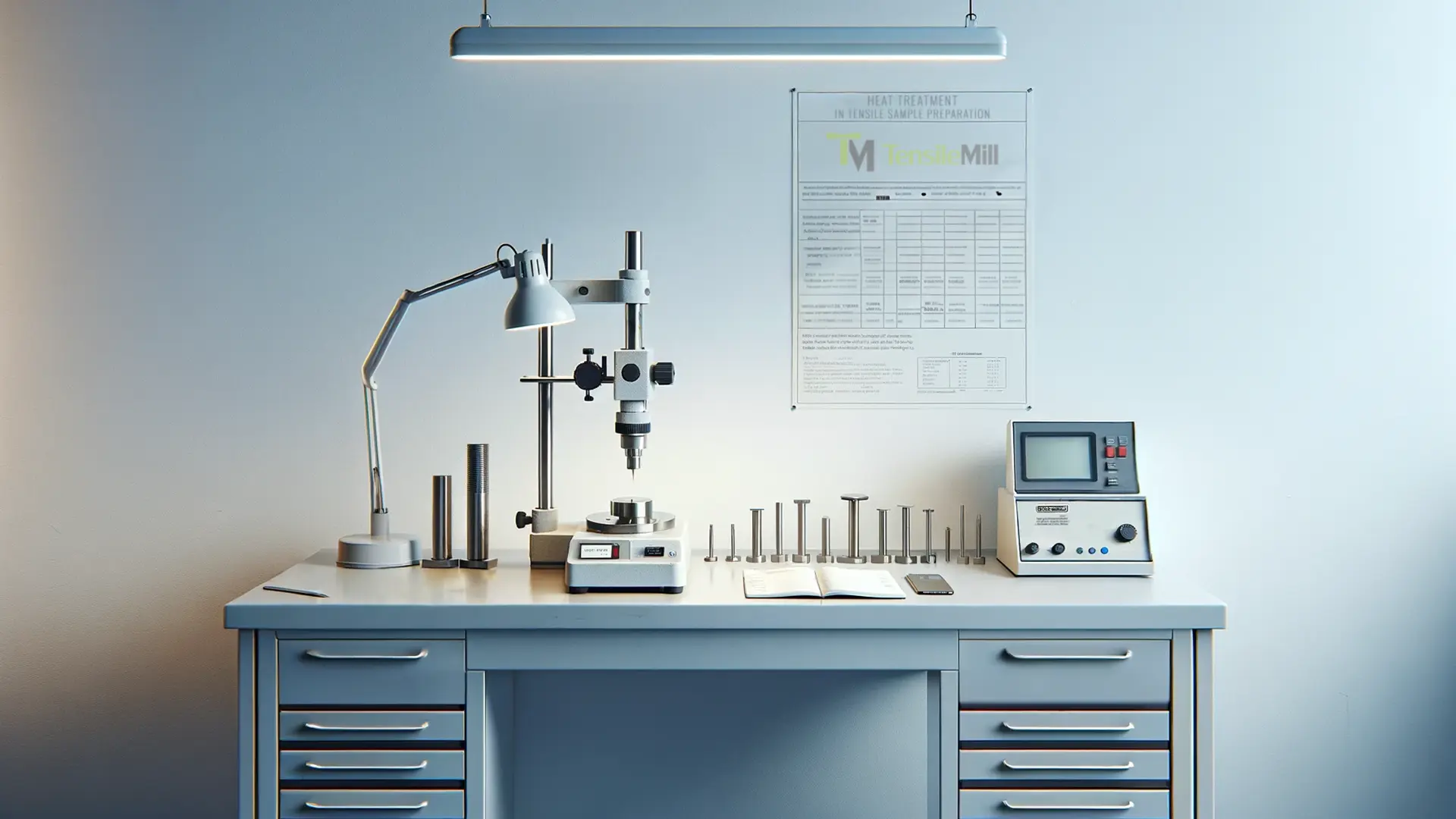
Heat treatment in tensile sample preparation is a process that aims to replicate the material properties of metals subjected to use in real-world applications. The objective here is to mimic the conditions and characteristics the metal would exhibit after heat treatment in industrial settings. This approach helps to ensure that tensile testing reflects the accurate behavior of materials as they perform under operational conditions and provides vital insights into their durability, strength, and suitability for specific uses.
Heat treatment is of utmost importance in tensile testing. It plays a key role in assessing materials' mechanical integrity and performance under uniaxial tensile stress. Moreover, it helps determine vital properties such as yield strength, ultimate tensile strength, and ductility. Heat treatment is strongly influential as it directly influences these properties by changing the material's microstructure. For instance, thermal treatment may enhance metal parts' tensile strength, making them more suitable for high-stress applications.
In this article, we will discuss the relationship between heat treatment and tensile sample preparation, along with the process of tensile testing for assessing the mechanical properties of different materials. By exploring how thermal treatment modifies material characteristics and the implications for tensile testing, we aim to provide insights into optimizing material performance for many different uses.
Heat Treatment in Material Testing
Heat treatment involves processes of heating and cooling metals in a controlled manner to alter their physical and sometimes chemical properties. This process is not about shaping the material but optimizing its performance characteristics to suit specific applications. Heat treatment can significantly impact metal durability, strength, and functionality
Why Use Heat Treatment?
The primary purpose of heat treatment is to make materials more useful, efficient, and adaptable to different environments. For instance, it can increase a metal's hardness to withstand more wear and tear or improve its ductility for better shaping and molding capabilities. Heat treatment relieves stresses in the material, making it more stable for precision applications.
Material Types Used in Heat Treatment
The heat treatment process is used for a range of metals and alloys, including steel, aluminum, copper, and nickel alloys. Depending on how the material responds to heating processes, there is a wide variety of applications that can be made. The following are some examples of materials:
- Steel: One of the most heat-treated materials, steel can undergo hardening, tempering, and annealing. Post-treatment is used in the manufacturing of construction beams, automotive parts, and cutting tools, owing to its enhanced strength and durability.
- Aluminum: Aluminum alloys are often treated to improve corrosion resistance and strength. This makes them ideal for aircraft structures and automotive components. Aluminum heat treatment processes include annealing, solution heat treating, and aging. These processes are aimed at achieving desired strength levels without compromising the material's lightweight properties.
- Copper: Heat treatment enhances copper's electrical conductivity, making it perfect for electrical wiring and components. The process can adjust copper alloy hardness and conductivity to meet specific electrical application needs.
- Nickel Alloys: These alloys don't experience a ferrite transformation but harden through precipitation, often referred to as "age hardening." Nickel alloys are renowned for their strength and corrosion resistance, making them suitable for high-temperature and high-stress applications in industries like aerospace and chemical processing.
Common Heat Treatment Processes
These are the most common heat treatment processes used in material testing:
- Annealing: This process softens the metal, enhancing its ductility and reducing hardness. This makes metal easier to machine, weld, or deform during manufacturing processes. Annealing relieves internal stresses in the material, leading to uniformity.
- Quenching: Aimed primarily at steel, quenching involves the rapid cooling of the material, typically in water or oil. This sudden cooling transforms the metal's structure, significantly increasing its hardness and strength. The process is crucial for manufacturing components with high wear resistance.
- Tempering: Following quenching, steel often becomes too brittle for practical use. Tempering is the process that mitigates this brittleness by reheating the quenched steel to a temperature below its critical point and then cooling it again at a controlled rate. This process maintains hardness obtained through quenching while improving toughness and ductility. Tempered steel finds applications in manufacturing tools, springs, and blades, where both hardness and resilience are required.
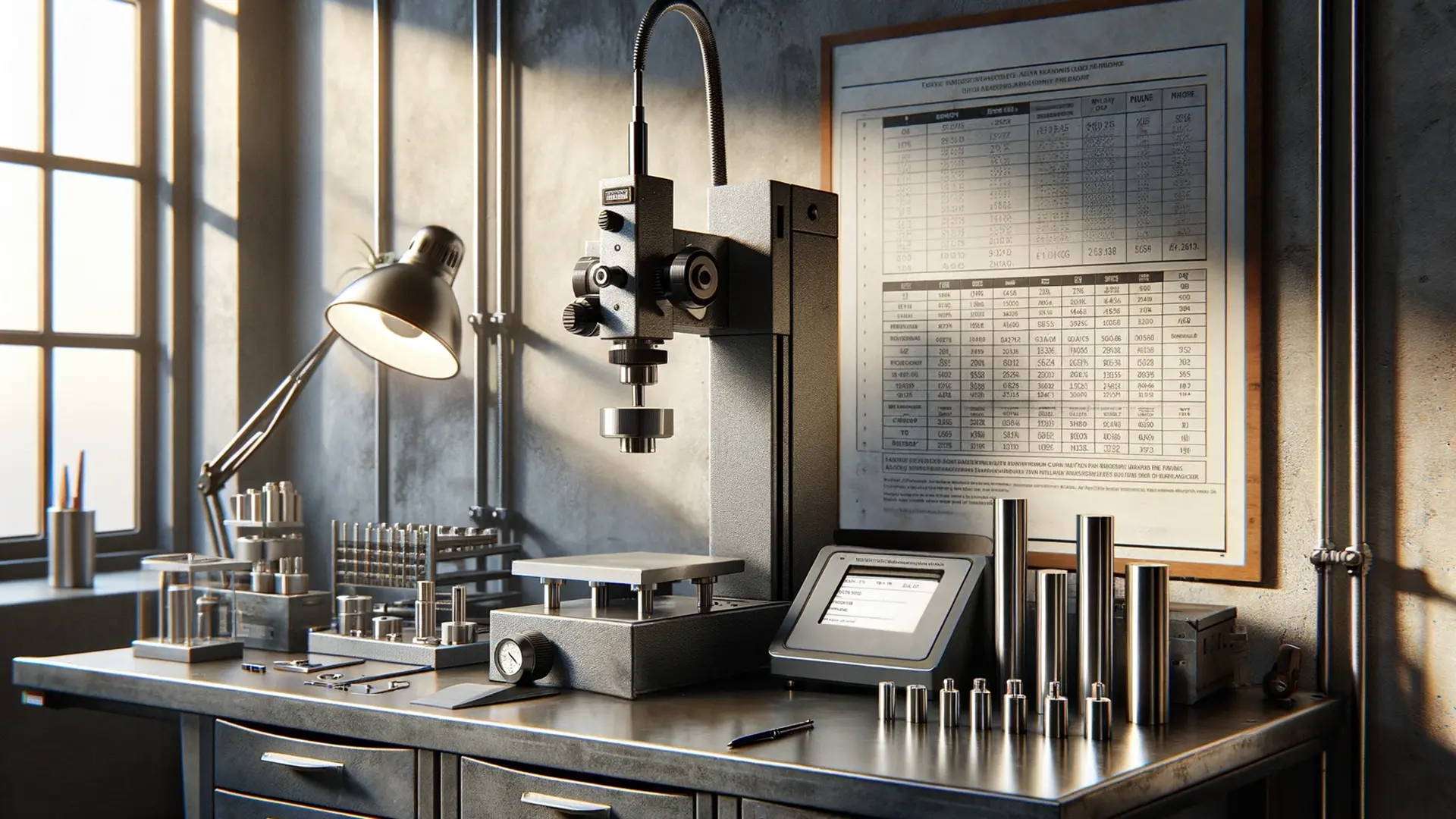
Understanding Heat Treatment in Tensile Sample Preparation
Heat treatment of tensile samples is used to replicate the conditions under which materials are manufactured and used. During material evaluation, tensile testing measures the force required to stretch a material to its breaking point. A test of this type provides critical information about the material's strength and flexibility, indicating its suitability for a particular application. Therefore, heat-treated tensile samples offer insight into how the material will behave under actual service conditions, including its capacity to sustain loads, resist deformation, and maintain integrity.
Researchers and engineers can also pinpoint the optimal thermal treatment for enhancing material properties by heating the material before tensile testing. Using this methodical approach, materials can be designed to exhibit desired characteristics, enhancing their reliability and performance in the field. Tensile testing of heat-treated samples guides material selection, design decisions, and quality control processes in every industry.
The use of tensile samples in the heat treatment processes acts as a bridge between theoretical knowledge and practical application. Material engineering requires meticulous attention to detail, making sure that the materials used are not just fit for purpose but also exceed expectations in their application environments.
The Process of Heat Treating Tensile Samples
The process of heat-treating tensile samples is important in preparing materials for mechanical testing. The following is a brief overview:
- Material Selection and Preparation: The first step involves selecting the appropriate material and cutting it into specimens sized according to testing standards. This precise cutting guarantees material integrity before heat treatment.
- Initial Cleaning and Inspection: Samples are cleaned to remove surface contaminants and inspected for defects. Any pre-existing anomalies could affect the heat treatment and tensile test.
- Heat Treatment Process: Depending on the desired material properties, samples undergo one or multiple heating processes. The specifics of each process - temperature, duration, and cooling method - are rigorously controlled to achieve the target microstructure and mechanical properties.
- Post-Treatment Cleaning and Inspection: After heat treatment, samples are cleaned again to remove any oxidation or residue from the surface. A detailed inspection follows to ensure the heat treatment has achieved the desired effect without introducing defects.
- Final Machining and Polishing: Some samples may require final machining to achieve precise dimensions for tensile testing. Polishing provides a smooth surface, minimizing the risk of introducing stress concentrators that could influence tensile test results.
- Tensile Testing: The heat-treated tensile samples are then subjected to tensile testing commonly using Universal Testing Machines (UTMs), where they're stretched until failure. The test measures properties such as yield strength, ultimate tensile strength, and elongation, providing insight into material performance.
Innovations Changing Heat Treatment in Material Engineering
The continuous quest for innovation has led to significant advancements in heat treatment processes. Controlled atmosphere and laser heat treatments have established themselves as frontrunners, revolutionizing material properties improvement. The precision offered by controlled atmospheres allows for uniform treatment of metals. Simultaneously, laser heat treatment introduces a level of precision and efficiency previously unattainable, enabling localized hardening without compromising the integrity of complex components.
The push towards sustainability has also seen the rise of electrically heated furnaces, marked by their high operational efficiency and reduced environmental impact. These furnaces, equipped with automated temperature control, represent a leap forward in eco-friendly manufacturing, aligning with the global shift towards greener technologies.
This technological evolution aligns closely with the automotive industry's needs, especially in integrating heat treatment processes into production lines. As the industry moves towards electric vehicles, the demand for innovative thermal treatment solutions that cater to the unique requirements of sustainable metals used in EV production is growing. This is indicative of the broader industry trend towards automation and efficiency, driven by the increasing adoption of electric vehicles. In addition, it shows the need for environmentally friendly manufacturing practices to be implemented in the future.
The Importance of Tensile Sample Preparation
The careful preparation of tensile specimens, whether round or flat, is the cornerstone of any tensile test. This directly impacts tensile testing reliability and accuracy. Precise specimen preparation guarantees that physical dimensions and surface conditions of the sample accurately reflect the properties of the material being tested. This precision is essential because any deviations in shape or surface deformations can significantly skew the results of tensile tests, leading to data that misrepresents the material's actual characteristics.
Tensile specimens that undergo heat treatment must have ideal shape and integrity. A specimen that is poorly shaped or has undergone deformation is useless for analytical purposes post-heat treatment. Such imperfections could mask the true effects of heat treatment.
Specimen integrity highlights the need for advanced and reliable equipment for tensile sample preparation. Modern specimen preparation equipment offers precision cutting, milling, and polishing capabilities that guarantee specimens meet exacting standards. This equipment minimizes human error and variability, guaranteeing that each specimen is consistent with its counterparts and true to its intended dimensions and finishes. By using state-of-the-art preparation tools, laboratories and testing facilities can uphold the highest levels of accuracy and reliability in their tensile testing processes.
Investing in advanced equipment for tensile sample preparation is not just a matter of convenience but a fundamental requirement for achieving precise and actionable insights from tensile testing.
Best Equipment for Precise Tensile Sample Preparation
At TensileMill CNC we pride ourselves on crafting exceptional equipment customized to meet tensile testing needs. Understanding the necessity of precise specimen preparation, we have dedicated ourselves to developing a top-tier line of equipment, specifically designed to address the unique needs of flat and round tensile sample preparation. Let us show you our best equipment whether you want flat or round tensile samples.
TensileMill CNC MINI for Flat Tensile Specimen Preparation
When it comes to preparing flat tensile samples, there is no better tool than the TensileMill CNC MINI, which stands out as an example of innovation. Contrary to what one might infer from its name, the compact size of the TensileMill CNC MINI belies its comprehensive capabilities and robust performance. Engineered for ultimate flexibility, this machine is not just about preparing tensile specimens but also offers full CNC machining capabilities, meaning it meets a broad spectrum of laboratory needs.
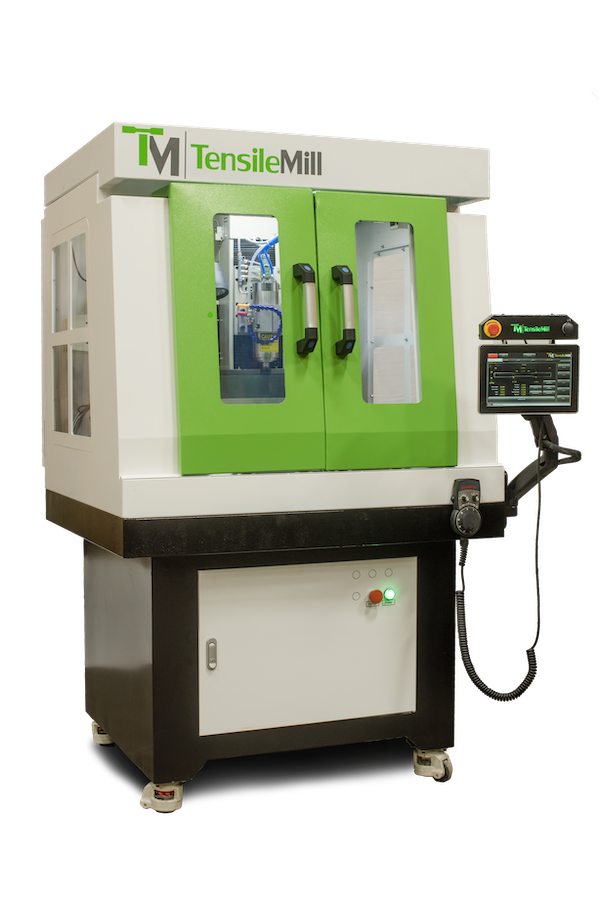
One of the standout features of the TensileMill CNC MINI is its small footprint, making it an ideal choice for laboratories with limited space. Despite its compact design, it offers a larger table size, higher power, and improved precision & repeatability than its predecessors. The machine's design addresses the modern laboratory's need for efficient and reliable specimen preparation without compromising quality or performance.
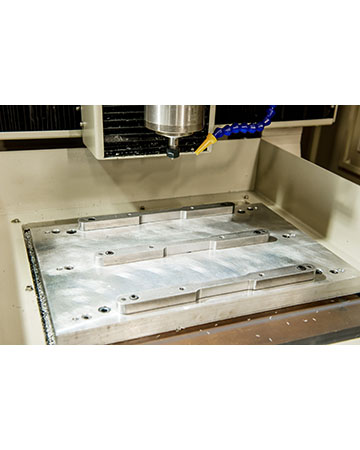
Ease of use is another key feature of the TensileMill CNC MINI, with its machine accommodating even operators untrained in CNC machining. The inclusion of a user-friendly tensile milling interface simplifies the specimen preparation process, allowing for quick and accurate production of specimens conforming to various industry standards like ASTM, ISO, DIN, JIS, and more. The machine's powerful Carbon software enhances its functionality, providing a smooth transition between tensile sample preparation and advanced CNC control functions for broader machining tasks.
Material testing requires accuracy and repeatability. TensileMill CNC MINI delivers both, every time. Its high-performance features, coupled with dedicated tensile software, make it the ideal solution for laboratories aiming for excellence in tensile sample preparation. The machine's ability to prepare an array of materials, from soft metals to hard and Inconel materials, further underscores its versatility and efficacy as a leading solution on the market.
TensileTurn CNC - Industrial Upgrade for Round Sample Preparation
The TensileTurn CNC - Industrial Upgrade Model is expertly designed for complex material testing tasks. Its key feature is the touch screen tensile milling interface, which simplifies the preparation process, enabling operators of any skill level to quickly produce tensile specimens to precise dimensions. Whether working in compliance with common standards such as ASTM, ISO, DIN, etc., or with custom dimensions, this machine is equipped to handle a range of materials with different finishes and automation capabilities, including an automatic center drilling function.
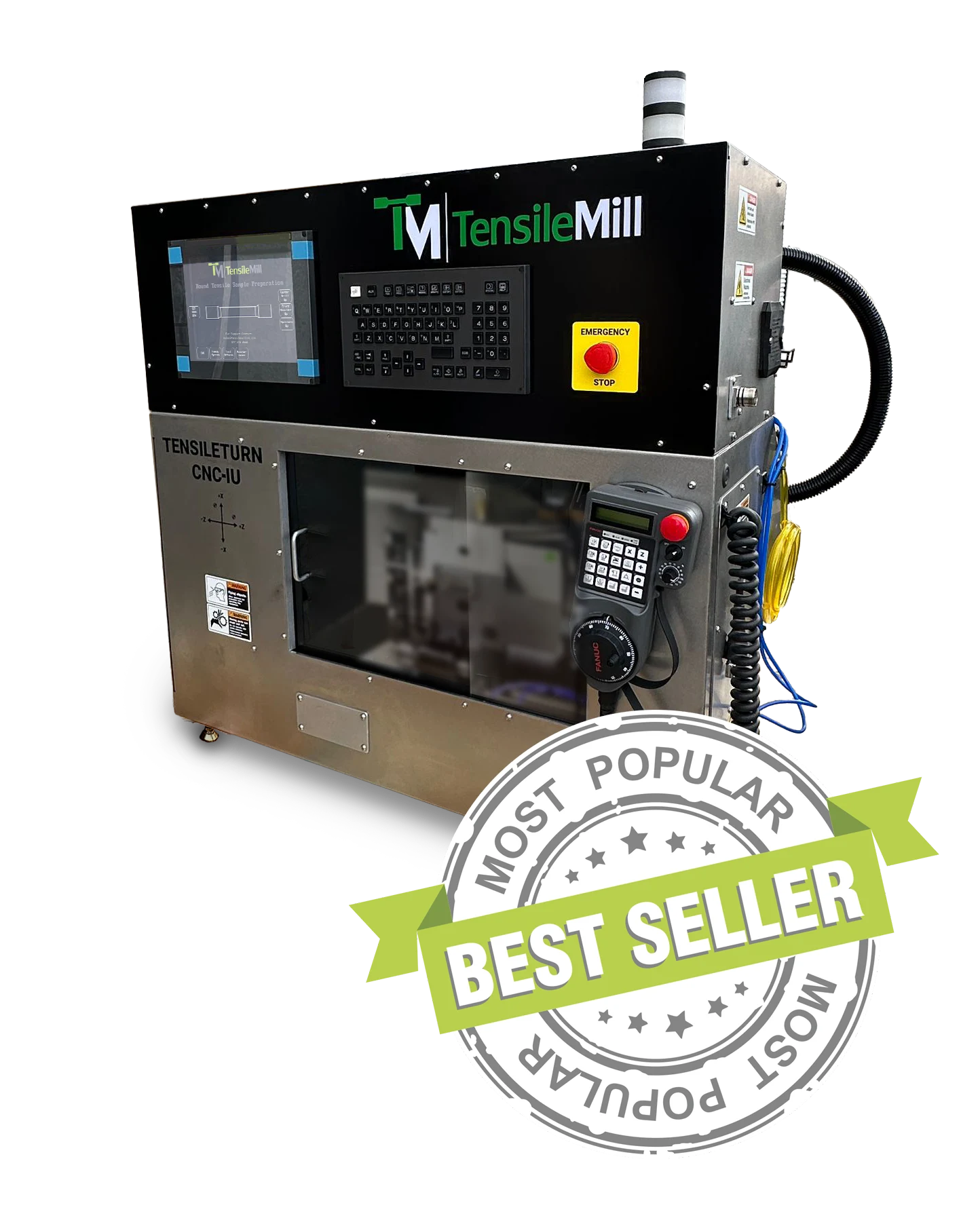
What sets the TensileTurn CNC - Industrial Upgrade apart as the top machine in our lineup for round sample preparation is its combination of user-friendly design with advanced capabilities. The machine is also suitable for untrained CNC machinists due to its turnkey solution and super user-friendly operation.
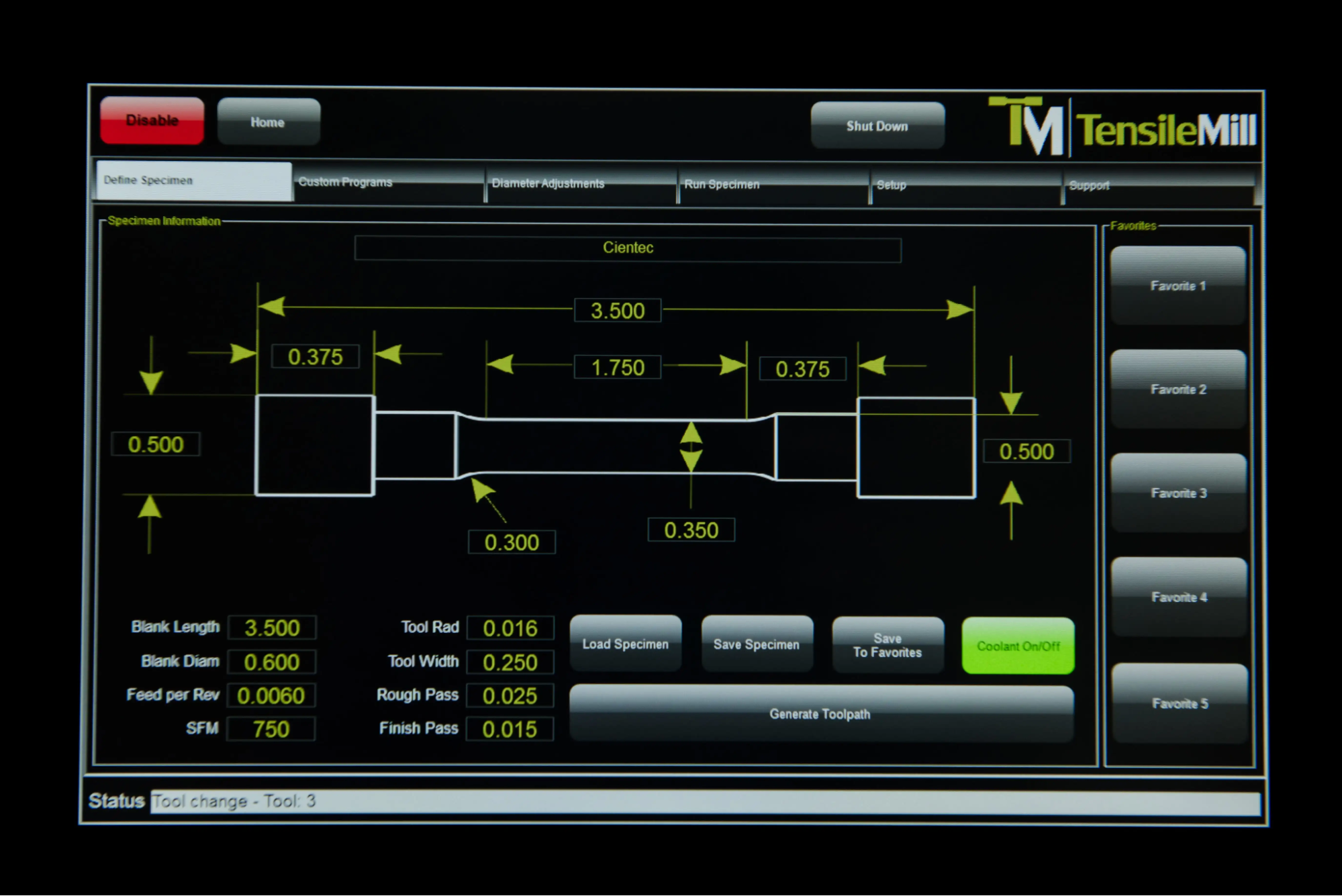
The upgraded version of our classic system, the TensileTurn CNC - Industrial Upgrade Model, features a granite frame and ball screws providing a robust and shock-absorbent foundation necessary for industrial-grade high-speed machining. With a stainless steel enclosure, a powerful 3500 RPM 2 HP motor, and an 8-position turret, it's built to deliver exceptional performance.
Operated via an easy-to-use touchscreen controller integrated with our comprehensive Carbon software, the TensileTurn CNC - Industrial Upgrade provides operators access to professional CNC control functions alongside a tensile milling software interface, making it a hybrid of tensile sample preparation and CNC machine. This adaptability is key to why it stands as the best tool for round sample preparation needs, capable of preparing standard and sub-size round tensile specimens, threaded specimens, button-head tensile bars, fatigue specimens, and more, all with exceptional ease and efficiency.
Exploring Heat Treatment's Impact on Metal Products
Heat treatment extends beyond improving metal products' mechanical properties. It also shapes the functionality and longevity of an array of essential components and tools used in multiple sectors. For instance, in the automotive industry, heat treatment is indispensable for creating parts that can withstand extreme conditions, such as gears and engine components. This process is key to developing materials that can bear automotive high stresses and wear conditions.
In aerospace, the demands for precision, reliability, and performance are even higher. Heat-treated metals are foundational in crafting turbine blades, landing gear components, and structural elements of aircraft. These components benefit from thermal processing that enhances their strength, resist corrosion, and withstand extreme temperatures encountered during flight.
Heat treatment also benefits the construction sector. Tools and machinery exposed to daily wear and tear, and environmental elements are made more durable and resistant to deformation. From high-rise buildings to construction equipment, thermal treatment makes certain these materials can support heavy loads and resist harsh conditions.
Moreover, heat treatment processes have led to specialized techniques like case hardening, induction hardening, and flame hardening. These techniques are customized for specific applications. These processes allow for the selective hardening of metal surfaces, providing wear resistance where it is most needed without compromising the material's overall toughness and ductility.
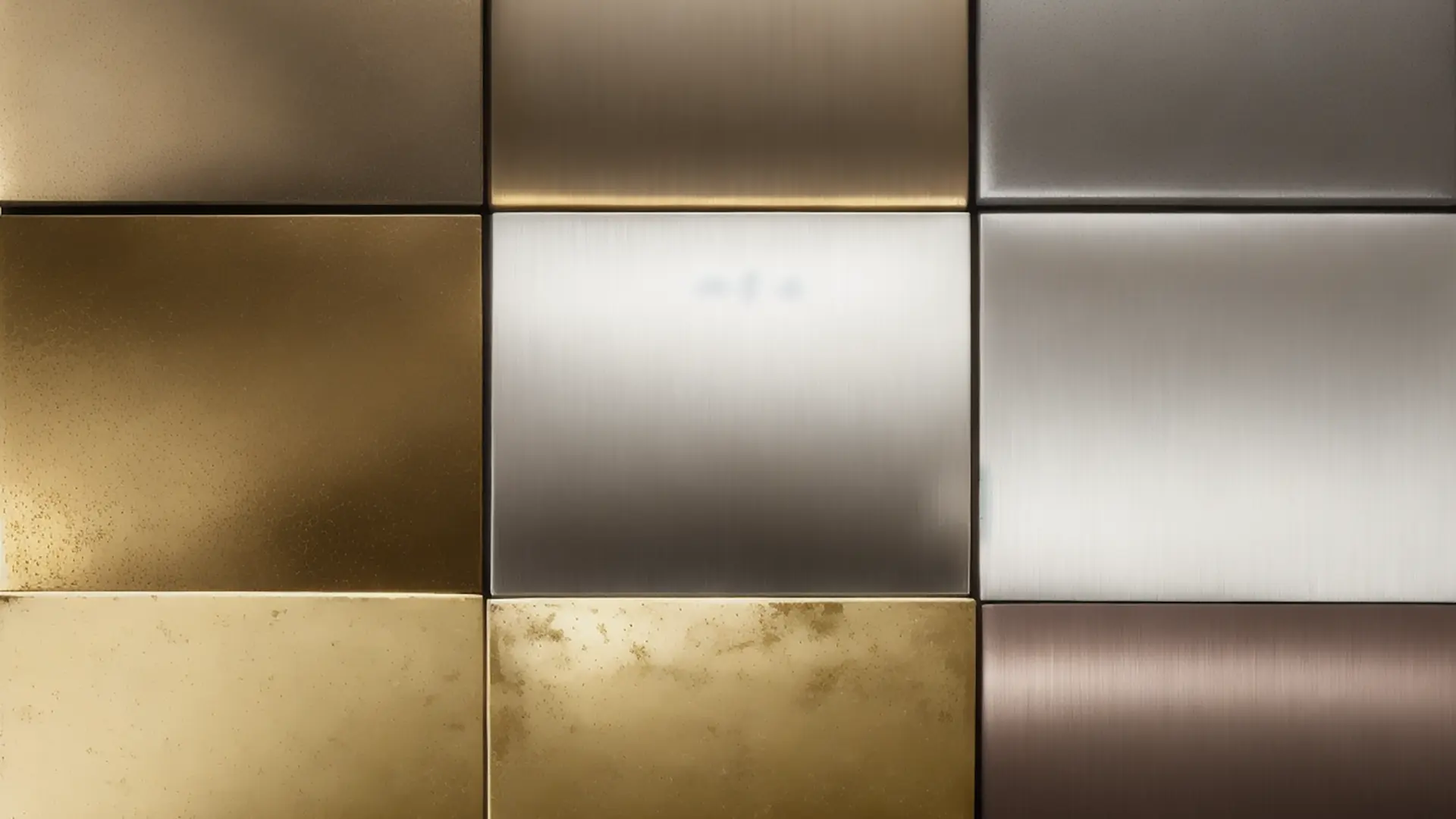
Harnessing Heat Treatment for Tensile Testing Excellence
Heat treatment is crucial in the preparation of tensile samples. This methodological approach guarantees that tensile testing accurately reflects real-world performance. The alteration of a material's microstructure through heat treatment significantly affects its mechanical properties such as yield strength, ultimate tensile strength, and ductility. The use of heat treatment in tensile sample preparation is fundamental for analyzing material's performance and durability.
The process of heat treating tensile samples involves several steps, including selection, cleaning, heat treatment according to desired properties, and post-treatment procedures, to prepare materials for mechanical testing. This process aims to achieve the target microstructure and mechanical properties, making sure that samples accurately represent material's behavior under actual service conditions. Heat treatment innovations, like controlled atmosphere and laser heat treatments, offer precision and efficiency, pushing material engineering.
For those in need of reliable tensile sample preparation, we offer top-tier products, including the TensileMill CNC MINI for flat specimens and the TensileTurn CNC - Industrial Upgrade for round specimens. These tools are designed with precision and ease of use in mind, accommodating both experienced machinists and newcomers.
At TensileMill CNC, we are committed to supporting your tensile testing needs with advanced equipment and expert services. Whether you are looking for equipment to prepare tensile samples or need specialized assistance, you can directly contact us or request an online quote. Our team is here to provide the solutions you need for accurate and efficient tensile testing.