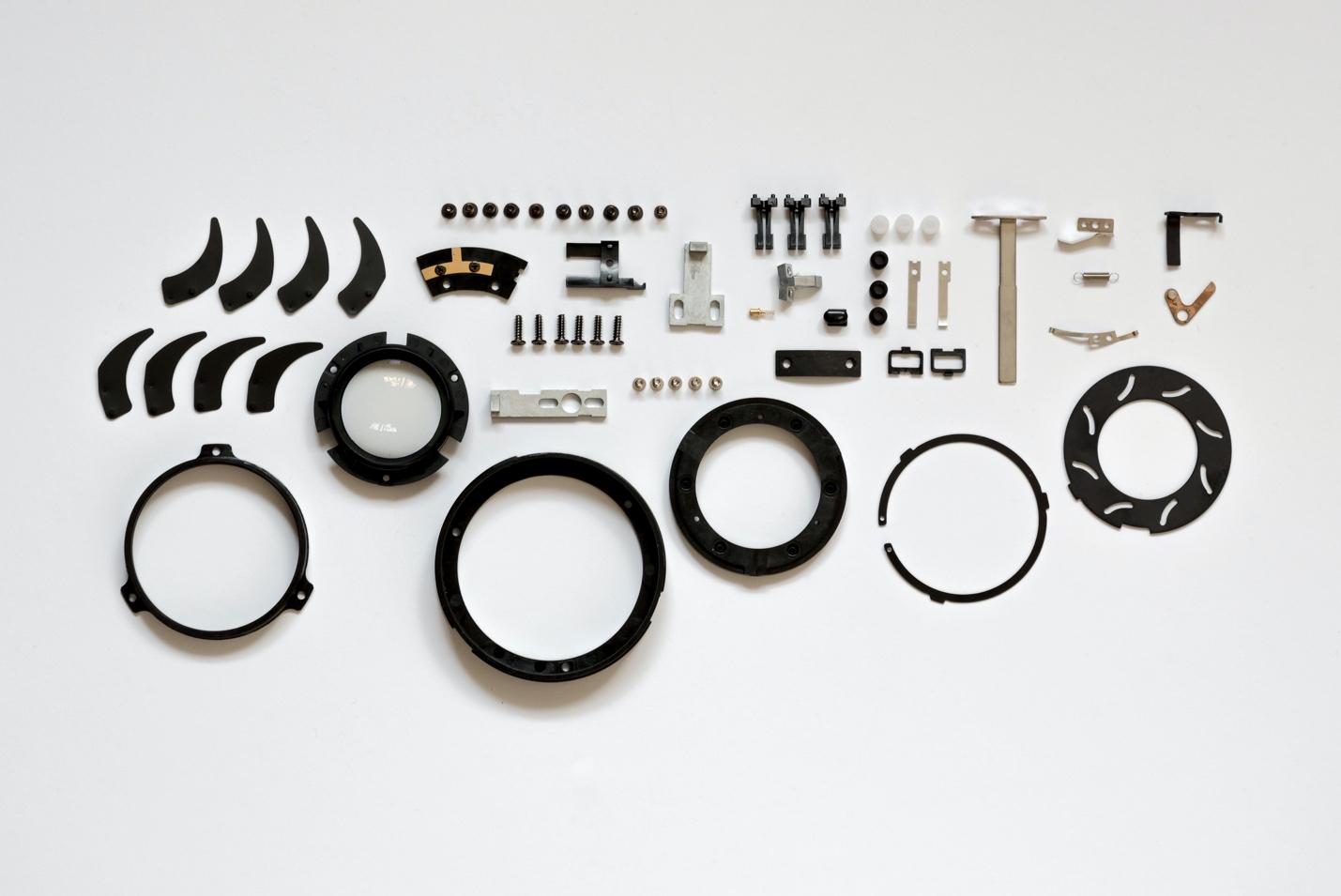
What determine the key mechanical properties of metals - hardness/softness and strength/brittleness and toughness? How does heat treatment of metals work to create the hardest and most long-lasting parts? What guarantees the quality of metal products in production? Let's take a closer look.
Introduction
In the minds of the average person without special education, metallurgy consists of a simple list of sequential actions, such as mining various metals, fusing them in certain proportions, and casting the alloys into molds, followed by machining the hardened billets. Looking at the periodic table of elements, which contains almost a hundred different metals, it is easy to confirm this concept of metallurgy. After all, the variety of alloys used in technology and the variability of their properties could seemingly be explained by the combination of these metal elements in different proportions. However, this view is not only inaccurate, it is wrong. So what exactly is going on in reality?
Metal Alloys: a Brief Overview
First of all, not all metals can be used to create structural alloys and products made from these alloys. In fact, the list of common engineering metals is quite small and includes only eight elements: iron, aluminum, copper, chromium, nickel, titanium, zinc, and magnesium. Other metals are not as common, but are still important in various industries. These include mercury, tungsten, cobalt, tantalum, and rhenium. Precious metals, gold, silver, platinum, and palladium, are also used not only in financial and jewelry businesses, but also in technology due to their unique properties.
It should be noted that there are some industries that use specific metals for specific purposes. For example, depleted uranium is used in the military to create armor-piercing projectiles due to its uniquely high mass density, which gives the projectile increased kinetic energy. This property also makes the metal more resistant to impact and suitable for making armor. For example, the latest modifications of Abrams tanks produced after 1998 contain depleted uranium armor elements in the front hull and turret.
Lead is also used to protect against ionizing radiation due to its high density, which contributes to efficient radiation absorption. Rhodium has extremely high corrosion and chemical resistance and very low electrical resistance, so it is valued as a material for electrical contacts and electroplating. It is also a material for neutron flux detectors in nuclear reactors.
Secondly, not all of these metals can be mixed in the liquid state to form alloys: some metals do not dissolve in each other, or separate from each other when cooled, forming a solid mixture of metals.
Thirdly, metals are the main components of alloys, but nonmetals are also extremely important for them. For example, carbon is contained in steel (usually up to 2%) and in cast iron (from 2 to 4.5%). The alloying process should also be considered in this context. Alloying in metallurgy is the introduction of elemental impurities into metal alloys to help produce materials of a given chemical composition and structure with the required physical, chemical and mechanical properties. In fact, alloying is the process that is most responsible for the creation of the entire variety of alloys. These are mostly non-metallic elements: chromium, nickel, manganese, tungsten, titanium, tantalum, aluminum, vanadium, copper, cobalt, niobium, zirconium, and rare earth metals. However, the nonmetals silicon, boron, selenium, and nitrogen can be used as alloying elements.
Finally, the properties of alloys depend not only on their composition, but also on the way the metal is processed. Here we are getting closer to the heat treatment process. But before it, we need to understand what the structure of an alloy is, because it changes under the influence of heat treatment, ultimately changing the properties of the alloy.
Structure of Alloys
There are three types of alloys: solid solutions, chemical compounds, and mixtures:
- Solid solution alloys are characterized by the fact that during their formation, one component (the solvent) retains its crystal structure, and the atoms of the other one (the dissolved component) are arranged in the crystal phase of the solvent. In such alloys, the atoms of the dissolved component are arranged in a disordered fashion.
- Chemical compounds are formed when a chemical reaction occurs between alloy components to form a new compound. These can be combinations of metals with nonmetals, as well as compounds containing two or more metals. In their pure form, they have a single-phase structure with an ordered arrangement of component atoms.
- Mixtures are formed by components that do not dissolve in each other in the solid state and are also incapable of chemical interaction to form a compound. In mixture alloys, each component retains its own crystal lattice. The structure of the mixture is heterogeneous, consisting of two or more phases. The mechanical properties of mixtures depend on the quantitative ratio of the components, as well as on the size and shape of the phases (grains).
In addition, there are components that can form several different phases depending on the conditions of heating and cooling of the alloy.
In practice, things are still much more complicated. After all, real alloys, such as the most common steel and cast iron, are actually complex mixtures of many phases that are formed depending on their composition, melt cooling conditions, and subsequent mechanical and heat treatment of billets and products.
Heat treatment results in changes in phase composition, grain size reduction or enlargement, redistribution of impurities, and surface modification. All these processes change the properties of the final material.
For the manufacture of tool parts and stamping dies, the most common material is hard and durable steel grades. This is due not only to its specified mechanical properties, but also to its availability. However, other materials such as hard metals, carbides or special alloys can be used in certain cases, depending on the specific material requirements and application conditions.
Steel vs. Cast Iron in Tool & Die Sector
As we have already mentioned, steel and cast iron are two different types of iron alloys, and they have different compositions, properties, and uses. It is widely believed that the main difference between these alloys is the carbon content. Cast iron contains more than 2% carbon, while steel contains less than 2%. This is largely true, but there are steel grades that have a carbon content of up to 3%. But that doesn't make it cast iron. So how can one clearly distinguish between cast iron and steel?
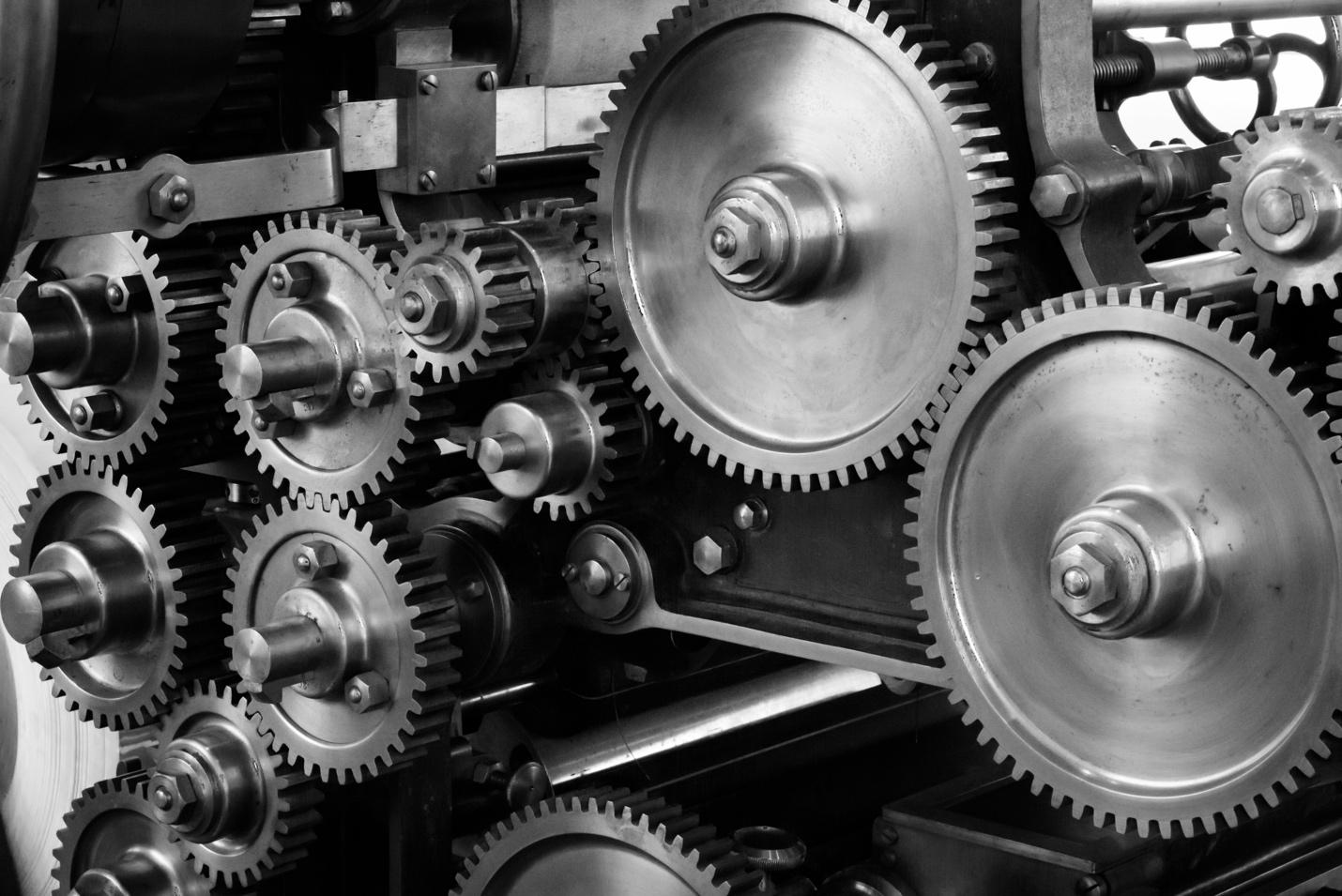
The main feature that helps to distinguish between cast iron and steel is the microstructure of the material. In cast iron, the microstructure usually consists of a large number of carbon inclusions (graphite and iron carbide phases), which gives it its brittleness. Steel, on the other hand, has a much more homogeneous microstructure with no visible carbon inclusions, and it usually has better mechanical properties such as ductility and strength.
Appearance can also help distinguish cast iron from steel. Graphite is black and iron carbide is white, so cast iron is usually gray to white. Cast iron can be made black by special heat treatment of its surface. The surface of cast iron is rougher, rougher, also because of its grain structure. Steel usually has a smoother surface and can have a variety of colors, including silver, blue, or even black, also depending on the treatment and coating.
For technical applications, the most important difference in mechanical properties of cast iron and steel is the following:
- Cast iron has a lower hardness than steel, it is a softer material that is less resistant to scratches and wear.
- Steel has higher strength compared to cast iron. It can withstand higher loads and provide better resistance to deflection and tearing.
- Steel has a higher yield strength and tensile strength than cast iron. This means that steel can deform more before breaking and has better ductility.
- Cast iron has a higher stiffness (lower flexibility) than steel. This means that it is less flexible and less able to absorb shocks.
- have sufficient hardness to provide resistance to wear and scratches
- be strong enough to withstand heavy loads without deformation or fracture
- have high wear resistance, as they are subjected to prolonged mechanical stress
- have sufficient heat resistance to maintain their reliability when the tools or dies are used at high temperatures
- if the tools or dies are used in conditions where there may be interaction with aggressive media or liquids, it is important to have alloys that have high corrosion resistance.
- High-Speed Steel - one of the most common materials for the manufacture of tools for cutting, drilling, milling and reaming metal materials.
- Carbon Steel - for stamping and forging, it has high strength and wear resistance, which allows it to be used for processing high-stiffness materials, such as stainless steel or aluminum.
- Hot Work Tool Steels - used for the manufacture of dies and tools used at high temperatures during hot stamping of metal blanks.
- Manganese Steels - high toughness allows for effective absorption of impact energy, strengthening the surface layer, they are used for stamping soft insulating materials such as rubber or plastic.
- Special Stainless Steels are used for processing specific materials, such as plastic or food, where high corrosion resistance is required.
- Quenching: The part is heated to a high temperature and cooled rapidly, changing the microstructure of the material, which improves mechanical properties such as hardness, strength, and wear resistance.
- Tempering: a process used after quenching to reduce brittleness and internal stresses. The part is heated to a certain temperature and held at that temperature for a certain time, and then slowly cooled. This process reduces stiffness and improves ductility. Internal stresses can occur in the previous procedure due to a sharp temperature difference and make it difficult to further process and use the product, cause cracking or fracture.
- Normalization is a process similar to tempering, but performed at a higher temperature. In addition to removing internal stresses, it is used to improve structural homogeneity and ensure uniform material strengthening throughout the part. The part is heated to a critical temperature, held for a certain time, and then slowly cooled in air or with the help of special cooling media.
- Thermochemical Treatment: a group of processes that occur on the metal surface, changing its properties. The interaction of the material surface with an atmosphere of chemicals containing carbon or nitrogen contributes to the formation of a coating on the surface of the part. This coating improves the strength, wear resistance, and corrosion resistance of the part without increasing the brittleness of the base material.
- Straightening: is a process by which deformations and deviations that occur during machining and heat treatment are corrected. Straightening can include mechanical straightening, hydraulic straightening, or thermal straightening, depending on the shape, size, and complexity of the part.
It is important to keep in mind that the chemical composition and processing method can affect the mechanical properties of both cast iron and steel.
Another way to distinguish between cast iron and steel is to use a magnet. Cast iron has ferromagnetic properties, meaning it attracts a magnet, while most steel grades are paramagnetic or non-magnetic and do not interact with a magnet. However, it is worth noting that some specialty steels can be magnetic, and some cast irons exhibit very weak magnetic properties. So this factor is not categorical.
Usually, a combination of microstructure, appearance, and magnetic response data can be sufficient to distinguish between cast iron and steel.
Which Alloys Guarantee Hardness and Strength of Tools and Dies?
When selecting alloys for the production of tools and dies, various criteria are used, taking into account the material requirements and the conditions of its application. Tools and dies must:
In general, we can say that special high-strength steels with a high content of carbon and other alloying elements can meet these requirements, among the following types.
Cemented Carbides, such as tungsten carbides or ceramic materials, are also used to make tools that require ultra-high hardness and wear resistance. High-temperature alloys (e.g., nickel alloys) can provide increased temperature resistance: they are used for stamping and forming materials at very high temperatures, for example, in the aviation industry.
The choice of material must also take into account economic constraints and be competitive in terms of production costs. Professional engineers usually take these criteria into account and conduct material testing to find the optimal solution. By the way, TensileMill CNC Inc. is well known for the quality of its software-controlled tensile testing machines. The Flat Specimen Preparation Equipment Lineup (for dog bones) and Round Specimen Preparation machines are already well established in the testing equipment market. Recently, the company has entered the market with a new offering of its Tensile Testing Equipment. These lines of equipment will help determine the optimal material for the tool and die sector.
In the next part of the article, we will discuss the most important methods of heat treatment of metals that make tools and dies even more reliable.
The Most Important Methods of Heat Treatment of Working Parts of Tools and Stamping Dies
Heat treatment is a technological process that involves changing the structure of metals and alloys by heating, holding at high temperature and cooling in accordance with a special regime, and thereby changing the mechanical and physical properties of metals and alloys, as well as the chemical properties of their surface, without significantly changing the geometry of the part. It is the conditions of heating, holding and cooling that determine the variety of heat treatment methods.
Therefore, heat treatment can be used to improve the properties of already formed products, which may require minor operations such as grinding or minor dimensional adjustments after such treatment.
For the tool and die sector, the following five heat treatment methods are the most important.
Professional technologists use various methods to monitor mechanical, physical, and property data after each heat treatment operation to gain a clear understanding of its effect on these properties. From this data, processing technologies are created, which can include one to many such operations. It is also possible to repeat them several times, depending on the technical task. Thus, the reliability of property control methods becomes a guarantee of the effectiveness of the developed technology, which is also used for current quality control of products in production.
Heat Treating and Tensile Testing
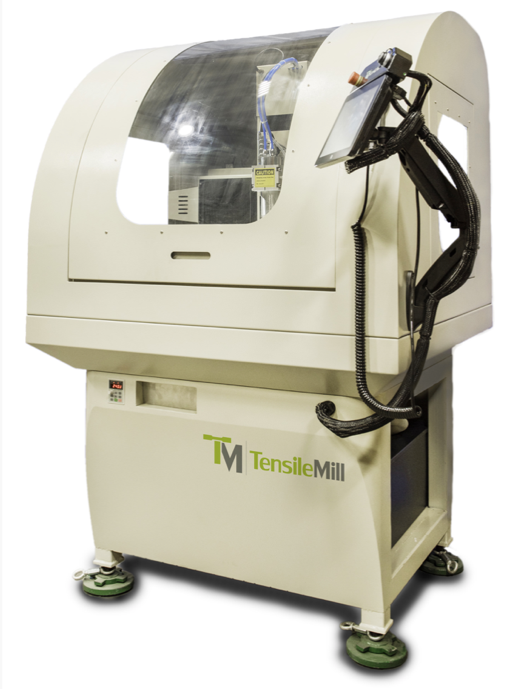
Studying mechanical properties is an important step in optimizing the technology for creating tool parts and stamping dies. Performing this control after each heat treatment operation allows you to see the full picture of their impact on the properties, and thus create the most effective sequence of treatment procedures. In the future, such control methods can be used for periodic in-line monitoring of product quality in production.
One of the most important methods of testing mechanical properties is tensile testing of materials. Special test devices have been developed for this purpose. The best example is the Tensile Testing Equipment & consumables from TensileMill CNC Inc. During the test, a gradually increasing tensile load is applied to the material sample, measuring the change in its geometry.
The data is accumulated on the change in the geometry of the part until it breaks, and it is used to calculate the tensile strength, maximum elongation and contraction. This gives information about the strength and ductility of the material under load, which can be compared with the data for samples before the heat treatment procedure. Also, in ongoing quality control, these data must meet certain standards developed for the product.
Tensile test specimens are cut from parts in the form of flat or round oblong parts that are flared at the ends and tapered in the middle. The widened ends are used for fixation in the tensile testing machine, and the main changes under load occur in the narrow part of the specimen, where it eventually breaks. There are a large number of standardized round and flat specimen shapes of various sizes that are used to test different products. Given that tensile test results are highly dependent on the accuracy of the specimen shape, TensileMill CNC Inc. milling and turning machines ensure this accuracy by providing software process control and a library of standard specimen sizes.
The Flat Specimen Preparation Equipment Lineup and Round Specimen Preparation machines guarantee the exact reproduction of the tensile shape of samples, and in combination with Tensile Testing Equipment from TensileMill CNC Inc. the reliability of the entire measurement process becomes ideal. You can also check our partners for your metal & other material testing equipment.