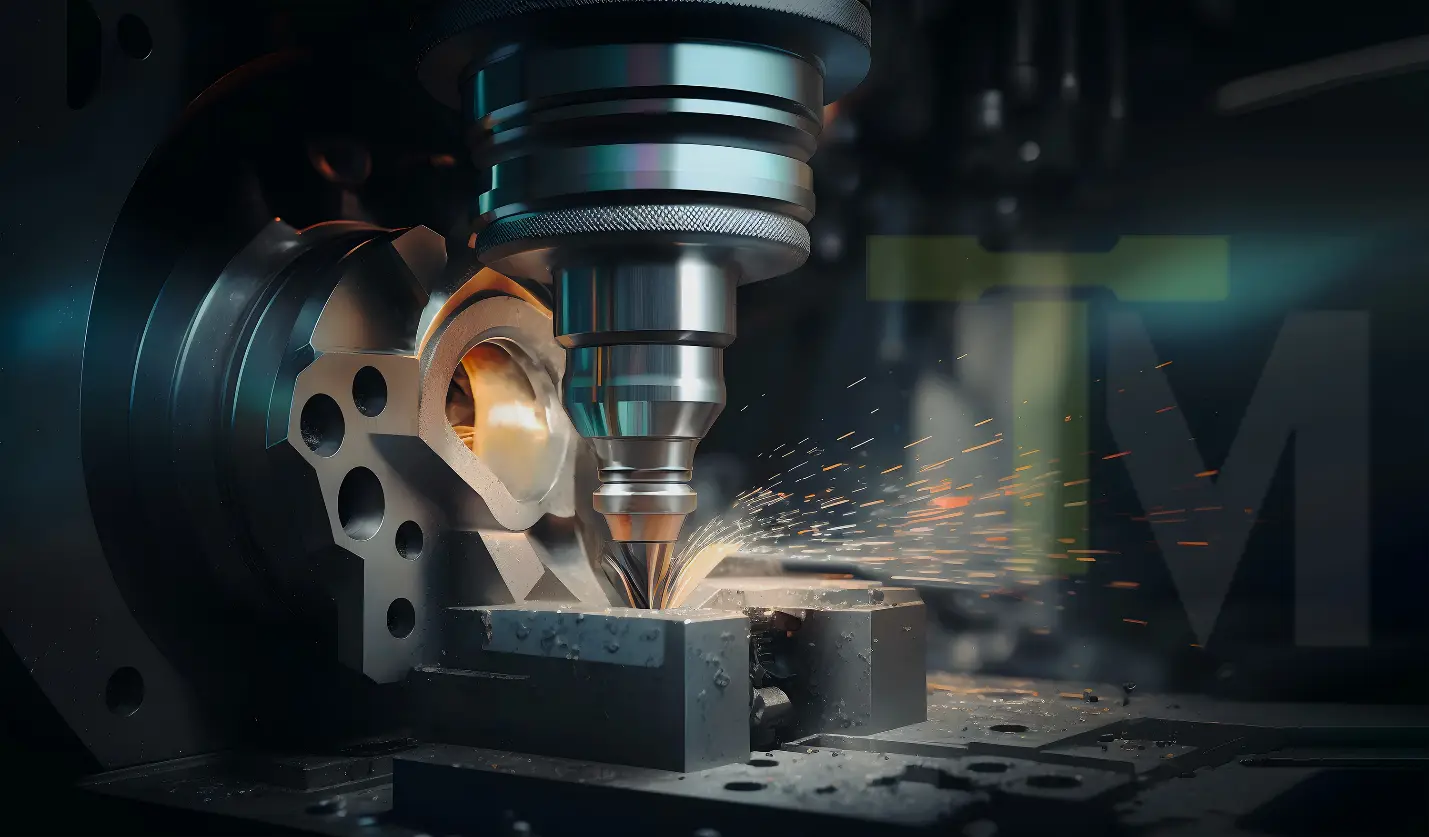
In North America's industrial sector, precise quality control for tools, especially in tensile testing, is non-negotiable. There are many industries where quality assurance and tensile quality control are required. These industries include, but are not limited to aerospace, automotive, and construction. These tools, pivotal in shaping vital components of daily life, directly influence product safety, efficiency, and longevity. Any mistakes can result in production errors, higher costs, and potential dangers. Thus, a strong quality control system guarantees the best performance of tools and their alignment with set standards.
The North American industrial tool market, known for precision and innovation, demands tools of unparalleled durability and adaptability. In an age of global competition, only the highest standards suffice. To ensure this caliber of excellence, specialized testing methodologies have been developed, assessing attributes from tensile strength to environmental resilience. In this article, we examine 12 critical quality control tests that are essential for North American industrial tools.
Standardization of Quality Control Testing
The creation of standard-setting groups was a key step in improving quality control in manufacturing, especially in tensile testing. For example, when considering tensile testing methodologies, groups such as ASTM, ISO, DIN, and JIS have established clear and stringent rules. By following these standards, manufacturers know their materials can handle real-world stresses. These groups made sure that no matter where a product was made, it followed the same high-quality and safety standards. Their rules gave manufacturers a clear set of steps to follow, focusing on doing things the same way every time, with care and accuracy. This approach built trust in products and made global trade smoother, as businesses knew that products from different places would meet the same strict standards.
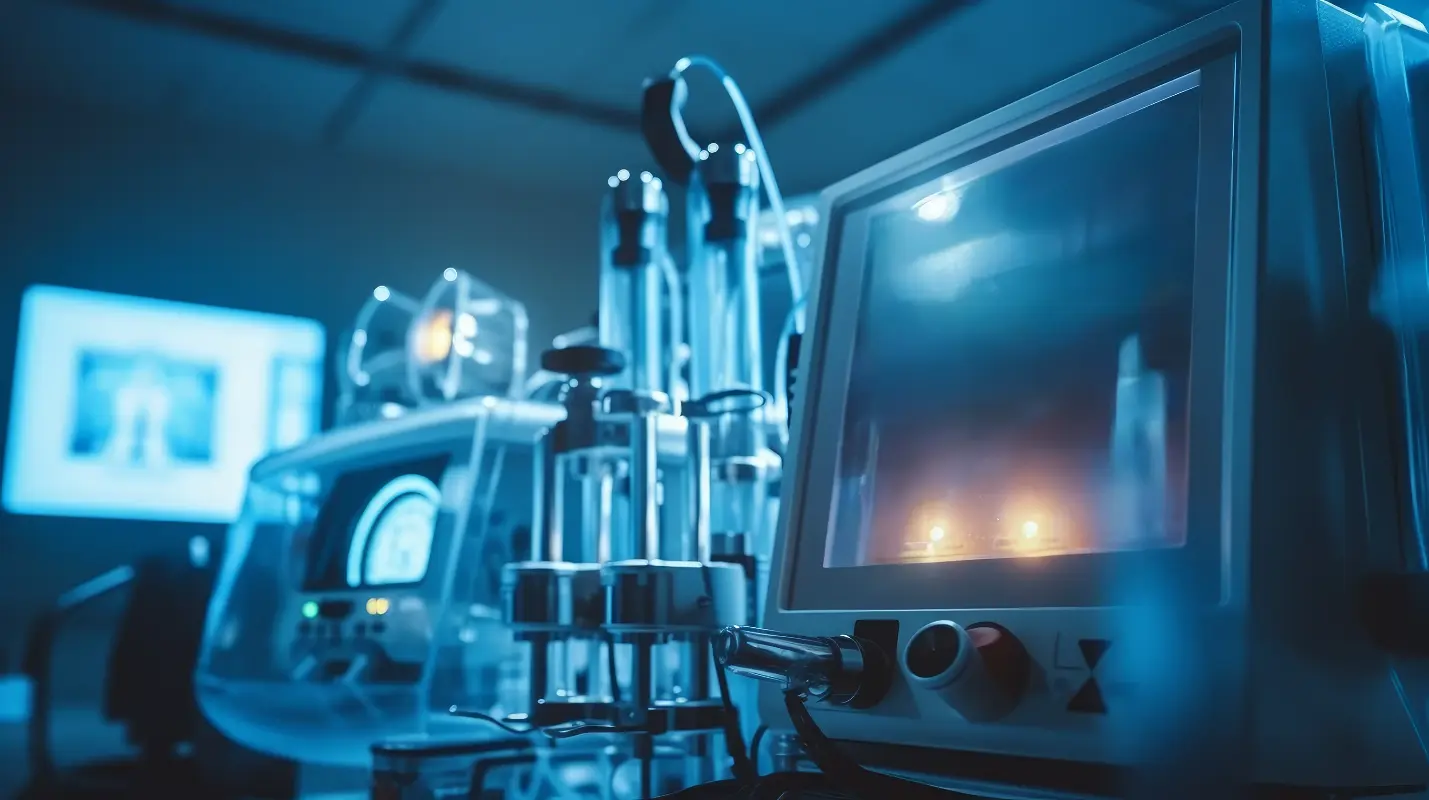
Regulatory Oversight and its Role in Upholding Quality Control
Quality control is vital to ensure products are safe, reliable, and adhere to established standards. While its significance is universally acknowledged, certain sectors prioritize it due to errors' significant implications. Let's examine a few of the major industries such as aviation, automotive, energy, maritime, construction, and mining sectors. Each of these sectors places a strong emphasis on stringent quality inspections.
Aviation Sector
The aviation sector, which includes a wide range of manufacturers, suppliers, and operators, upholds some of the strictest quality control standards in the world. Aircraft are marvels of modern engineering, comprising millions of parts. Every component, be it an engine turbine blade or an electronics chip inside an avionics system, must meet precise specifications. Even the smallest failure can lead to catastrophic results. Beyond immediate safety concerns, the financial implications of grounding aircraft due to quality issues are significant. Quality control remains the foundation of aviation from the initial design phase to regular maintenance checks.
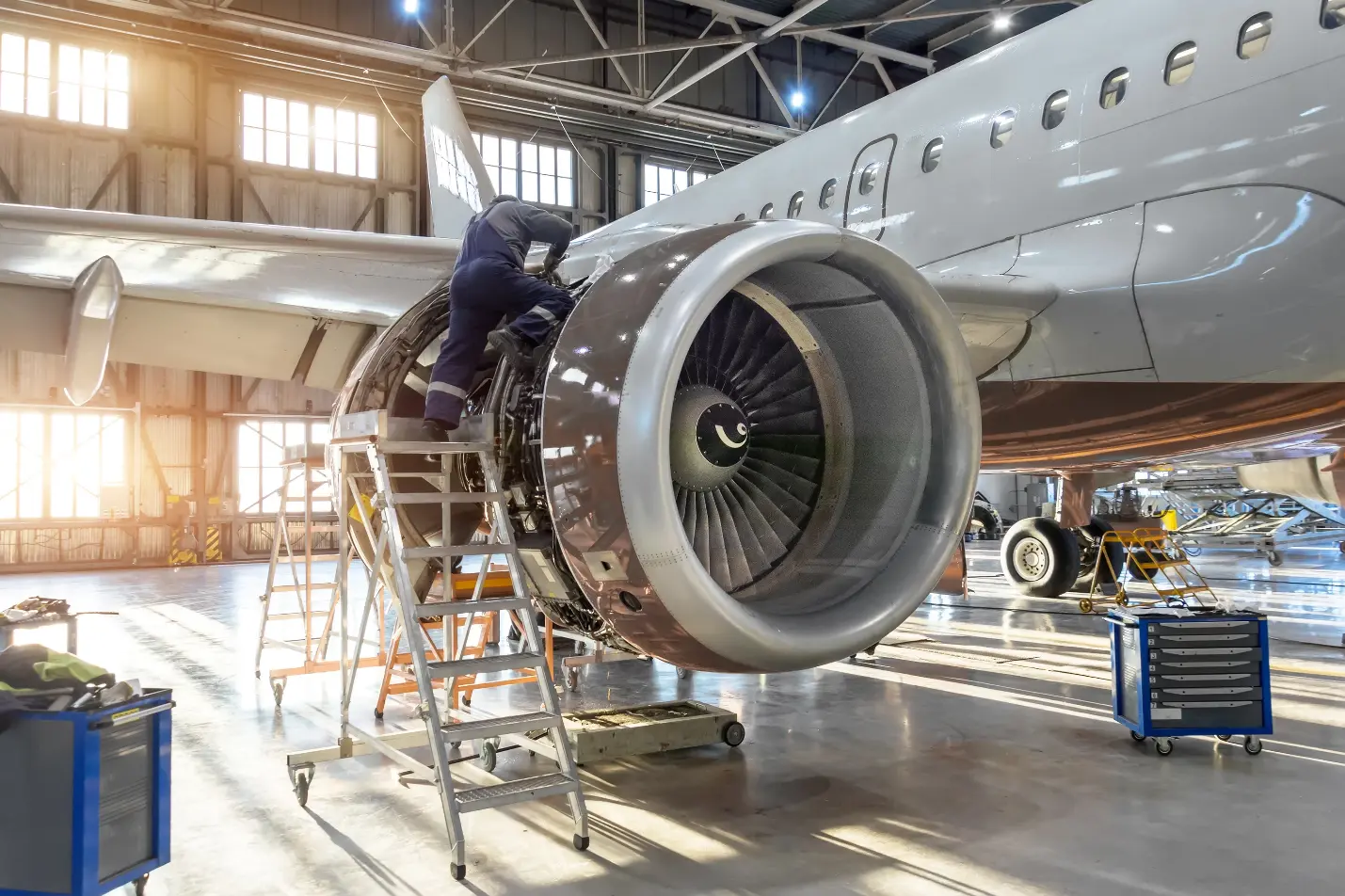
Examples of essential industrial tools in the aviation sector include:
- Composite Autoclave: A device used for the thermal processing of composite materials in aviation.
- Rivet Gun: A handheld tool for fastening structural components of an aircraft with rivets.
- Spectrum Analyzer: An instrument for testing and analyzing electronic systems in aviation.
Energy Sector
The energy sector underpins the modern world's functioning, ensuring homes are illuminated, industries operate, and data centers support the digital ecosystem. Given the critical nature of the energy supply, there's no space for error. Power plants, whether renewable or fossil-fueled, must operate optimally and safely. Quality control measures ensure power generation reliability, minimizing outage risk. Moreover, with the global push towards cleaner energy, quality checks verify that the latest technologies and systems adhere to environmental standards, reducing carbon footprints.
Here are examples of essential instruments utilized in the energy sector:
- Turbine Control Systems: Advanced mechanisms that manage the operations of turbines, especially in wind and hydroelectric power plants.
- Photovoltaic (PV) Testers: Instruments used to measure the efficiency and performance of solar panels.
- Circuit Breaker Analyzers: Devices that assess the functionality and reliability of circuit breakers in power grids and plants.
Maritime Sector
The maritime industry, with its age-old legacy, moves over 80% of global trade. The harsh marine conditions, characterized by aggressive saltwater, intense waves, and unpredictable weather, demand robust and durable equipment. It is crucial that these ships are built to withstand such adversities, with stringent attention given to the structural integrity of the hull and the efficacy of onboard systems. Comprehensive quality control is essential to ensure safe and dependable ocean navigation. Moreover, as the world pivots towards environmental conservation, maritime ships must meet rigorous emission standards, highlighting the need for precise quality assessments.
Here are examples of vital instruments employed in the maritime sector:
- Echosounders: Devices that determine water depth by measuring the time it takes for sound echoes to return from the seabed.
- Marine GPS Systems: Precision navigation tools that help vessels maintain their course and avoid potential hazards.
- Ballast Water Treatment Systems: Instruments that manage and treat ballast water in ships, ensuring it meets international environmental standards.
Automotive Sector
In modern automobiles, mechanical components are integrated with advanced electronics to enhance safety, efficiency, and comfort. As the automotive sector races toward autonomous driving, quality control becomes even more important. The failure of any component, whether in a braking system or a sensor interpreting data, can lead to severe accidents. Additionally, with consumers becoming increasingly environmentally conscious, the pressure on automobile manufacturers to produce energy-efficient and low-emission vehicles requires rigorous testing and quality assurance of every component.
Here are some examples of industrial tools used in the automotive industry:
- Welding Machines: Various types of welding methods like arc welding, MIG (Metal Inert Gas) welding, and spot welding are employed.
- Automotive Lifts: These are used to raise vehicles off the ground to allow mechanics to work underneath them.
- Body Repair Tools: Includes tools like body hammers, dent pullers, and hydraulic spreaders for repairing dents and damages.
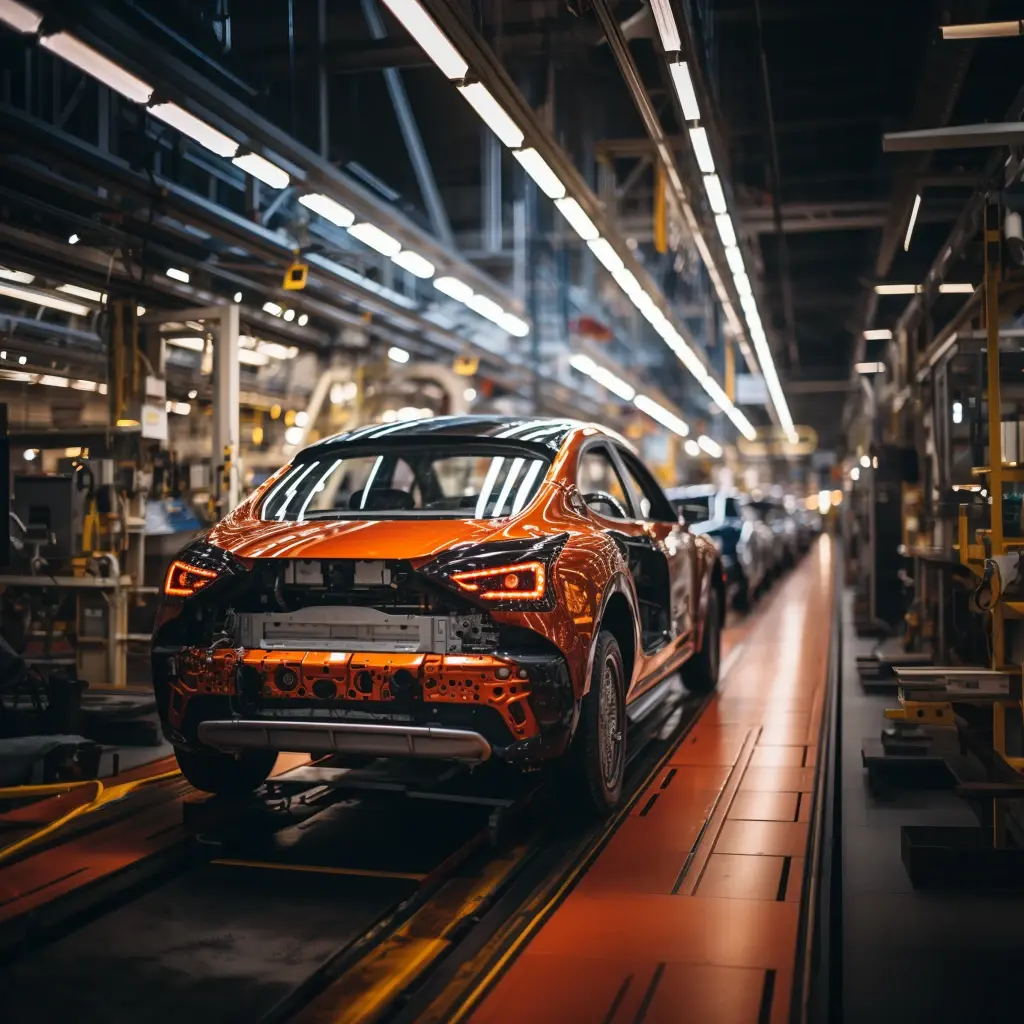
Construction Sector
Construction is the foundation of urbanization and progress. It creates everything from towering skyscrapers to foundational bridges and residential homes. These structures must be permanent and safe. This industry is bound by rigorous quality control measures that guarantee each project's longevity and safety. The quality of raw materials, construction teams' expertise, and equipment accuracy all play pivotal roles. Quality defects can result in substantial economic setbacks and, more critically, endanger lives. As architectural innovations and novel materials emerge, the emphasis on stringent quality evaluations in construction becomes even more paramount. This ensures our built environment's durability and safety.
In the construction sector, some of the essential tools include:
- Concrete Mixers: Machines used to combine cement, aggregate (such as sand or gravel), and water to form concrete.
- Laser Distance Measurers: Electronic devices that use lasers to accurately measure distances.
- Load-Bearing Cranes: Heavy equipment used for lifting and moving large objects during construction.
Mining Sector
Mining is the backbone of numerous industries, providing essential raw materials for everything from electronics to energy production. When working in harsh and unpredictable environments, mining projects demand robust quality control to ensure worker safety and operational efficiency. Extracted ores and minerals must meet specific purity levels to be viable for further processing. Moreover, the machinery used in this industry, often worth millions, must be resilient to the challenging conditions of the mine while maintaining operational efficiency. As the world pushes for sustainable and environmentally friendly mining practices, quality control also ensures that environmental impact is kept to a minimum. This protects ecosystems while providing essential resources. With these dual challenges of safety and sustainability, the mining industry's commitment to stringent quality control measures is evident.
In the mining sector, some of the essential tools include:
- Drill Rigs: Used to create holes in the earth to extract minerals. Their precision and durability are paramount for safe and efficient extraction.
- Bulldozers: These heavy machines move large amounts of overburden and are crucial for site preparation and rehabilitation.
- Flotation Machines: Employed in mineral processing to separate valuable minerals from waste based on their differences in hydrophobicity. Their performance determines the quality and quantity of minerals extracted.
12 Essential Quality Control Methods for North American Industrial Tools
Tensile Testing
Tensile testing, commonly known as a pull test, evaluates strength and durability. In this test, a specifically shaped specimen is stretched until it breaks, measuring its resistance to a force pulling it apart. Key outcomes include Ultimate Tensile Strength (the maximum stress before breaking), Yield Strength (stress causing permanent deformation), Elongation (how much it can stretch before breaking), and Modulus of Elasticity (material stiffness). These results guide engineers in material selection for various industries like aerospace, automotive, and construction, ensuring durability and safety in end products.
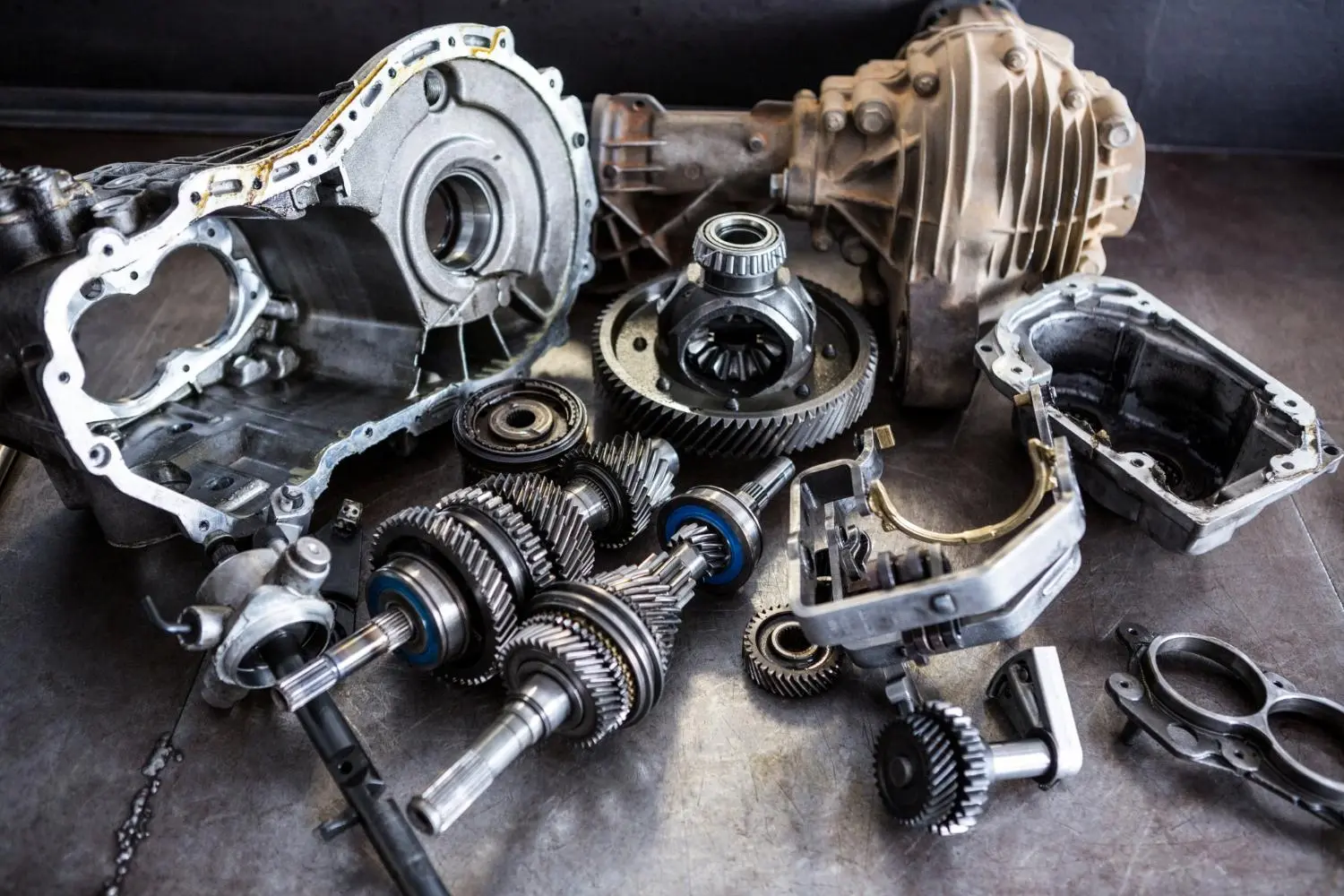
In tensile testing, results integrity depends on the specimen quality. Properly prepared specimens are indispensable for achieving consistent and reliable results. TensileMill CNC offers advanced machines that are designed to elevate your testing quality. Our round tensile sample preparation machines are capable of handling round, square, or irregular samples.
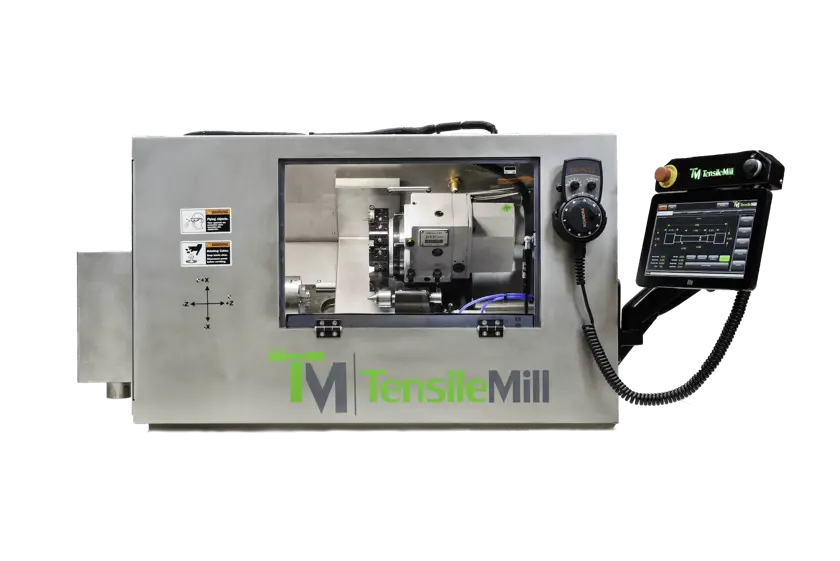
On the other hand, for those requiring flat tensile samples, we have available specialized flat sample preparation machines. They ensure unparalleled precision and efficiency, enhancing the tensile testing reliability of your tests. Such machines are equipped with intuitive software and essential components to ensure durability and user-friendliness.
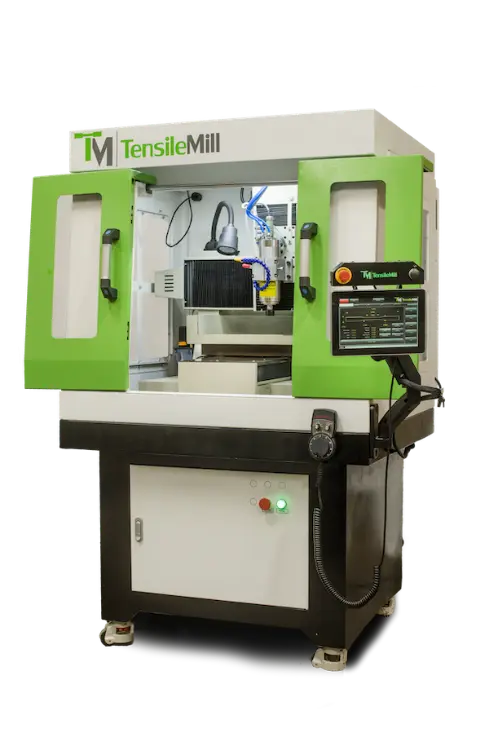
Abrasion Testing
Abrasion testing is essential in evaluating the durability and wear resistance of the materials used in industrial tools. Throughout this test, a sample from the tool is exposed to methodical abrasion following a standard protocol. The extent of wear or the volume of eroded material provides insights into the tool material's quality and potential longevity in real-world usage. Such insights are particularly valuable in sectors where tools confront regular friction and must sustain their shape and efficiency over time, such as in the manufacturing of machinery, heavy-duty equipment, or precision instruments.
Vibration Testing
Vibration testing is essential in determining a tool's resilience and response to various vibrational forces. Tools subjected to regular vibrations can lose functionality and wear out quickly. Moreover, excessive vibration can negatively impact user comfort, leading to fatigue or long-term health issues. Testing ensures tools remain dependable and comfortable for users, even in high-vibration settings. Employing precise testing equipment is crucial in ensuring accurate results, safeguarding both the tool's longevity and the user's well-being.
Impact Testing
Impact testing is essential for determining a material's resistance to sudden applied forces and inherent toughness. During this test, a specimen is subjected to sudden impact using a pendulum. This simulates real-world conditions where materials experience sudden shocks or stresses. The energy absorbed by the specimen during fracture provides valuable insights into its toughness and ability to withstand unexpected forces. Such knowledge is vital in industries where materials must resist sudden impacts without failing, such as automotive safety components, construction materials, or protective gear.
Hardness Testing
Hardness testing is crucial in evaluating an industrial tool's resistance to permanent deformation. Typically, this resistance is assessed by measuring a tool's ability to resist deformation or scratching. Such tests are critical for understanding the resilience and longevity of industrial tools. They ensure they can endure specific forces or wear without deformative effects. The significance of these tests is profound, influencing various sectors such as manufacturing, metallurgy, and engineering where the durability and strength of tools are vital.

Electrical Safety Testing
Electrical Safety Testing is paramount for power or electronic tools, ensuring they operate without electrical risks. This testing identifies potential dangers like short circuits, grounding issues, or damaged insulation. Proper assessments protect users from unexpected problems or dangers, ensuring tools are both efficient and safe for their intended applications. Reliable testing instruments are vital to safety standards.
Climatic Testing
Climatic testing is integral to evaluating how materials and tools perform under different climatic conditions, including shifts in humidity, temperature, and other atmospheric factors. This test simulates a range of environmental scenarios to determine material reliability and durability when exposed to different climatic challenges. The findings are critical for industries where tools and equipment must operate in a range of environmental settings. This ensures that they maintain their integrity and functionality regardless of external conditions. This is crucial for sectors like aerospace, automotive, and outdoor equipment, where consistent performance is paramount.
Compression Testing
Compression testing is critical in determining how materials used in industrial tools react under compressive forces. The purpose of this test is to determine the maximum amount of compressive force a tool material can handle without damage or change in shape. Insights derived from this test are paramount in sectors such as machinery manufacturing, heavy equipment production, and precision tooling, where tools are expected to handle substantial forces and stresses without compromising their functionality or structural soundness.
Dimensional Accuracy Testing
Dimensional accuracy testing ensures that a tool's measurements align precisely with its specified dimensions. This precision is crucial, as even slight deviations can impact tool functionality. Ensuring a tool meets its dimensional specifications guarantees its fit and function in its designated role. Reliable testing solutions are essential for accurate and consistent verification in industrial applications.
Torque Testing
Industrially, certain tools and instruments play pivotal roles in applying or resisting rotational forces. These include motor-driven equipment, drills, wrenches, and specialized gears and shafts. It's crucial that these tools apply the required torque without causing problems. They can also withstand external torques during operation. Failure in either scenario could lead to operational downtime, equipment damage, or safety hazards. Torque testing ensures that these tools function within their specified parameters, providing confidence for operators and technicians.

Corrosion Testing
Corrosion, particularly in outdoor or moisture-rich environments, can damage industrial tools. A material's susceptibility to corrosion can severely limit its operational lifespan, compromise its structural integrity, and lead to structural failure. This necessitates the crucial role of corrosion testing. By assessing how well a tool resists corrosive conditions, manufacturers can ensure their products meet industry standards but also maintain functional efficiency in real-world scenarios.
Thermal Cycling Testing
Thermal cycling testing is a rigorous process that exposes tools to cycles of heating and cooling, assessing their reliability and performance under variable temperature conditions. This test is critical for tools used in environments with extreme temperature variations, ensuring they maintain functionality and structural integrity. Repeated temperature transitions can reveal potential weaknesses or defects in the material or design. Utilizing advanced testing solutions guarantees accurate results, ensuring tools can withstand real-world temperature variations without compromising effectiveness or durability.
Quality Assurance in North American Industrial Tool Craft
As a crucial component of North America's industrial sector, the significance of tools that consistently meet and meet high standards cannot be ignored. Throughout our exploration of quality control methodologies, we emphasize the paramount importance of precision, durability, and reliability. Whether shaping the aerospace sector's future or laying down the foundation for construction, these tools play an instrumental role in ensuring efficiency, safety, and cost-effectiveness.
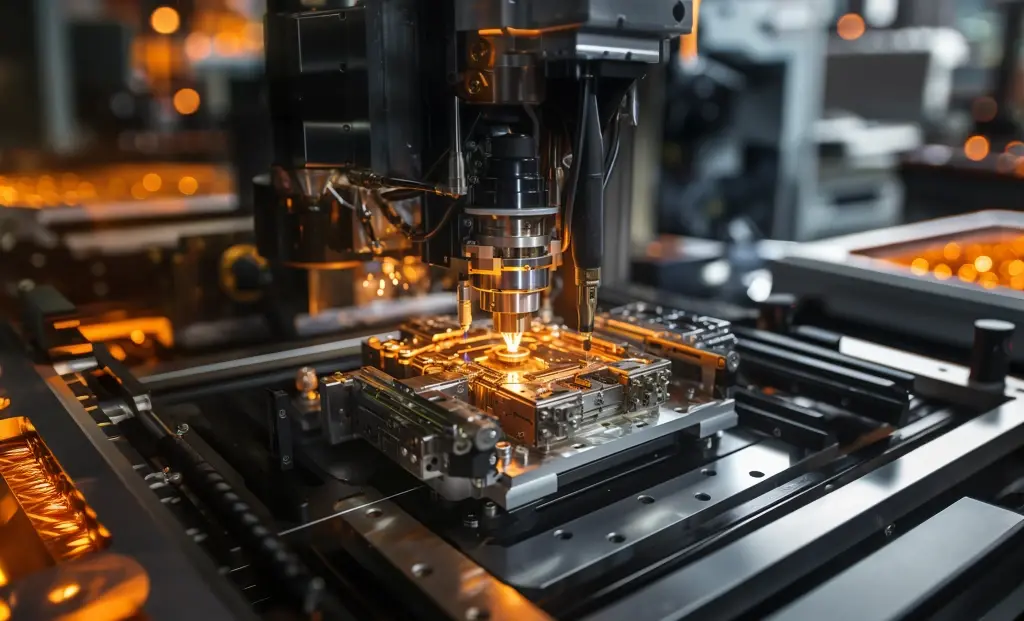
Understanding the importance of quality control processes, like tensile testing, is imperative, as they demonstrate the region's commitment to quality. As the global economy evolves, innovation and competition intensify, and North America's emphasis on meticulous quality testing isn't just about meeting standards—it's about setting them. In the realm of modern tooling, the balance between innovation and quality underscores the foundation for future advancements. In summary, at a time of great potential, dedication to superior quality will distinguish North American industries at the forefront of the international arena.
In conclusion, in a time when industries are rapidly advancing, it's the pursuit of the highest quality, emphasized by various tests from tensile testing to climatic testing, which will lead North American industries forward.