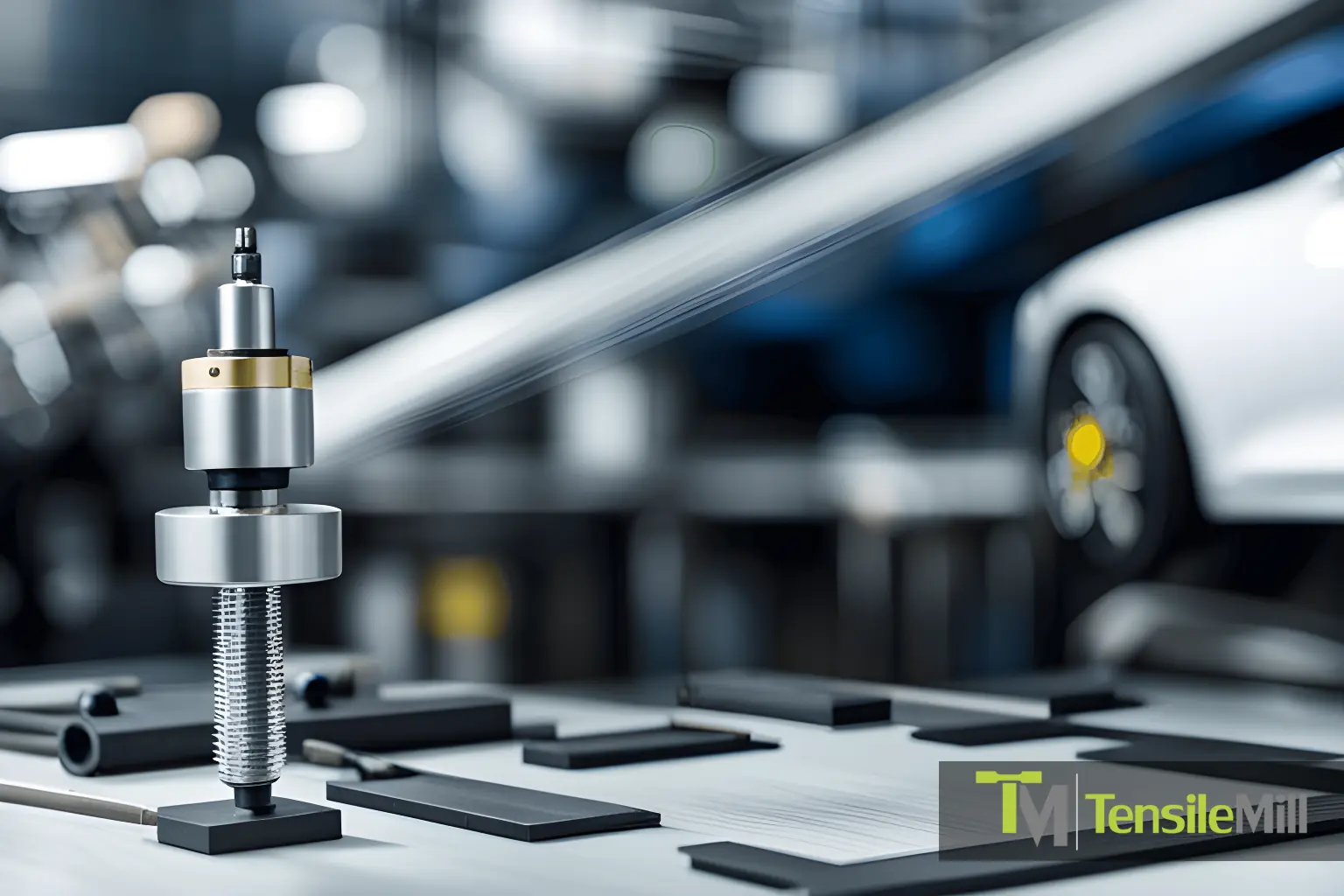
"Until we have established reliability there is no point at all in wasting time trying to make the thing go faster" – Carroll Smith. Who better to know the true value of reliability than a man who has combined successful careers as an amateur racer and a sports car engineer?
Reliability of Cars
In extreme driving conditions, the decisions of the technical team of engineers who take care of the race car are tested like nowhere else. After all, not only the sporting success or failure of a team depends on these decisions, but also the health and life of the pilot, and possibly other spectators and participants.
In the context of the broader automotive market, the importance of reliability is not diminishing. Although ordinary cars are not typically subjected to the stresses of extreme conditions like race cars, a technical error in the development of a production car will cause even more problems when it is replicated.
The most common causes of vehicle failure are listed below in descending order of importance.
- Mechanics: Wear and tear of parts and breakdowns of units are the main cause of vehicle failure. Constant operation, the influence of time, weather conditions and other external factors on the road - all this leads to failure.
- Electricity: A malfunction or interruption in the electrical system causes problems with engine start, lighting, security systems, etc.
- Inadequate fluid levels: Engine oil, antifreeze, brake fluid, or other fluids - can cause damage to the engine or other vehicle systems.
- Fuel system: Incorrect operation of the fuel injection system, contaminated filters or tubes can cause a decrease in engine efficiency and engine failure. The use of low-quality fuel affects engine performance, contaminates the fuel injection system, and causes vehicle malfunctions.
- Improper care and maintenance: Lack of regular maintenance, untimely replacement of oil, filters, spark plugs, etc. can lead to premature consumption of parts and deterioration of the vehicle's performance.
- Design flaws: Less common, but manufacturing defects can lead to problems with the vehicle.
- Tread wear: Insufficient pressure, damage or seasonal incompatibility affect traction, handling and braking. Regularly checking the condition of your tires is an important component of staying safe on the road.
Therefore, the reliability of the mechanics is the first and one of the most important aspects that determines the quality and duration of the car's operation.
Reliability of Mechanics
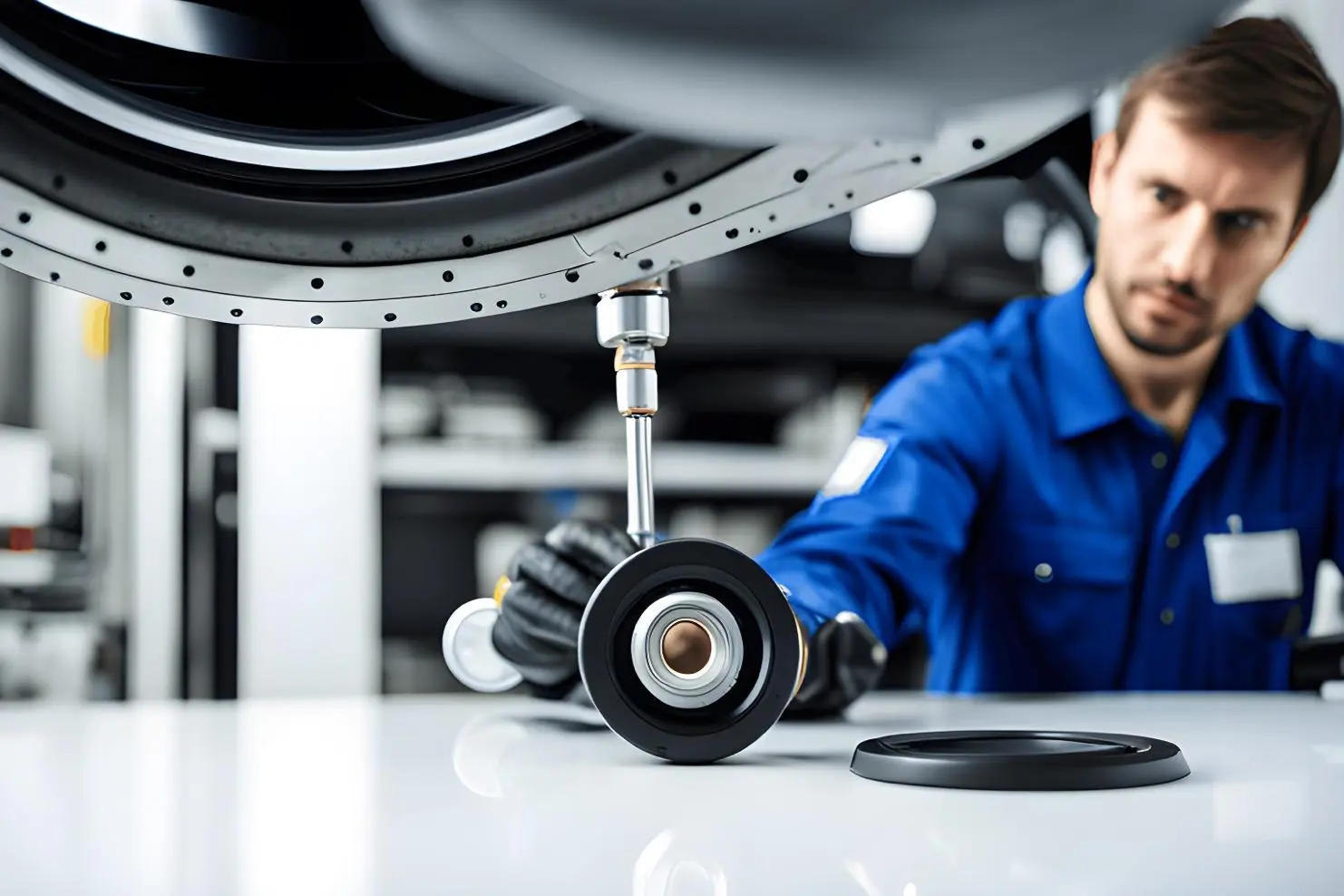
Ensuring the high quality of every part, from engine components to suspension systems, is a critical task for automakers. Flaws in design or manufacturing can lead to malfunctions, accidents, and unreliable vehicle performance. The reliability of vehicle components and assemblies is largely ensured by production quality control. Each vehicle part undergoes a thorough quality control process from the initial development stage to the completion of production.
The production of high-quality parts begins with the selection of appropriate materials. Automakers cooperate with specialized suppliers. This cooperation guarantees the quality and compliance of materials with technical standards.
Tensile testing of materials is an important step in quality control, especially for parts that must be made of high-strength materials. Metal parts are tensile tested to evaluate their ability to withstand the loads and strains that are expected for a particular part during vehicle use.
During production, each part is put through a series of control tests where specialists check for dimensional compliance, shape, and other technical characteristics. Finished components and assemblies are subjected to functionality tests to ensure that they work properly and meet specified standards.
Individual engine parts are subjected to durability testing to assess their ability to operate continuously over a long period of time. In such experiments, tensile tests may be performed before and after prolonged loading of the metal parts, which allows the impact of metal fatigue to be assessed for a particular part.
After the parts are manufactured and the vehicle is assembled, control tests are carried out again to ensure that all components maintain a high standard of quality. Control tests of vehicles are carried out in conditions very close to those of actual use.
This comprehensive approach to quality control allows automakers to ensure that their vehicles' mechanicals are highly reliable. Going back to where we started, reliability is a basic characteristic that maintains the safety and satisfaction of the car owner, as well as guarantees a long service life, and thus ensures the success of the automotive manufacturer.
Robust Reliability in the Automotive Industry
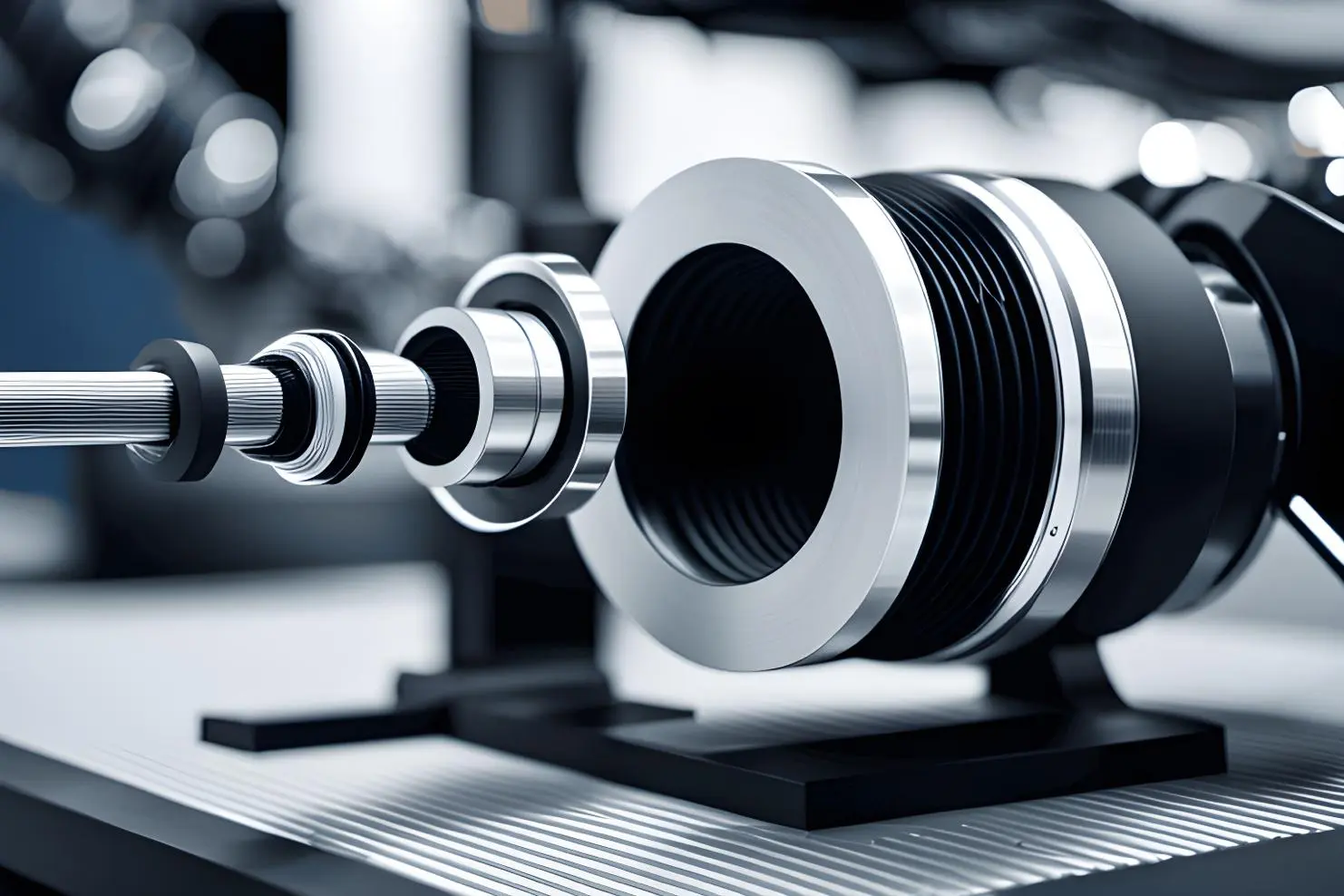
Car manufacturers are faced with the requirement to create structures that provide maximum strength and safety for passengers. Strength is the ability of a material to resist irreversible deformation and fracture under the influence of loads or other factors. Loss of strength or exceeding its limit value leads to the destruction of the material and parts or structure.
Tensile testing allows us to assess the strength of metal materials and their ability to withstand loads without breaking, while maintaining their shape. The results of tensile testing help engineers improve vehicle design and select the most appropriate materials for specific parts. This can help reduce the weight of the vehicle, thereby improving its efficiency and reducing fuel costs.
As for the tensile testing process, it usually involves the following steps:
- Selection of sample: Material samples are taken from key parts that are subject to the greatest stress during operation or those on which the integral integrity of the entire unit and its functionality directly depend.
- Sample preparation: Material specimens for tensile testing are machined, usually using milling or lathes. Given the strict need to adhere to a specific standardized specimen size and shape, program-controlled machines are best suited for this purpose. Their use avoids operator influence on the measurement results and helps to obtain reliable data on the strength of materials.
- The shape of the tensile specimens is dictated by standards and requirements depending on the type of test being performed. Two types of specimens are most commonly used for tensile testing of metals in the automotive industry: flat and round.
- Flat specimens are often used for tensile testing, where the goal is to evaluate the strength and deformation behavior of a material. These specimens are rectangular or flat, and they are stretched along the length of the specimen. Most flat specimens are made from parts that are flat themselves, such as car body parts, aluminum and other profiles. Such tests allow measuring stress, strain, and elastic modulus of the material, as well as determining the strength limits of materials and products.
- Round samples are made from three-dimensional parts such as driveshafts, levers, springs, and other suspension components, as well as engine components, beams, and struts. These parts are usually made of strong steel grades, as they provide structural strength at critical junctions not only due to the strength of the construction material but also due to the thickness of the product. That's why round specimens are used in such cases – so the thickness of the part can also be optimized in such tests, especially when it comes to evaluating the strength and behavior of the material under radial loads.
- Standardization of conditions: Flat and round specimens have certain standards for size and shape to ensure uniform testing conditions, which also makes the results comparable. The same applies to the load applied to the specimens – it has defined values and is applied with a certain increase until the specimen breaks.
- The correct fixation of the specimens in the testing machine also has a decisive influence on the results. The specimens are fixed in the clamps of the tensile machine with their expanded ends, while the tensile force and subsequent tearing occur in the narrower part of the specimen.
- Testing: Specimens are gradually loaded with increasing loads until they fracture or deform. Changes in the geometry of the specimen are observed during the test, which is then used to analyze the results.
- Analysis of results: Using the observed data, the deformation parameters are calculated and the strength characteristics of the material are determined. Next, they are compared with the parameters previously obtained for other samples or with standard characteristics known for a particular material.
The key to obtaining reliable tensile test results is to follow test standards and protocols to ensure repeatability and accuracy, and to use high-quality measuring equipment designed specifically for tensile testing. In addition, specimens must be presented in accordance with geometric and material characteristics to ensure correct testing. Engineers must be careful in selecting test parameters to ensure that the results are correct and relevant to real-world vehicle conditions.
The Best Tensile Testing for Quality Control
Summarizing the above, we can conclude that the reliability of cars is based on three main principles:
- reliability of every detail of the car;
- reliability of all components and mechanisms, their proper interaction;
- reliability of the user and maintenance workers.
In turn, the first point can only be fulfilled if a reliable quality control process for incoming materials and manufactured parts is implemented in automotive production. Not the only, but one of the key aspects of such control is checking the strength of parts that are subject to mechanical stress during vehicle operation. This is done through tensile testing. Thus, ensuring the reliability of such testing is the key to the safety of vehicle use.
Today, TensileMill CNC Inc. supplies the North American market and around the world with the high quality equipment needed to control product quality through tensile testing of materials. The company has earned a good reputation among industrial manufacturers and government quality control laboratories as a recognized manufacturer of tensile sample preparation machines. Recently, it has started to supply tensile testing equipment that meets all the latest international industry standards. Therefore, we now provide a full range of tensile testing equipment for quality control.
- Tensile Testing Equipment – load range from 1 to 3000 kN. Contact our consultant for full information about the new equipment!
According to the company's philosophy, the new tensile testing equipment is designed with the practical experience of our many customers from quality control laboratories and research departments of enterprises in manufacturing industries. Therefore, we offer systems that use CNC control with a user-friendly interface and touch screen. Our engineers have done their best to give you the most accurate test results in the easiest way possible with minimal room for error!
As before, you can find a description and order the already well-established Flat Specimen Preparation Equipment Lineup, which currently includes two items, on the company's website:
- TensileMill CNC MINI – Flat Specimen Preparation
The compact system for production of “dog bone” samples retains virtually all the essential functions required to meet most testing laboratory needs without using much workspace. It is ideal for small space requirements. The machine can also prepare virtually all types of flat tensile specimen standards and has a full range of versatile CNC machining capabilities. Despite its small size, the MINI is capable of handling high volumes of tensile specimen preparation and hardness values of up to 60 HRC. This means that it can handle virtually all materials from Plexiglas to most metals up to high carbon and stainless and ultra-hard tool steels, as well as carbides such as tungsten carbide (WC), tantalum carbide (TaC) and titanium carbide (TiC), and high-hardness ceramic materials such as aluminum oxide (Al2O3) and silicon carbide (SiC).
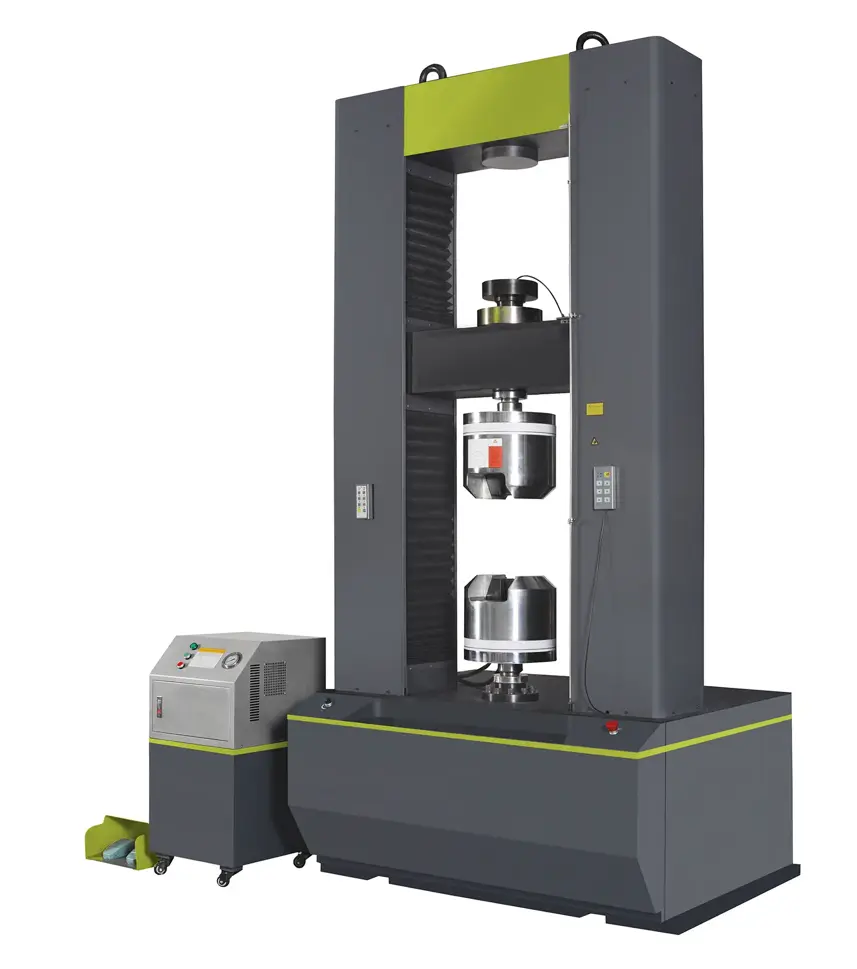
No need to waste time measuring and matching dimensions to the required standards, our powerful Carbon software with a user-friendly interface allows the operator to quickly find the desired tensile specimen size in a library of standards that includes ASTM, ISO, DIN, JIS and other industry standards. Simply start the appropriate fabrication program and the machine will start milling in seconds.
- TensileMill CNC XL – Flat Specimen Preparation
The TensileMill CNC XL is an updated and expanded flat specimen system that is a dynamic addition to the test equipment of quality control laboratories. The increased stroke distance, servo power, and updated software will meet your needs for preparing large quantities of tensile specimens in particularly strong materials.
The TensileMill CNC XL is therefore more powerful than both the MINI (see above) and the Classic (currently discontinued). XL has a larger frame, the machine is able to handle tougher materials and produce larger tensile specimens. The automatic tool changer allows for consistent production of samples from materials of different strengths without stopping the process and operator intervention. The machine is therefore capable of 24/7 operation, continuously supporting high productivity production, which is especially important for the automotive industry.
As for the TensileTurn CNC – Round Specimen Preparation line of machines, it includes three positions that cover all possible tensile specimen production needs of automotive manufacturers.
This is a software-controlled automatic CNC lathe in a conveniently sized machine tool designed to prepare precision circular tensile specimens with diameters up to 2 inches (~60 mm) and lengths up to 16 inches (~406 mm). Standard sample sizes according to ASTM, ISO, DIN, etc. are already in the system - so programming the machine is done with a few taps on the machine's touchscreen control. The workpieces can be rectangular, round or irregular in shape, and the machine will process them according to the specified dimensions.
Round tensile specimens, smaller specimens, tensile specimens with threaded ends, and push-button head rods are no problem, as is preparing specimens for fatigue testing and more! The operator simply needs to load a round, square or irregular example into the machine. With automatic machines from TensileMill CNC Inc. tensile specimen production becomes very easy and precise, regardless of the hardness and strength of the materials under test.
The machine differs from the previous one in terms of maximum sample sizes: the maximum sample diameter for the TensileTurn CNC - Industrial Upgrade is 5 inches (127 mm) with a maximum length of 8 inches (~203 mm).
While the model
- The TensileTurn CNC XL – Heavy Duty Round Specimen Preparation is designed for large specimens with diameters up to 450 mm (~18 in.) and lengths up to 550 mm (~22 in.).
To summarize, TensileMill CNC Inc. has been operating on the market for 5 years as a supplier of high-end tensile testing equipment, and has already established itself as a reliable partner for many of our customers in the automotive industry. We are proud that our equipment is responsible now for the quality of many of the vehicles that provide comfortable and safe transportation for many people in North America and around the world.